Fuel cell technologies have taken the BP industry by storm for quite some time. But what is a fuel cell, what is the design of fuel cell stack in bipolar plates and why is it so essential? In other words, fuel cells are electrochemical devices that convert hydrogen and oxygen into electricity while producing water as the only waste. There is no waste pollution into the environment – ​​just clean energy. As the emphasis on minimizing the carbon footprint continues to grow, so do the prospects of fuel cells for power generation.
Structure of Fuel Cell Stacks
A single fuel cell unit by itself can produce a small amount of energy. This is what the fuel cell stack is designed for. It is a combination of several cells placed on top of one another to create enough energy for anything from electric cars to standby power systems. To charge up galvanic batteries let’s say one can stack them one over the other. The fuel cell stack building up batteries does the same only that it’s efficient.
The stack is basically the heart of the power system. Each cell in the stack has an anode, a cathode and an electrolyte. Nonetheless, it is the design of the stack which allows power generation on a large scale, and among such structures are the bipolar plates.
The Role of Bipolar Plates in Fuel Cells
What Are Bipolar Plates?
There are hardly any gainsayers about the fact that bipolar plates are the workhorses of fuel cells but they do not always get the credit they deserve. They are interposed between the individual fuel cells mounted in any given stack, which is a lot. These plates not only assist in the even partitioning of gaseous fuels like hydrogen and oxygen on the surfaces of the cells but also gather the electric more.
Key Functions of Bipolar Plates
- Gas Distribution : These components ensure that each active side of the cell (anode or cathode) receives hydrogen or oxygen sufficiently and hence the reaction takes place uniformly.
- Current Collection: These plates are also integral in the electrical connections as they allow the electricity from a cell to be conducted or moved to another cell.
- Heat Management: A considerable amount of heat is produced and bipolar plates come into play in heat management to improve efficiency.
- Structural Support : Last but not the least, they provide the required support to be able to hold the stack and all or its components together.
Material Choices for Bipolar Plates
The material used for bipolar plates is one of the factors that influence the functional efficacy and lifetime service of a fuel cell rather much. Let us now look into the three most commonly occurring types.
Graphite Bipolar Plates
When it comes to fuel cells, graphite has been the first material for bipolar plates – why? Because the major drawback in a fuel cell, the scarcer of the two types of connectors, is fuel cell corrosion, due to a very acidic environment.
Advantages and Disadvantages of Graphite Bipolar Plates
Out of all graphite’s performance characteristics and manufacturing characteristics, thermal and electrical conductivity, and particle size are most likely indispensable. That being said, there is no silver lining. The brittle nature of graphite plates necessitates complex machining, often rendered in fragile and costly structures . Though corrosion resistance is remarkably satisfactory, mechanical properties tend to be less appealing.
Metal Bipolar Plates
Bipolar metal plates are widely used, more so in heightened following demand for their strength and durability. In addition, they are much thinner than graphite plates allowing a compact and lightweight fuel cell stack.
Advantages and Disadvantages of Metal Bipolar Plates
A further downside of metallic plates is their comparative advantage of increased mechanical strength and better ionic and electronic conductivity, which might be offset by the problem of corrosion. On this matter, coatings have been developed and some of them are applied by manufacturers but at the expense of adding the costs without the necessity. Nevertheless, such coatings may even increase costs and sometimes lead to performance degradation.
Composite Bipolar Plates: A Balance Between Metal and Graphite
Reinforced panoramic plates want to take advantage of the best of both possibilities. It is in that they incorporate both metalliferous and non metalliferous components to form lightweight, rigid and rust proof plates.
Performance and Benefits
Composite plates are more durable than graphite and than metals, more resistant to corrosion. Plus, they’re easier to manufacture and less expensive, making them a promising option for future fuel cell designs.
Design Considerations for Bipolar Plates
In developing the bipolar plates, there are certain engineering principles. Those should be used so that the performance and efficiency is enhanced to the maximum.
Structural Requirements
Bending of the plates is required while one is stacking them but at the same time they should not be too bulky to make the fuel cell bulky.
Weight and Thickness
Weight reduction of the fuel cells stacks is made possible when thinner plates are adopted which is important in cases like that of electric vehicles. However there is consideration that has to be made to the thickness and the strength.
Fluid Flow Channels and Heat Management
Role of Fluid Channels in Performance
The fluid channels on the surfaces of the bipolar plates are important especially in the introduction, distribution of gasses and water inside the cell. However some designs of the channels enable flow of gasses evenly to help in the power constant output.
Managing Heat and Pressure
Fuel cells normally do produce too much heat which if not managed will exacerbate the inefficiencies so often experienced other than of heat management alone. Bipolar plates also act to control the heat and the gasses that build up pressure inside the cell for maximum performance.
Corrosion Resistance and Durability in the Bipolar Plates
Typical Corrosive Circumstances
This is no less so for the metal bipolar plates, where corrosion is more pronounced damage. The acidic environment in the fuel cell can degrade the plates over time, leading to reduced performance and even failure.
Strategies for Longevity
Applying protective coatings, like graphite or polymer layers, can be beneficial in enhancing the life of the bipolar plates by reducing corrosion. The other thing is that the manufacturers are always looking for new materials to enhance durability.
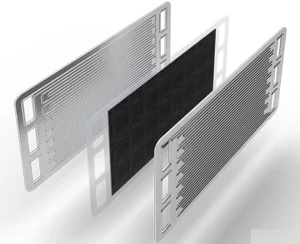
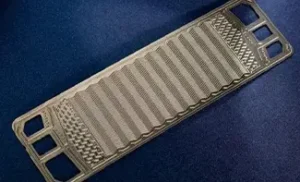
Manufacturing knows how of the Bipolar Plates
There are several available procedures for manufacturing bipolar plates, though none is without its demerits.
Compression Molding
This technique is most pertinent in respect to graphite plates. It involves molding of the material under pressure with the help of a machine. It is effective, although it tends to be long and expensive.
Stamping Techniques
By using thin sheets of metal, metal plates are usually stamped out – a quicker and less expensive process. But stamping also requires special tools, and any mistakes will lead to a wrong stamped product.
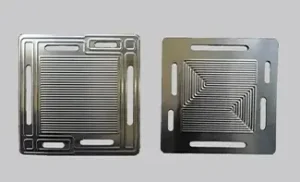
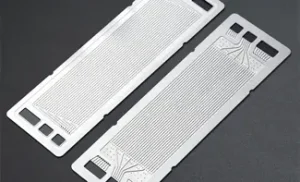
Advances in Manufacturing Technologies
Recent Technological Innovations
In the last couple of years or so, there have come new ways of manufacturing bipolar plates due to the advancement of a particular technology, 3D printing. This way, it makes it possible to make more complex patterns and quicker pattern making which might end up cutting the price.
3D Printing of Bipolar Plates
3D printing has the capability to help embed forms of structure and arrangement that was hardly realized in traditional manufacturing processes. Instead of using wires, fluid passages and other structures can be made with more precision.
Difficulties Encountered In The Design Of Fuel Cell Stack in bipolar plate
Cost Factors
Fuel cell systems have an impressive efficiency but remain expensive to manufacture, with bipolar plates being one of the items driving that cost up. The goal of cutting down on the cost of the materials and the manufacturing processes of the fuel cell systems is paramount.
Scalability and Efficiency
With technological advances came the demand for more fuel cells which would require more production expansion possibilities. Striking the right balance between efficiency and durability of the system remains a puzzle that manufacturers are still grappling with.
With specialized services on key components and microscopy of thin film devices, TMN offers custom services of X-ray etching with ultrahigh-precision to control processing parameters. The company employs over 100 people including engineers and chemists with qualification and is capable of providing various custom photochemical etching services. Faced with this challenge, TMN consists of a corporation aimed at creating highly innovative photochemical etching technologies. They expect tighter tolerances, improved accuracy, better functionalities and thinner components. As a result, TMN provides specialized technical support to the customers of the bipolar plate which has been well received by the clients without any objections.
TMN has foreign trade experience of more than ten years focusing on import and export. TMN’s custom-etched metal bipolar plates are sold abroad in the UK, USA, Switzerland, Hungary, Germany, Estonia, Latvia, Czech republic, India and Saudi Arabia who are customers for research and manufacturing of fuel cell stacks and water electrolyzers. Also, upon delivery, we are in a position to supply the appropriate documentation and COC certificates for purposes of customs clearance and inspection.
Contact Lydia.sales1@tmnetch.com or visit Facebook page for more information.
Detailed Explanation of the Structure and Principle of Proton Exchange Membrane Fuel Cells