1. Basic Principles of Proton Exchange Membrane Fuel Cells
Proton exchange membrane fuel cells, also known as polymer electrolyte fuel cells, are a type of low-temperature fuel cell that operates at relatively low temperatures (typically below 100 degrees Celsius). This makes them highly versatile in their applications, ranging from powering vehicles to providing backup power for critical infrastructure. They were first developed by General Electric in the 1960s and later used in America’s first manned spacecraft.
Note: Learn about the development history of fuel cells.
1.1 Components of Proton Exchange Membrane Fuel Cells (PEM)
PEMFC consists of core components such as the proton exchange membrane, catalyst electrode layer, gas diffusion layer, and bipolar plate. The gas diffusion layer, catalyst electrode layer, and polymer electrolyte membrane are fabricated into a membrane electrode assembly through a hot-pressing process.
The proton exchange membrane at the center of the membrane electrode assembly serves multiple roles: conducting protons (H+), preventing electron transfer, and isolating the reactions at the anode and cathode. The catalyst electrode layers on both sides of the proton exchange membrane are where the fuel and oxidant reactions occur. The outermost gas diffusion layer supports the catalyst electrode layer, stabilizes the electrode structure, provides gas transport channels, and improves water management.
The bipolar plates consist of anode and cathode plates, clamping the membrane electrode assembly in the middle. Their main functions are to separate the reactive gases, guide the reactive gases into the fuel cell through flow fields, collect and conduct current, support the membrane electrode assembly, and handle the fuel cell’s heat dissipation and water management.
1.2 Working Principle of Proton Exchange Membrane Fuel Cells (PEM)
After understanding the structure of PEMFC, we can better comprehend its working principle: When the fuel (H2) enters the anode plate, it diffuses to the surface of the anode catalyst. Under the action of the anode catalyst, it decomposes into positively charged protons and negatively charged electrons. The protons pass through the proton exchange membrane to the cathode, while the electrons flow to the cathode through an external circuit and load. Meanwhile, O2 diffuses to the surface of the cathode catalyst. Under the action of the cathode catalyst, electrons, protons, and O2 undergo an oxygen reduction reaction (ORR) to form water. The electrode reaction formulas are as follows:
Anode (oxidation reaction): 2H2→4H++4e– E0=0V(us.RHE)
Cathode (reduction reaction): O2+4H++4e–→2H2 E0=0V(us.RHE)
Overall reaction:O2+2H2→2H2O E0=0V(us.RHE)
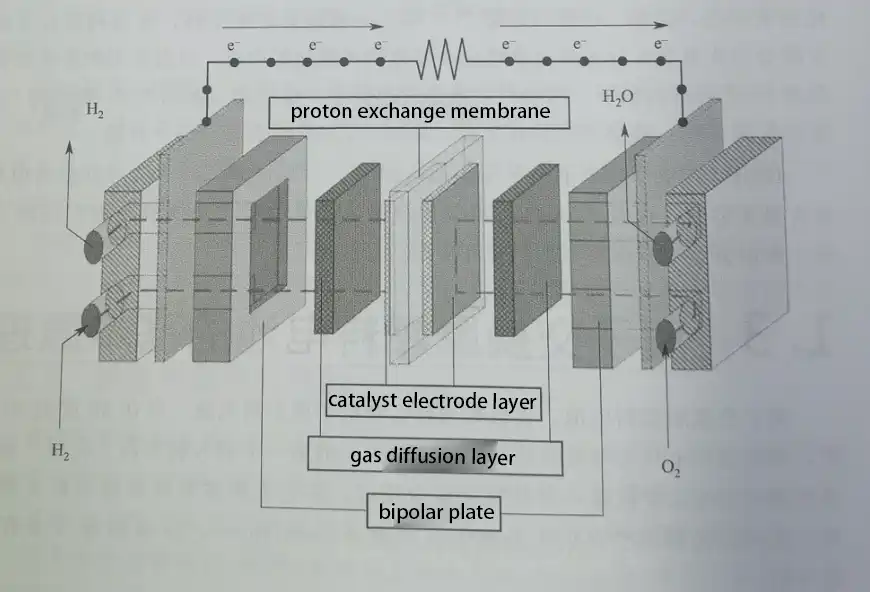
1.3 Cost Proportion in Fuel Cells
The cost proportions in fuel cells are as follows: electrocatalyst (46%), proton exchange membrane (11%), and bipolar plate (24%). Due to the extensive use of precious metal platinum in the electrocatalyst, its cost accounts for nearly half of the total cost of the fuel cell. Therefore, high-performance, high-durability, and low-cost new materials for proton exchange membrane fuel cells are currently the focus of research in this field.
2. Components of Proton Exchange Membrane Fuel Cells
In the above diagram, besides the basic chemical reaction principles of fuel cells, important components are also involved: the membrane electrode assembly (MEA) and bipolar plate. The MEA includes the proton exchange membrane, gas diffusion layer, and catalyst electrode layer. There are two common MEA fabrication techniques: one is to evenly spray the catalyst onto the gas diffusion layer, known as a gas diffusion electrode (GDE); the other is to evenly spray the catalyst onto the proton exchange membrane, known as a catalyst coated membrane (CCM). Using the CCM technique can reduce the amount of precious metal used.
With this brief introduction, you now have a basic concept of proton exchange membrane fuel cells. Next, we will introduce each of these components in detail.
2.1 Catalyst Electrode Layer Materials for Proton Exchange Membrane Fuel Cells
The catalyst electrode layer is typically prepared from an electrocatalyst and a proton exchange resin solution. It is a thin, porous structure with electrochemical activity for hydrogen oxidation or oxygen reduction. The thickness of the catalyst electrode layer is generally between 5 and 10μm. The electrocatalyst is one of the key materials in fuel cells. Its function is to reduce the activation energy of the reaction, promote the redox process of hydrogen and oxygen at the electrodes, and increase the reaction rate.
2.1.1 Platinum Loading in the Catalyst Electrode Layer
Currently, the platinum loading in the catalyst electrode layer of PEMFCs is relatively high. Fuel cell vehicles require about 50g of Pt per car and 100g per bus. Balancing the cost and performance of fuel cells while reducing Pt usage is a significant challenge. For PEMFCs operating under acidic conditions, the hydrogen oxidation reaction (HOR) at the anode has a very low overpotential, allowing it to operate at very low platinum loadings (0.05mg/cm²) without significant energy loss. The oxygen reduction reaction (ORR) at the cathode, however, has a low exchange current density and is the rate-limiting step of the overall fuel cell reaction.
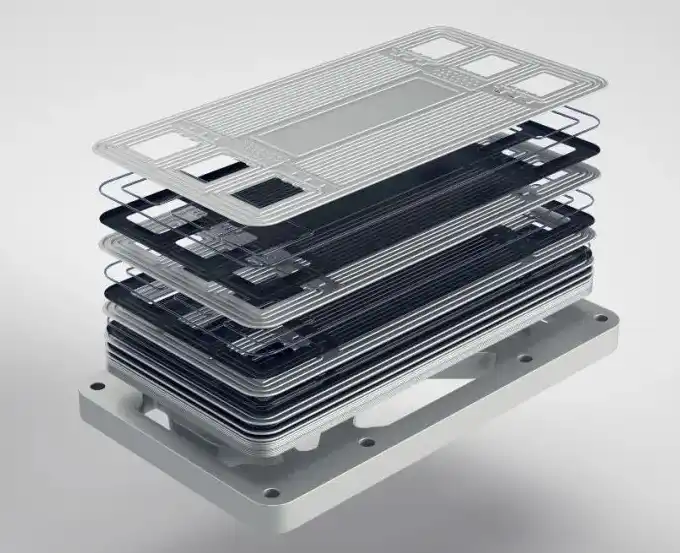
2.1.2 The Process of Cathode Oxygen Reduction Reaction
The oxygen reduction reaction (ORR) at the cathode is complex, with many intermediate products, and its reaction efficiency is far lower than that of the anode fuel oxidation reaction. The complexity of the ORR at the cathode causes significant current efficiency losses in low-temperature fuel cells, with the efficiency loss from this process accounting for up to 80% of the total efficiency loss of the cell. Therefore, researching highly active and stable ORR electrocatalysts is crucial for advancing the large-scale commercialization of fuel cells.
2.1.3 Cathode Electrocatalysts in Proton Exchange Membrane Fuel Cells
In proton exchange membrane fuel cells, the commonly used cathode electrocatalyst is commercial Pt/C electrocatalyst, which consists of 3-5 nm Pt nanoparticles. The 40% (mass fraction) Pt/C electrocatalyst produced by Johnson Matthey (JM) has a mass activity (MA) of 0.21 A/mg and a specific activity (SA) of 0.32 mA/cm² at 0.9V (vs. RHE), which is far below the US Department of Energy’s (DOE) 2025 targets (MA@0.9V vs. RHE: 0.44 A/mg; SA@0.9V vs. RHE: 0.72 mA/cm²).
2.1.4 Platinum Usage in Fuel Cells Needs Further Reduction
The high cost of platinum limits the large-scale commercialization of fuel cells, as discussed in several other articles. Although the current platinum usage has been reduced from 0.8-1.0g/kW ten years ago to 0.3-0.5g/kW now, there is still a desire to further reduce it to achieve the levels used in traditional internal combustion engine exhaust purifiers (less than 0.05g/kW). Recently, there have been reports that the first fuel cell with platinum usage as low as 0.1g/kW is about to be developed.
2.1.5 Stability of Platinum in the Catalyst Electrode Layer
In addition to the constraints of cost and resources, platinum catalysts also face stability issues. Through the analysis of fuel cell degradation mechanisms, it is evident that catalysts degrade during vehicle operation. For instance, under dynamic potential, Pt nanoparticles can agglomerate, migrate, and dissolve. High potentials caused by hydrogen-air interfaces during open circuit, idling, and start-stop processes can lead to the corrosion of the catalyst’s carbon support, resulting in catalyst loss. Therefore, given the cost and durability issues of current commercial catalysts, researching new, highly stable, highly active low-Pt or non-Pt catalysts is a current hotspot.
2.1.6 Known Methods for Reducing Platinum Usage
Common methods for reducing platinum usage and improving catalyst activity and stability include doping transition metal elements to form alloys through crystal structure regulation and creating special structures (such as core-shell structures). There has also been some progress in the field of non-precious metal catalysts.
2.2 Electrolyte Membrane
As a key component of proton exchange membrane fuel cells (PEMFC), the main functions of the electrolyte membrane include: separating the fuel and oxidant, supporting the electrocatalyst, and ensuring the smooth progress of the reaction; selectively conducting protons while blocking the transmission of electrons. The performance of the proton exchange membrane significantly impacts the performance, lifespan, and cost of PEMFCs. Based on the usage conditions of PEMFCs, an excellent electrolyte membrane material should have high proton conductivity, good chemical stability, good thermal stability, good mechanical properties, low gas permeability, low water electro-osmotic drag coefficient, low cost, and be easy to form and process.
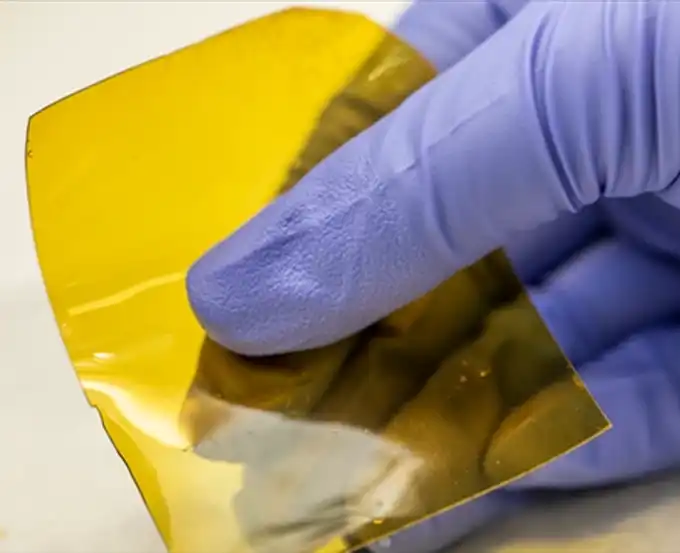
2.2.1 Different Types of Proton Exchange Membranes
To meet the requirements for the commercialization of fuel cells, scientists have conducted extensive research on different types of proton exchange membranes.
2.2.1.1 Perfluorosulfonic Acid Proton Exchange Membranes
Perfluorosulfonic acid proton exchange membranes were the first to be used in PEMFCs. However, these membranes have a fatal flaw: their performance declines sharply due to degradation during actual use, leading to their temporary suspension. It wasn’t until the 1960s that DuPont in the United States developed a new perfluorosulfonic acid proton exchange membrane (Nafion membrane), which has both excellent stability and high proton conductivity, making it renowned worldwide and still widely used today.
Nafion membranes have multiple advantages, such as good chemical stability, high mechanical strength, high conductivity under high humidity, high current density at low temperatures, and low proton conductive resistance.
However, they also have drawbacks, such as poor proton conductivity at medium to high temperatures, high requirements for temperature and water content, excessive methanol permeability when used in direct methanol fuel cells, the difficulty of synthesizing and sulfonating perfluoropolymers, difficulty in forming films, and high cost.
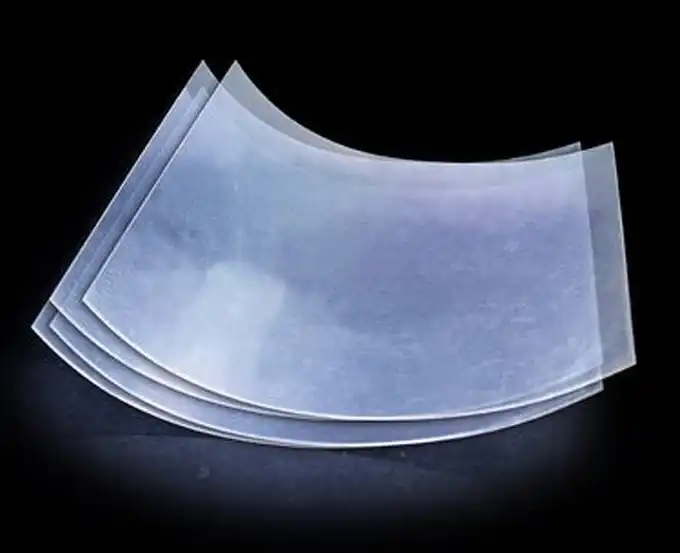
2.2.1.2 Partially Fluorinated Proton Exchange Membranes
Due to the high and persistent cost of perfluorosulfonic acid proton exchange membranes, many scientists have researched partially fluorinated and non-fluorinated proton exchange membranes to reduce costs and address the challenges of synthesizing perfluoropolymers.
Partially fluorinated proton exchange membranes use partially substituted fluorides to replace perfluorosulfonic acid resins or blend fluorides with inorganic or other non-fluorinated materials to create membranes. Non-fluorinated proton exchange membranes are essentially hydrocarbon polymer membranes. As fuel cell membrane materials, they are inexpensive, easy to process, and have good chemical stability and high water uptake. Studies have also indicated that sulfonated polysulfone, polyethersulfone, and polyether ether ketone can be used to make proton exchange membranes. The research challenge lies in balancing proton conductivity with mechanical strength and extending their lifespan.
2.2.1.3 Composite Proton Exchange Membranes
To address the high cost, difficult synthesis of raw materials, and complex production processes of perfluorosulfonic acid proton exchange membranes, various composite proton exchange membranes have gained increasing attention from researchers. The advantages of composite proton exchange membranes include improved mechanical strength in dry states and dimensional stability in wet states, as well as reduced thickness.
Composite membranes can be made by combining perfluorinated non-ionic microporous media with perfluorinated ion exchange resins. The perfluorinated ion exchange resin forms proton transport channels within the micropores, maintaining the proton conductivity of the membrane, improving its properties, and enhancing its mechanical strength and dimensional stability.
Additionally, adding other fillers can enhance certain properties of proton exchange membranes. For example, Nafion membranes with sulfonated zirconia added show improved proton conductivity and water retention capacity under low humidity. Composite membranes with sulfonated graphene oxide (SGO) added exhibit significantly reduced gas permeability, but due to the poor interlayer proton conductivity of sulfonated graphene oxide, the overall proton conductivity of the composite membrane is greatly reduced.
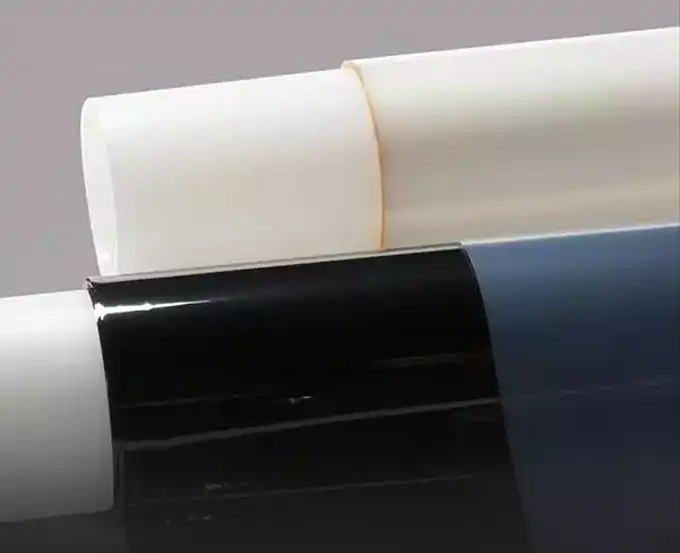
2.3 Gas Diffusion Layer
The gas diffusion layer (GDL) is located between the flow field and the catalyst layer. Its main functions are to provide transport channels for the reacting gases and the produced water and to support the catalyst. Therefore, the performance of the GDL substrate material directly affects the performance of the fuel cell. A high-performance GDL must have good mechanical strength, appropriate pore structure, good electrical conductivity, and high stability.
2.3.1 Composition of the Gas Diffusion Layer
The gas diffusion layer is usually composed of a porous carbon fiber substrate and a microporous layer. The porous carbon fiber substrate is often hydrophobically treated porous carbon paper or carbon cloth, with a thickness of 200-400 μm. The microporous layer, also called the water management layer (approximately 100 μm), typically consists of conductive carbon black and a binder. Its function is to reduce the contact resistance between the catalyst layer and the support layer, ensure uniform redistribution of the reactant gases and product water between the flow field and the catalyst layer, enhance conductivity, and improve electrode performance.
2.3.2 Function of the Gas Diffusion Layer (GDL)
The GDL distributes the reactant gases over the electrode and conducts electrons and heat between the electrode and the bipolar plate. More importantly, the GDL plays a critical role in the water management of the fuel cell. This is because the proton exchange membrane in the membrane electrode assembly needs to conduct protons under humid conditions, while excess water can cause flooding of the electrodes. Thus, the GDL must balance the appropriate amount of water present on the electrode surface.
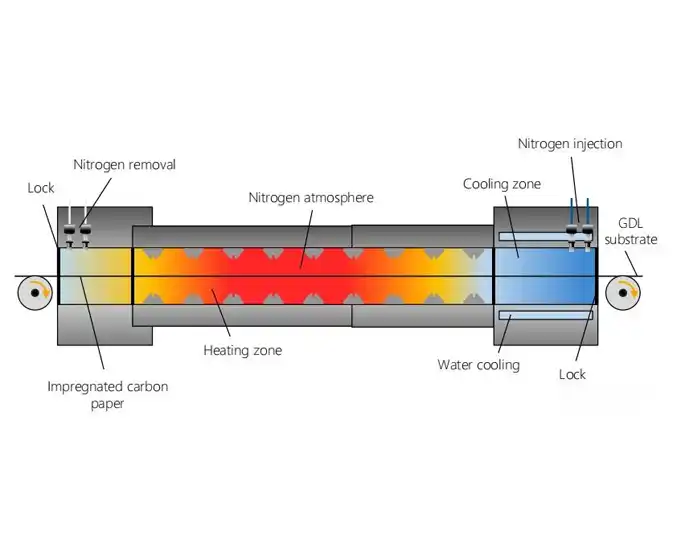
2.3.3 High-Performance Gas Diffusion Layer
A high-performance GDL can directly improve the working performance of the fuel cell. What constitutes high performance? It must meet the following requirements:
Corrosion resistance: The GDL is in direct contact with the catalyst layer and is subject to high electrochemical corrosion during reactions.
Porosity and breathability: The GDL must be a porous, breathable material, as it mediates the diffusion of hydrogen/oxygen or methanol/air to the catalyst layer.
High electrical conductivity: Since the GDL conducts electrons, it must have high electrical conductivity.
High thermal conductivity: Electrochemical reactions are exothermic, and excessive heat can damage the proton exchange membrane. The GDL must be able to conduct heat away to prevent damage to the proton exchange membrane.
High hydrophobicity: Water produced during fuel cell reactions can degrade performance. Therefore, the GDL must be able to expel water effectively.
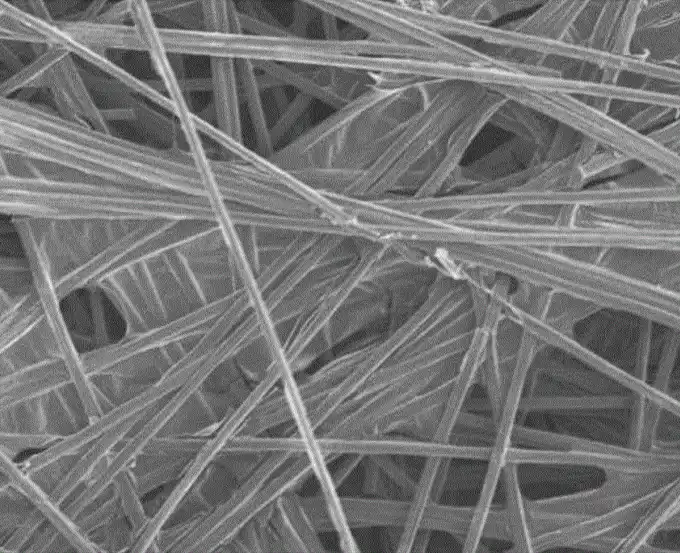
2.4 Bipolar Plate
The bipolar plate is a crucial component of a proton exchange membrane fuel cell (PEMFC). It features channels on both sides: one side contacts the anode of one cell to provide the anode flow field, and the other side contacts the cathode of another cell to provide the cathode flow field. Typically, the water channels are isolated from the anode and cathode flow channels within the bipolar plate. The bipolar plate serves functions such as collecting and conducting current, separating gases, supporting the cell stack, and connecting individual cells in series.
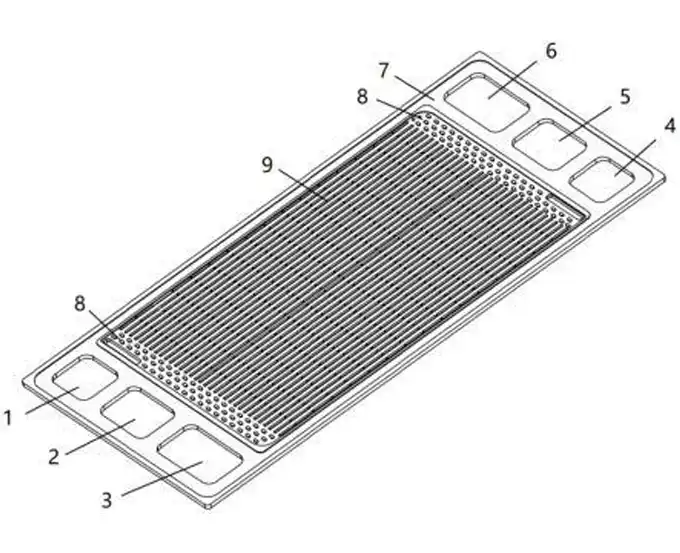
2.4.1 Structure of the Bipolar Plate
The bipolar plate accounts for 70%-80% of the cell’s mass, and the cost of machining graphite flow field plates constitutes 60%-70% of the total cell stack processing cost. The structure and size of the flow channels significantly affect cell performance. Therefore, the design and structure of the bipolar plate have a substantial impact on the cell stack. Current research on bipolar plates mainly focuses on material selection to meet the technical requirements for fuel cell commercialization.
Note: Impact of bipolar plate flow channels on fuel cell performance
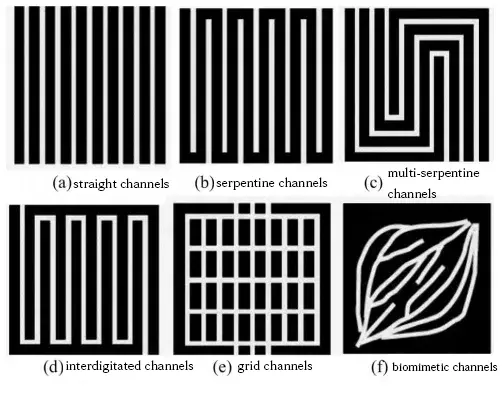
2.4.2 Types of Bipolar Plates
Given the functionality and importance of bipolar plates in the cell stack, their materials must satisfy conditions such as high electrical conductivity, high mechanical strength, low hydrogen permeability, high stability, corrosion resistance, low cost, ease of manufacture, and lightweight. Based on the material, bipolar plates can be broadly categorized into three types: graphite bipolar plates, metal bipolar plates, and composite bipolar plates.
2.4.2.1 Graphite Bipolar Plates
Graphite bipolar plates are one of the earliest developed bipolar plate materials. They have characteristics such as low density, good electrical conductivity, and chemical stability, which can meet the requirements for long-term stable operation of fuel cells. However, during the production of graphite bipolar plates, pores can easily form. The deformation of graphite plates during the high-temperature graphitization process makes it difficult to precisely control the dimensions of the bipolar plates. Therefore, to achieve the required mechanical properties, the volume and mass of the graphite bipolar plates have to be increased, making graphite difficult to process and resulting in high processing costs.
Note: Understanding Graphite Bipolar Plates: The Key Component of Fuel Cells
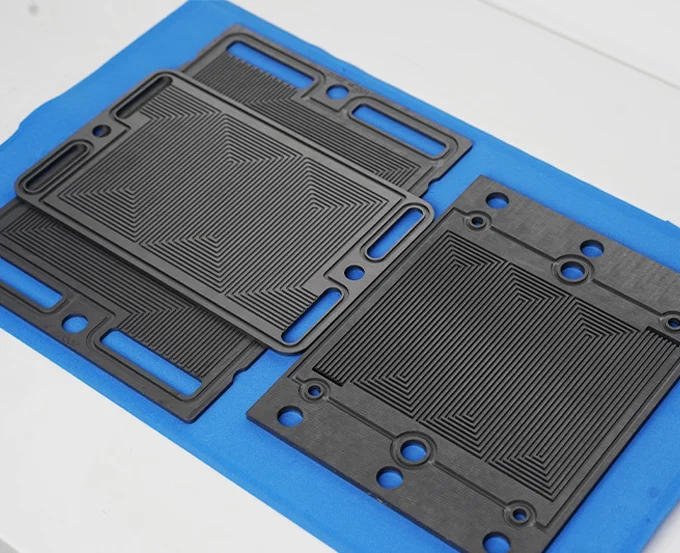
2.4.2.2 Metal Bipolar Plates
Metal bipolar plates have high strength, good toughness, excellent electrical and thermal conductivity, low cost, and superb processing performance. They can significantly reduce the thickness of the flow field plates (the excellent mechanical processing strength allows metal bipolar plates to be less than 1 mm thick), greatly enhancing the power density of the cells. This makes them the optimal choice for micro fuel cells. However, metal bipolar plates are prone to corrosion in the PEMFC working environment, making surface modification or coating a necessary choice. Currently, stainless steel plates are widely researched because they have advantages such as low cost, high strength, easy forming, and small volume.
Note: Understanding Metallic Bipolar Plates for PEM Fuel Cells
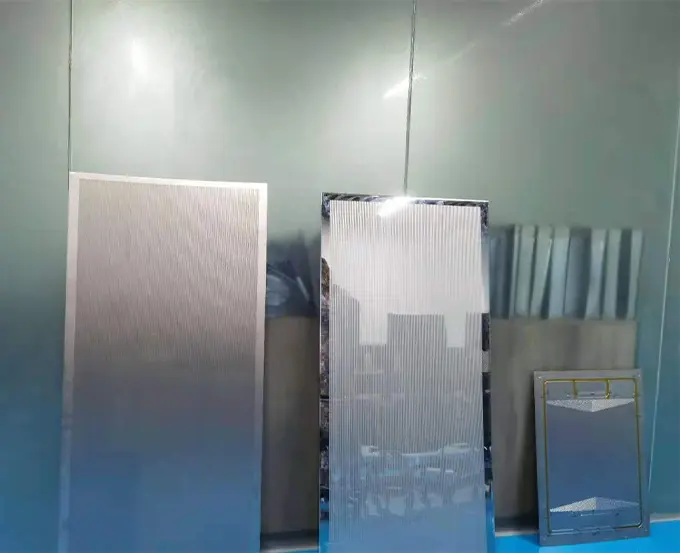
2.4.2.3 Composite Bipolar Plates
In addition to graphite and metal bipolar plates, composite bipolar plates are also commonly used. These are made by using thin metal plates or high-strength conductive plates as separators, with frames made of plastic, polysulfone, and polycarbonate, and the frame and metal plate bonded with adhesive. Flow field plates are prepared using injection molding and sintering methods.
Composite bipolar plates combine the advantages of graphite and metal bipolar plates. They are cheaper to produce, occupy less space, have higher mechanical strength, and better corrosion resistance, optimizing the mass-specific power and volume-specific power of fuel cell stacks. They have become the future trend for bipolar plates, but their electrical and mechanical properties still need improvement.
2.5 Air Compressor
The air compressor is a crucial component of the cathode air supply system in automotive fuel cells. By pressurizing the air entering the stack, it can increase the power density and efficiency of the fuel cell, and reduce the size of the fuel cell system. However, the parasitic power consumption of the air compressor is quite high, accounting for about 80% of the auxiliary power consumption of the fuel cell. Its performance directly affects the efficiency, compactness, and water balance characteristics of the fuel cell system. Therefore, fuel cell projects around the world place great emphasis on the research of air compressors.
Unlike conventional secondary batteries, fuel cell power generation requires a complex set of auxiliary systems for material supply, temperature control, and more. A typical fuel cell power generation system includes air subsystems, hydrogen subsystems, thermal management subsystems, and electronic control subsystems. Key components include air compressors, humidifiers, hydrogen recirculation pumps, and more.
Ending
This concludes the entire content of this article, which mainly revolves around the principles of proton exchange membrane fuel cells and the construction of various components. It explains the working principle formula of PEMFC and highlights the crucial roles of the five main components in PEMFC: platinum catalyst, proton exchange membrane, gas diffusion layer, catalyst electrode layer, and bipolar plate. Each component significantly affects the performance, lifespan, and cost of PEMFC.
Related articles:
What are the main differences between PEM fuel cell,FCAFC,MCFC,SOFC and DMFC ?
Practical Applications of Proton Exchange Membrane Fuel Cells