What is graphite bipolar plate?
A graphite bipolar plate is a crucial component in fuel cells, particularly in proton exchange membrane fuel cells (PEMFCs) and solid oxide fuel cells (SOFCs). It is responsible for providing the surface for electrochemical reactions, enabling the flow of electrons, and serving as a separator between individual fuel cell units.
Graphite bipolar plates are valued for their excellent electrical conductivity, high stability, and strong resistance to corrosion. They play a key role in the fuel cell stack by facilitating the distribution of reactant gases, removing heat, and contributing to the overall structural integrity of the cell stack.
What materials are graphite bipolar plates made of?
Graphite bipolar plates are primarily made from various types of graphite, which can include natural graphite, synthetic graphite, or expanded graphite. However, they are often further processed or combined with other materials to improve their mechanical properties, electrical conductivity, and corrosion resistance.
1. Natural Graphite: This is mined from natural sources and processed to form the plates. It has good electrical conductivity but may require additional treatment to improve durability and resistance to corrosion.
2. Synthetic Graphite: This is produced through industrial processes, providing a more uniform structure and potentially enhanced properties such as higher purity, better mechanical strength, and improved resistance to wear and tear.
3. Expanded Graphite: This type of graphite is made by chemically treating graphite to create a more flexible, expanded structure. It’s often used to create composite bipolar plates, providing a balance of flexibility and conductivity.
To enhance the performance and durability of graphite bipolar plates, they are often combined with resin binders, polymers, or other conductive additives. These composites help increase mechanical strength, reduce brittleness, and maintain conductivity, making them more suitable for use in the demanding environments of fuel cells.
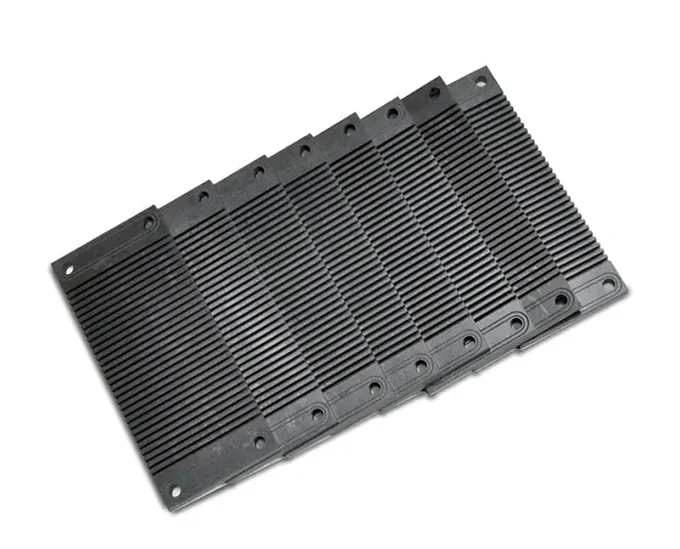
How Graphite Bipolar Plates Are Made?
Graphite bipolar plates are vital components in fuel cells, providing a conductive surface for reactions and a structure that separates individual cells. Their production involves complex processes to ensure high conductivity, strength, and resistance to corrosion.
Next, we will look at how these panels are manufactured, focusing on three key manufacturing methods: Machined Graphite Plates,Injection-Molded Graphite Plates, and Molded Graphite Plates.
1. Machined Graphite Plates
The manufacturing process for machined graphite plates involves several steps:
Raw Material Preparation: This involves mixing coke and pitch at high temperatures (1,000-1,300°C) to form carbon, which is then impregnated with pitch and baked. The carbonized material is subsequently heated in an electric furnace at 2,500-3,000°C to produce graphite.
Slicing: The large graphite blocks are roughly sliced into sheets to fit the required bipolar plate dimensions.
Impregnation: The graphite slices undergo resin impregnation to fill the internal pores and improve surface quality. This process typically takes 24 hours, followed by heat treatment to solidify the resin. Depending on the type of resin used, graphite plates can be impregnated with phenolic or furan resins.
Grinding: After impregnation, the plates are coarse, so they undergo coarse, medium, and fine grinding to achieve the desired smoothness.
Engraving and Machining: This is a critical step for achieving precise flow fields and dimensions. Due to graphite’s brittleness, this process requires high precision to ensure quality and structural integrity.
This method may not be suitable for ultra-thin plates (less than 1.5 mm) due to graphite’s low strength and brittleness, leading to increased tool wear and potentially inaccurate dimensions.
2. Injection-Molded Graphite Plates
Injection molding uses a mixture of graphite and resin, which is heated and injected into a mold to form bipolar plates. This process involves:
Material Mixing: Graphite and resin are blended in specific proportions. Metal powders and fibers (like carbon or ceramic fibers) can be added to enhance conductivity and mechanical strength.
Injection Molding: The mixture is heated and injected into a closed mold. After cooling and solidification, the bipolar plate is removed from the mold.
While injection molding offers scalability, it has limitations, including prolonged binder removal (up to 7 days), cracking in thick sections, and size constraints. Further graphite processing can improve performance but increases production costs.
3. Molded Graphite Plates
Molded graphite plates are made to reduce production costs and enable large-scale manufacturing:
Material Preparation: A mixture of graphite powder and resin is prepared, then subjected to pre-treatment.
Molding: The mixture is placed in a mold, and pressure and heat are applied to allow the material to flow and fill the mold cavity. If the binder is thermosetting plastic, curing and demolding take a few minutes. If it’s thermoplastic, the mold must be cooled below the melting point before demolding.
Molded graphite plates offer a more cost-effective and scalable method compared to other processes, but require careful control to ensure uniformity and quality.
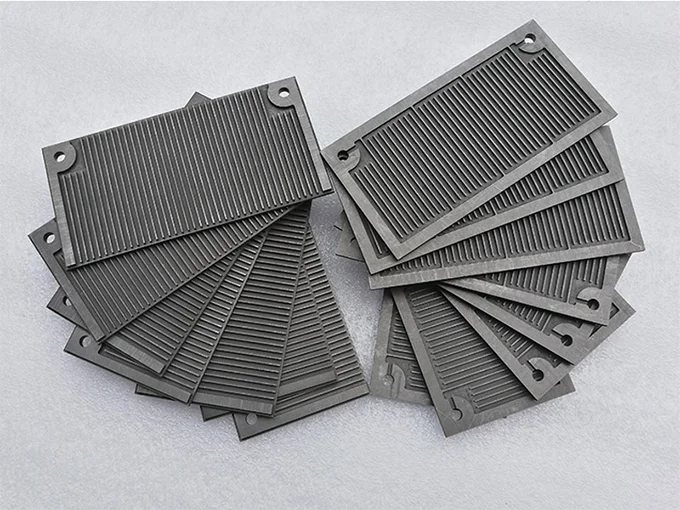
Applications of Graphite Bipolar Plates
Graphite bipolar plates are essential industrial components, especially in hydrogen energy applications, owing to their remarkable conductivity, durability, and chemical resistance. Next,Let’s explore some of the key applications of graphite bipolar plates across various industries:
1. Fuel Cell Manufacturing
Graphite bipolar plates are critical in the production of fuel cells, serving as both anode and cathode components. They play a vital role in storing electrical charges and facilitating electron transport within the cell. As an electron transmission pathway, these plates enable the electrochemical reactions required to generate electrical power. Their high conductivity and corrosion resistance make them ideal for use in fuel cells, particularly in Proton Exchange Membrane Fuel Cells (PEMFCs) and Solid Oxide Fuel Cells (SOFCs).
2. Hydrogen Production via Water Electrolysis
Water electrolysis involves breaking down water into hydrogen and oxygen using electrical energy. Graphite bipolar plates function as electrodes in this process, facilitating the electrochemical reactions needed to produce hydrogen gas. This application is crucial in generating hydrogen fuel, providing a sustainable and environmentally friendly energy source.
3. Electrochemical Sensors
Graphite bipolar plates are used in electrochemical sensors, devices designed to detect chemical substances through electrochemical reactions. As electrodes in these sensors, graphite bipolar plates help measure changes in electrode potential to determine the concentration of specific chemicals. This technology is widely used in environmental monitoring, medical diagnostics, and industrial process control, offering precise and reliable chemical detection.
4. Electrochemical Machining
In electrochemical machining, graphite bipolar plates serve as electrodes to process materials through electrochemical reactions. By controlling the electrode potential, this method allows for precise material removal and shaping. Electrochemical machining is commonly used to create microdevices, nanomaterials, and other high-precision components, offering a non-contact and low-thermal impact approach to manufacturing.
Graphite bipolar plates are versatile and play a significant role in advancing electrochemical technologies. From fuel cell manufacturing to hydrogen production, electrochemical sensors, and machining, their applications are broad and impactful.
Should Fuel Cells Use Graphite Bipolar Plates or Metal Bipolar Plates?
The choice between graphite and metal bipolar plates depends on the specific requirements of the fuel cell application. If corrosion resistance and durability are primary concerns, graphite bipolar plates are a better choice. However, if thinness, lightweight, and lower manufacturing costs are more critical, metal bipolar plates may be more suitable.
For high-performance fuel cells where longevity and corrosion resistance are paramount, graphite bipolar plates are generally preferred. On the other hand, for compact and lightweight applications, metal bipolar plates are likely the better option, provided proper corrosion protection is implemented. Ultimately, the decision should be based on a comprehensive assessment of the fuel cell’s intended use, environmental conditions, and performance requirements.
Click to learn about metal bipolar plates for PEM fuel cells>>>
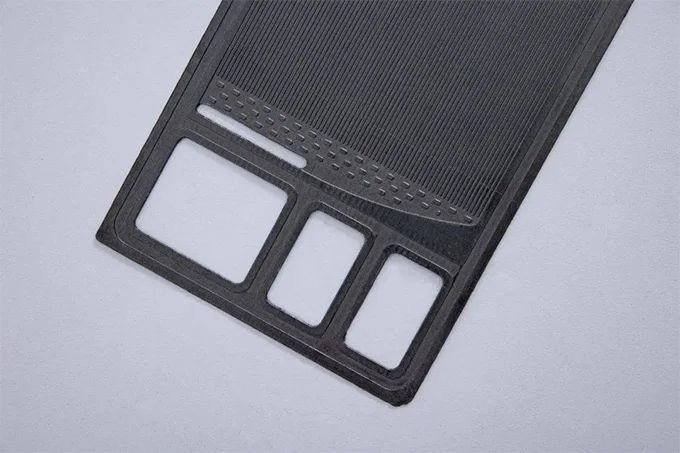