Introduction
In fuel cells, the bipolar plate is one of the core components, playing a crucial role in separating the cells, conducting electricity, and managing gas flow. However, due to the long-term exposure of bipolar plates to complex electrochemical environments, their stability and lifespan often face challenges. In practical applications, bipolar plates not only come into contact with hydrogen, oxygen, electrolyte solutions, and the water produced by reactions but are also frequently exposed to air containing impurities such as water vapor and carbon dioxide. These impurities, when combined with oxygen, can form oxides or other corrosive compounds on the surface of the bipolar plate, leading to corrosion. These corrosive products not only reduce the conductivity of the bipolar plate but can also cause localized structural deterioration, ultimately affecting the overall performance and lifespan of the fuel cell.
The corrosion issue of bipolar plates is not only related to the electrochemical environment in which they are situated but also closely connected to the operating conditions, environmental factors, and material choices of the fuel cell. In real-world scenarios, fuel cells may be exposed to air containing pollutants like sulfur dioxide and nitrogen oxides, which, when combined with moisture, can generate acidic or corrosive substances that accelerate the corrosion of the bipolar plate. Furthermore, in applications such as transportation or industrial use, bipolar plates must also withstand external stresses like salt spray, mechanical vibrations, and temperature fluctuations, all of which further shorten the lifespan of the bipolar plate.
To address these challenges, TMN will conduct a detailed discussion on the role of bipolar plates in fuel cells, covering the following aspects: the operating principles of fuel cells, reaction processes, working environments, material selection, and anti-corrosion measures. Through an in-depth analysis of these factors, TMN will provide solutions to optimize the performance of bipolar plates, thereby extending the lifespan of fuel cells and enhancing their overall efficiency and reliability.
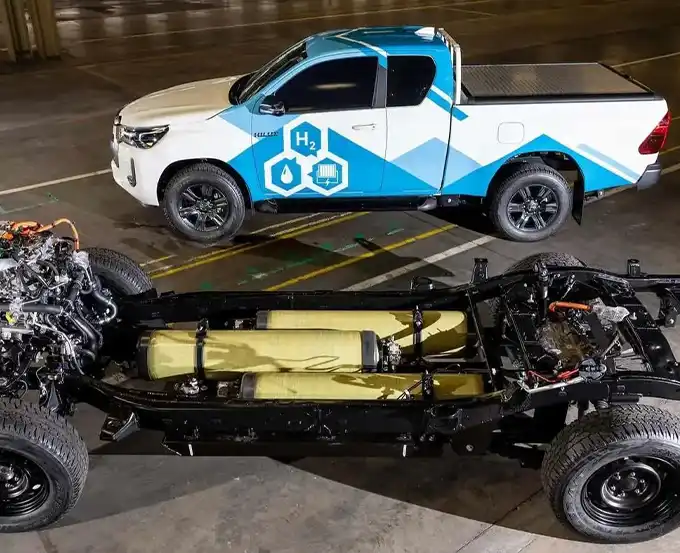
The Reaction Process and Role of Bipolar Plates in Fuel Cells:
In practical applications, bipolar plates play a crucial role in the reaction process within fuel cells. Through effective gas management, conductive connections, heat dissipation, and structural support, they ensure the efficient and safe operation of fuel cells.
1. The Operational Process of Fuel Cells
1.1 Hydrogen Supply and Anode Reaction
Hydrogen Inflow: Hydrogen (H₂) is directed to the anode side of the fuel cell. The flow channels of the bipolar plate ensure the even distribution of hydrogen to the anode catalyst layer.
Anode Reaction: On the surface of the anode catalyst (such as platinum), hydrogen is split into protons (H⁺) and electrons (e⁻). The chemical reaction is: 2H₂ → 4H⁺ + 4e⁻.
Protons pass through the electrolyte membrane to the cathode, while electrons flow through the external circuit, forming an electric current.
1.2 Electron Flow and Current Generation
Current Formation: The electrons produced from the splitting of hydrogen flow through the external circuit to the cathode, providing power to external loads (such as the motor of an electric vehicle, equipment, or the power grid). At this point, the current flows through the load, releasing energy.
1.3 Oxygen Supply and Cathode Reaction
Oxygen Inflow: Oxygen (O₂) is directed to the cathode side of the fuel cell. The flow channels of the bipolar plate ensure the even distribution of oxygen to the cathode catalyst layer.
Cathode Reaction: On the surface of the cathode catalyst (such as platinum), oxygen combines with protons and electrons to form water. The chemical reaction is: O₂ + 4H⁺ + 4e⁻ → 2H₂O.
The water produced is then removed from the cell.
2. Specific Roles of Bipolar Plates
2.1 Gas Distribution and Management
Gas Distribution: The flow channels within the bipolar plates help evenly distribute hydrogen and oxygen to the reaction areas, preventing uneven gas flow that could reduce reaction efficiency.
Water Removal: The flow channels of the bipolar plate also help remove the water produced during the reaction, preventing water accumulation, which could affect gas flow and reaction efficiency.
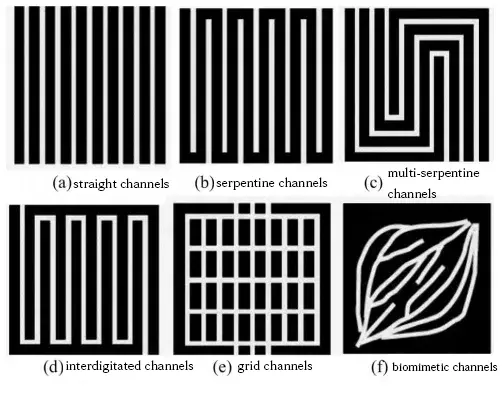
2.2 Current Conduction
Conductive Connection: The bipolar plates connect adjacent cells, providing a conductive pathway through the electrode surfaces, ensuring smooth electron flow within the cell stack. This is crucial for maintaining the current output of the cell stack.
2.3 Cooling and Heat Dissipation
Thermal Management: Fuel cells generate heat during operation. The materials and design of the bipolar plates aid in the conduction and dissipation of heat, maintaining the fuel cell’s temperature within an optimal range to prevent overheating.
2.4 Structural Support
Mechanical Stability: Bipolar plates not only provide electrical connections but also support the structure of the fuel cell stack, ensuring the stability of the cells during operation and transportation.
The Importance of Corrosion Resistance for Bipolar Plates
In practical applications, fuel cells are commonly used in various vehicles (such as cars and buses) and backup power supplies. Their operating environments are complex and variable, which has a tangible and significant impact on the corrosion performance of bipolar plates.
1. Temperature and Humidity Variations in Urban Transportation Environments
In cars and buses, fuel cells must operate in outdoor environments where temperature and humidity fluctuations are substantial. For example, in low-temperature winter conditions, the water in the electrolyte membrane may freeze, affecting ion conductivity. Low temperatures can also slow down the reaction rate, potentially leading to localized corrosion on the bipolar plates.
In contrast, during hot summers, high temperatures and humidity may accelerate corrosion reactions. Especially when vehicles are parked, a high-humidity environment may form inside the fuel cell, making the bipolar plates more susceptible to corrosion.
2. Impact of Gas Purity in Real-World Operation
Hydrogen: In real-world applications, hydrogen is often not pure and may contain trace amounts of impurities such as carbon monoxide and sulfur compounds. These impurities can react with the bipolar plates during fuel cell operation, forming corrosive products that directly affect the lifespan of the bipolar plates.
Oxygen: In actual use, fuel cells typically draw air from the outside as the oxidant. However, air contains pollutants like carbon monoxide, sulfur dioxide, hydroxides, and particulate matter. These pollutants can chemically react with the bipolar plates inside the fuel cell, leading to increased surface corrosion. This issue is particularly pronounced in regions or countries with poor air quality, where pollutant concentrations are higher.
3. Frequency of Vehicle Startups and Shutdowns
In traffic, vehicles often face frequent startups and shutdowns and may even encounter congested traffic conditions. The fuel cell switches from low-power mode to high-power mode, accompanied by temperature changes. This constantly changing environment poses a long-term challenge of wear and corrosion to the materials of the bipolar plates.
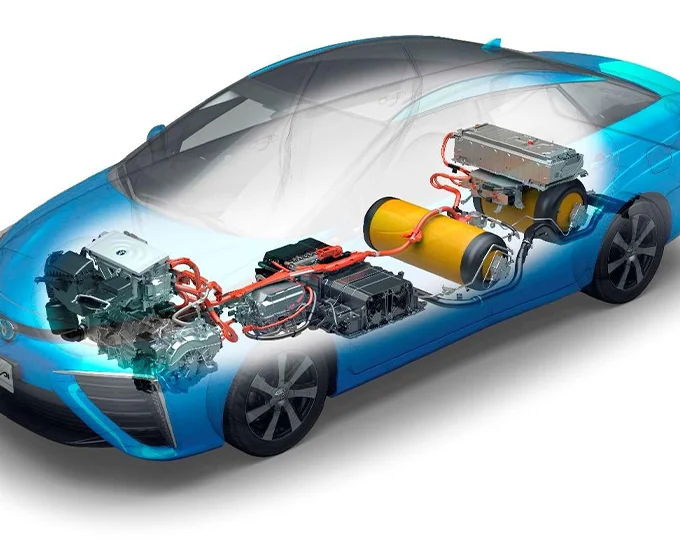
Corrosion Performance of Bipolar Plates Made from Different Materials
Given the complex and variable working environments, the choice of materials for bipolar plates is crucial. Understanding the properties of various materials and their performance in specific corrosive environments is essential. TMN will now discuss bipolar plates made from different materials to help you quickly understand the corrosion resistance characteristics of each:
1. Stainless Steel Bipolar Plates
Corrosion Resistance Advantages:
Protective Oxidation: Stainless steel is primarily composed of iron, chromium, and nickel. Its surface easily forms a chromium oxide layer, which provides good corrosion resistance, especially in neutral and mildly acidic environments.
Broad Applicability: Stainless steel can offer good corrosion resistance in various environments, including humidity, acidic steam, and certain acidic or alkaline solutions.
Limitations:
Susceptibility to Pitting and Crevice Corrosion: Although stainless steel generally has good corrosion resistance, it is prone to pitting or crevice corrosion in certain conditions (such as chloride environments), which can weaken the bipolar plate’s functionality over prolonged use.
Cost and Weight: Stainless steel is relatively dense, making it unsuitable for weight-sensitive applications. Additionally, stainless steels with high nickel content (such as 316L) offer stronger corrosion resistance but are also more expensive.
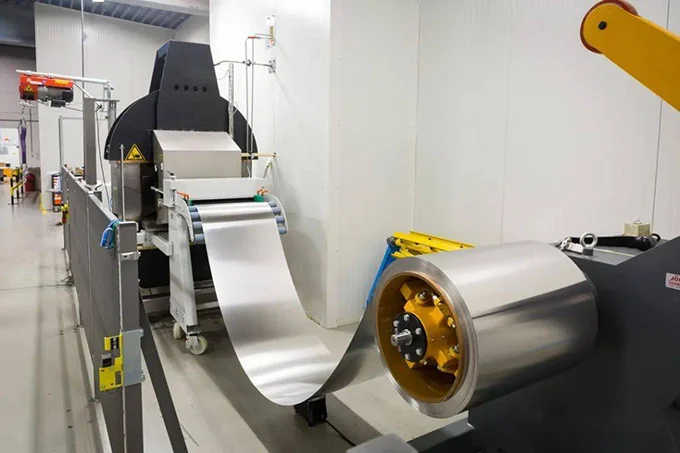
2. Titanium Alloy Bipolar Plates
Corrosion Resistance Advantages:
Outstanding Oxidation Resistance: Titanium forms a dense passive film (primarily titanium dioxide) in the air, which effectively resists the erosion of oxygen and other corrosive media.
Resistance to Chloride Corrosion: Titanium alloys are particularly resistant to corrosion in chloride environments.
Limitations:
High Cost: Titanium is expensive, and its processing is challenging, leading to higher manufacturing costs for titanium alloy bipolar plates.
Lower Conductivity: Titanium has lower electrical conductivity compared to copper and aluminum. Surface treatment is required to enhance its conductivity.
3. Graphite Bipolar Plates
Corrosion Resistance Advantages:
Natural Corrosion Resistance: Graphite has excellent chemical stability and does not easily react with hydrogen, oxygen, or electrolytes, providing extremely high corrosion resistance in acidic and alkaline environments.
Oxidation Resistance: Graphite is highly resistant to oxidation, and even in high-temperature environments, graphite bipolar plates can maintain relatively stable structures and are not easily oxidized.
Limitations:
Insufficient Mechanical Strength: While graphite excels in corrosion resistance, it is brittle and fragile, with high processing costs, limiting its use in applications requiring high mechanical strength.
Sealing Performance: Graphite bipolar plates do not seal as well as metal bipolar plates, which increases the risk of gas leakage.
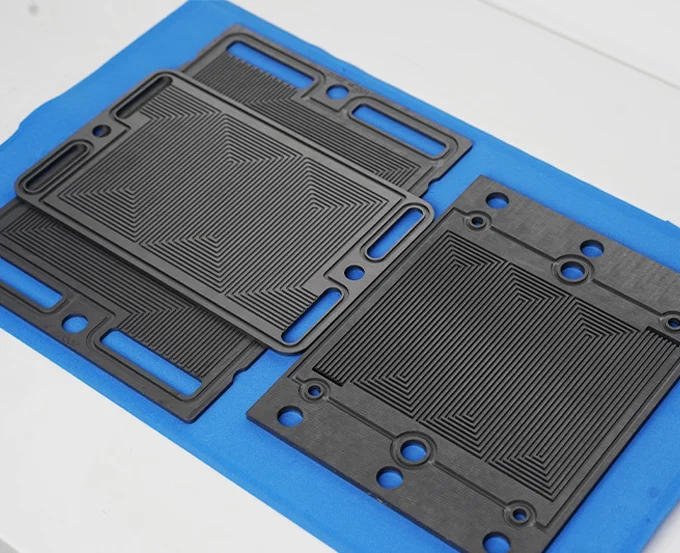
4. Carbon Composite Bipolar Plates
Corrosion Resistance Advantages:
Chemical Stability: Carbon composite materials exhibit excellent corrosion resistance in both acidic and alkaline environments, and they do not react with most chemical substances.
Lightweight: Compared to metal bipolar plates, carbon composites have a lower density, which can significantly reduce the weight of the fuel cell, making them suitable for applications requiring lightweight materials.
Limitations:
High-Temperature Oxidation: Carbon composite materials are prone to oxidation at high temperatures, especially in environments with high temperature and humidity, requiring additional protective measures.
Complex Production Process: The manufacturing and processing of carbon composites are complex, which can affect production efficiency and cost control if not carefully managed.
How to Enhance the Corrosion Resistance of Bipolar Plates
From the above, we understand that the environment significantly impacts the corrosion performance of bipolar plates. To ensure the overall performance of fuel cells, enhancing the corrosion resistance of bipolar plates is crucial. TMN will now provide some measures and suggestions based on the issues mentioned above:
1. Material Selection and Surface Treatment
High Corrosion-Resistant Materials:
Select materials with excellent corrosion resistance, such as titanium alloys, carbon composites, or optimized stainless steel (e.g., 316L). These materials perform well in various corrosive environments.
Surface Passivation:
Conduct passivation treatments on the surface of the bipolar plates to enhance their corrosion resistance. For example, surface passivation of titanium alloys can form a dense oxide layer that protects the substrate from corrosive media.
Coating Technology: Apply anti-corrosion coatings (such as platinum, gold, or metal carbides) to the surface of the bipolar plates to effectively increase corrosion resistance.

2. Gas Purity Control:
Use High-Purity Hydrogen and Oxygen:
Reduce the content of impurities in the fuel, such as carbon monoxide and sulfur compounds, to significantly decrease the reaction of impurities with the bipolar plates, thus preventing the formation of corrosive products.
Air Filtration System:
Filter the intake air to remove pollutants and particulates, increasing the oxygen purity in the air and reducing the concentration of corrosive substances.
3. Optimize Bipolar Plate Design
Flow Channel Design:
Design the flow channel structure of the bipolar plates to ensure even distribution of reactive gases and effectively remove the generated water, avoiding water accumulation and slowing the corrosion process.
Thermal Management Design:
Implement efficient heat dissipation designs to maintain the fuel cell at an optimal temperature during operation, preventing heat-induced corrosion at high temperatures.
4. Maintenance Optimization:
Regular Inspection and Maintenance:
Regularly inspect the condition of the bipolar plates, promptly identify and repair corrosion issues, and extend their service life.
By implementing these measures, the corrosion resistance of bipolar plates can be effectively improved, thereby extending the service life of fuel cells and enhancing overall performance and reliability.
Related Searches:
Practical Applications of Proton Exchange Membrane Fuel Cells
The influence of bipolar plate structure on fuel cell performance
Understanding Graphite Bipolar Plates: The Key Component of Fuel Cells
Understanding Metallic Bipolar Plates for PEM Fuel Cells