Bipolar plates are critical components in fuel cells and water electrolysis devices. With increasing environmental awareness and continuous technological advancements, the demand for fuel cells in areas such as electric vehicles and portable power devices is on the rise. Consequently, the market demand for efficient and reliable Bipolar plates is also growing. This trend has spurred research and development in materials, design, and manufacturing processes of Bipolar plates, bringing more innovation and breakthroughs to the industry.
What is a Bipolar plate?
A Bipolar plate is an essential component of proton exchange membrane fuel cells and other types of fuel cells. It plays a crucial role in the cell, with primary functions including distributing fuel (such as hydrogen) and oxidants (such as oxygen or air), collecting and conducting current, and providing gas tightness and structural support between the cell units. Bipolar plates are typically made of metal or composite materials, featuring high conductivity, good gas tightness, and corrosion resistance.
The design of Bipolar plates usually includes complex flow channel structures to evenly distribute fuel and oxidants, optimizing electrochemical reaction efficiency. Their surface needs to have excellent conductivity and corrosion resistance to ensure stability and reliability during long-term operation. Additionally, the manufacturing precision of Bipolar plates directly affects the performance and efficiency of fuel cells. Therefore, high-precision processes such as Photochemical etching are required during manufacturing to ensure the complex shapes and details of the flow channels.
In fuel cell systems, Bipolar plates have multiple functions, including current collection and distribution, distribution of reaction gases and coolant, sealing and isolating reaction gases, and providing mechanical support. Thus, the material selection and manufacturing process of Bipolar plates are critical to ensure performance and durability under various operating conditions.

Manufacturing Requirements and Quality of Bipolar plates
The manufacturing and quality requirements for Bipolar plates are extremely stringent. Whether considering the materials, manufacturing processes, or the thickness, dimensions, and precision of the finished product, strict controls are necessary to ensure performance and durability in fuel cells. Below is a detailed introduction:
Material Selection:
Conductivity:
The material for Bipolar plates needs to have high conductivity to ensure efficient current conduction. Common materials include stainless steel, graphite, and Titanium.
Corrosion Resistance:
Bipolar plates will come into contact with acidic environments in fuel cells, so the material needs to have good corrosion resistance.
Mechanical Strength:
The materials used must also have sufficient mechanical strength and toughness to withstand the operating pressure and mechanical stress of fuel cells.
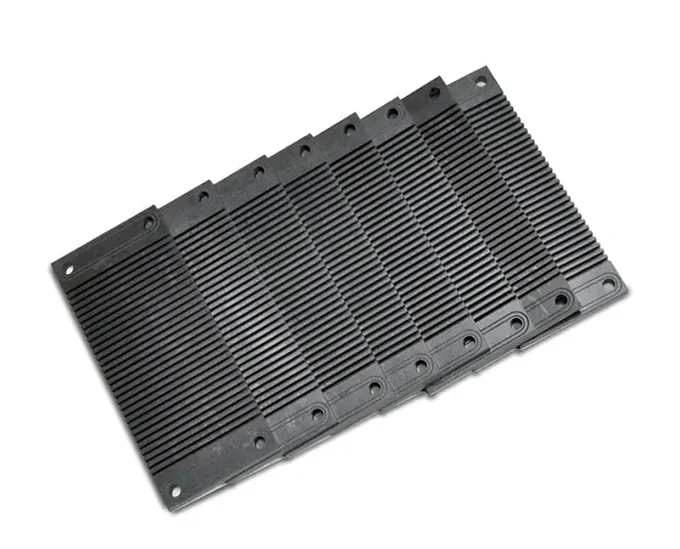
Manufacturing Process:
Precision Machining:
The flow channel structures of Bipolar plates are complex, requiring high-precision manufacturing processes to ensure the dimensional accuracy and consistency of the channels.
Surface Treatment:
To improve the conductivity and corrosion resistance of Bipolar plates, surface treatments such as gold plating or platinum plating are often necessary.
Thickness and Dimension Control:
The thickness and dimensions of Bipolar plates need to be strictly controlled to ensure the overall consistency and sealing of the fuel cell stack. During manufacturing, it is also crucial to prevent the material from being affected by stress, avoiding deformation, thermal melting, and other issues. Among many materials, Titanium has garnered widespread attention due to its unique properties.
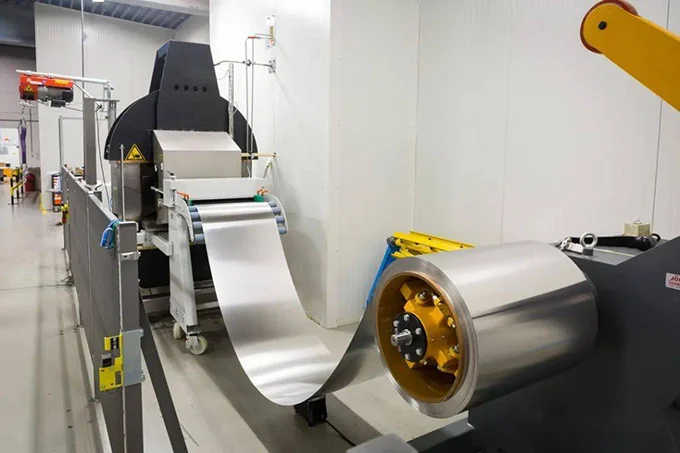
Metal Material – Titanium
Titanium is a metal material with many excellent properties, widely used in aerospace, medical, industrial, and consumer goods fields. The smelting process of Titanium is complex and requires high temperatures and an inert gas environment to prevent oxidation. Common methods include the Kroll process and molten salt electrolysis. Due to the high cost of refining and processing Titanium, its use is limited in some low-cost applications.
Advantages
Titanium has a very high strength-to-weight ratio. Although its density is only 60% that of steel, its strength is comparable to certain types of steel. Titanium exhibits excellent corrosion resistance, maintaining stability in corrosive environments such as seawater, acids, and alkalis. Additionally, Titanium has good electrical and thermal conductivity, and excellent high-temperature resistance. Moreover, Titanium’s environmental friendliness and sustainability make it highly favored in modern industry. Titanium is an environmentally friendly metal that does not release harmful substances during use and can be recycled, aligning with today’s sustainable development principles.
These characteristics give Titanium significant advantages in the manufacture of Bipolar plates.
Challenges
The high cost of refining and processing Titanium is the main factor limiting its widespread application. Since Titanium easily reacts with gases like oxygen and nitrogen at high temperatures, smelting must be conducted in an inert gas environment, increasing production costs. Additionally, Titanium is difficult to process; its high hardness and strength place higher demands on processing equipment and techniques.
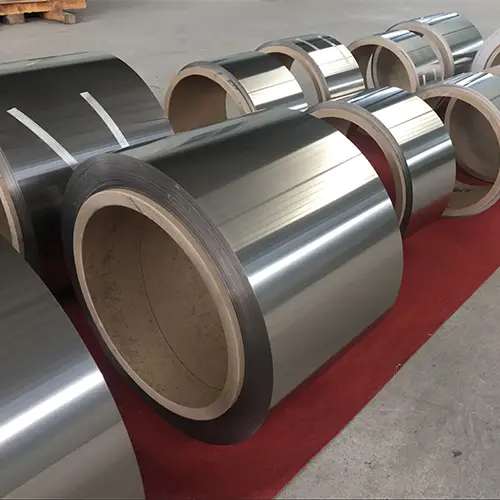
The Significance of Titanium in Manufacturing Bipolar plates
Titanium, as a material for Bipolar plates, possesses many excellent characteristics, but its high cost limits its widespread commercial application. Currently, stainless steel and graphite Bipolar plates remain the mainstream choices in the market. However, disregarding cost factors, Titanium demonstrates significant advantages in the manufacturing of Bipolar plates.
Firstly, the high strength and low density of Titanium make the Bipolar plates both robust and lightweight, effectively reducing the overall weight of the fuel cell. Secondly, Titanium exhibits excellent corrosion resistance, allowing it to operate stably in the acidic or alkaline environments of fuel cells, thus extending the device’s lifespan. Additionally, Titanium’s good electrical and thermal conductivity helps improve the efficiency and performance of fuel cells. These properties make Titanium an ideal material for Bipolar plates, meeting modern industrial demands for efficient, durable, and environmentally friendly materials.
To promote the widespread use of Titanium in Bipolar plates, improvements and research in several key areas are necessary. First, more cost-effective Titanium manufacturing processes need to be developed to reduce production costs. Second, the performance of Titanium can be further enhanced through alloying or surface treatments, making it perform better in specific applications. Finally, extensive testing and research on the application of Titanium Bipolar plates in actual fuel cell systems are essential to verify their reliability and durability under real-world conditions.
Although the application of Titanium in Bipolar plate manufacturing is currently not extensive, its potential as a Bipolar plate material will gradually be realized with technological advancements and cost reductions. In the future, Titanium is expected to become one of the primary materials for Fuel bipolar plates, contributing to the development of green energy.
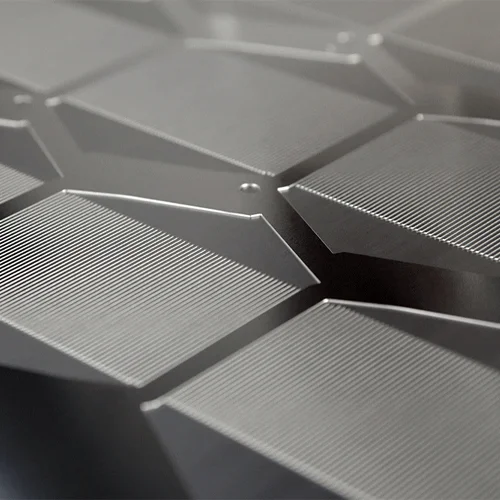
How to Find a Titanium Bipolar Plate Manufacturer that Meets Your Requirements
When choosing a supplier, it is crucial to find a reliable, professional partner who meets your needs. Here are several key factors to help you make an informed decision when looking for the right supplier:
1. Professional Manufacturing Capability
The supplier must have professional manufacturing capabilities to ensure product quality and production efficiency. It is especially important to work directly with the manufacturer to avoid information errors from intermediaries.
(TMNi boasts its own Etching plant, equipped with five fully automated Photochemical etching production lines, each 39 meters long, capable of providing high-quality manufacturing services.)
2. Experienced Team
An experienced team is a critical guarantee of product quality. Factories without custom service experience and Bipolar plate manufacturing experience may struggle to meet complex production needs.
(TMNi has over 100 experienced workers and a team of engineers and chemists, ensuring that every aspect of the product is professionally handled.)
3. Extensive Raw Material Inventory
The availability and variety of raw materials are important considerations when selecting a supplier. Ample raw material inventory can save procurement time and costs.
(TMNi has a large independent metal material warehouse, storing various metal raw materials from 0.01mm to 3.0mm, enabling quick response to customer needs.)
4. Customization Services
Each customer’s needs are unique, making the supplier’s ability to provide customization services especially important. Customization ensures that products fully meet specific customer requirements.
(TMNi has customized stainless steel and Titanium Bipolar plates for customers, achieving precision control within +/-0.03mm, ensuring high precision and quality of the products.)
5. On-site Inspection
Transparency and trust are the foundations of a long-term cooperative relationship. Being able to inspect the factory on-site allows customers to witness the production process firsthand, enhancing trust in the manufacturer.
(TMNi allows customers to visit the factory, giving them the opportunity to witness the production process firsthand, further strengthening trust in TMNi.)
6. Sample Provision
Obtaining samples for testing and verification before mass production is critical. Sample testing helps customers confirm product quality and specifications, ensuring that the final product meets expectations.
(TMNi provides a small number of samples, helping customers confirm product quality and specifications before formal production, ensuring that the final product fully meets expectations.)
If you have any needs or questions about customized bipolar plates,you can easily contact us by phone, WeChat and WhatsApp at +8613603056883; for inquiries, please email lydia.sales1@tmnetch.com.
Related articles:
The influence of bipolar plate structure on fuel cell performance
Understanding Graphite Bipolar Plates: The Key Component of Fuel Cells
Fuel cell bipolar plates materials and manufacturing
Photo Etching: Impact on the development of PEM fuel cells for electric vehicles