Earlier, we introduced the development events of fuel cells. As we can see, the development of fuel cells over time has been diverse, leading to a variety of types and numerous classification methods. However, the most common classification is based on the type of electrolyte, including “proton exchange membrane fuel cells,” “alkaline fuel cells,” “phosphoric acid fuel cells,” “molten carbonate fuel cells,” and “solid oxide fuel cells.” Besides classifying by electrolyte type, there are also classifications based on reaction temperature, different fuels, and other methods.
In the previous blog post on the development of fuel cells, we mentioned that proton exchange membrane fuel cells (PEMFCs) hold a dominant position in both practical applications and research. Of course, solid oxide fuel cells and molten carbonate fuel cells also have a certain research status. Next, we will briefly introduce some commonly researched types of fuel cells.
Proton Exchange Membrane Fuel Cell (PEMFC)
As one of the key materials in fuel cells, proton exchange membranes have garnered widespread attention and in-depth research from scholars worldwide. Fluoropolymer, aromatic polymer, and organic/inorganic hybrid materials have been successively developed as proton exchange membranes.
In proton exchange membrane fuel cells, the electrolyte is one of the key materials. It is a very thin polymer membrane, with DuPont’s Nafion perfluorosulfonic acid proton exchange membrane being one type. This polymer membrane can conduct protons while remaining electrically non-conductive. Electrode materials are generally composed of carbon or metal, with carbon-supported platinum used as the catalyst for the anode and cathode reactions. The operating temperature of PEMFCs is approximately 80°C, and a single cell can produce about 0.7V of voltage. In practical applications, to achieve higher voltage, multiple single cells need to be connected in series to form a fuel cell stack, typically consisting of about 200-500 cells, with the specific number adjusted according to actual situations and needs.
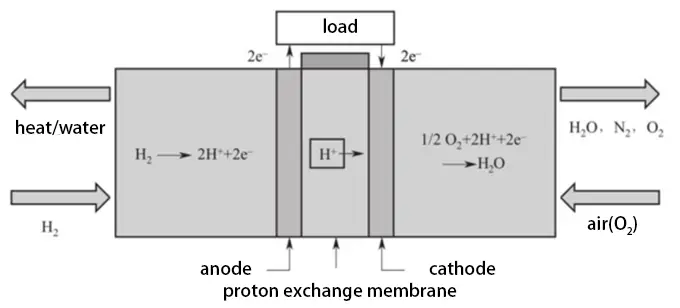
Proton exchange membrane fuel cells can start quickly in greenhouse conditions, easily discharge water by-products, have a long lifespan, high specific power, high specific energy, small volume, and are currently widely used in electric vehicles and home distributed power generation devices. Besides these features, they also have high operational efficiency, generally reaching 40% to 60%, and excellent dynamic response, allowing rapid adjustment of output power based on electricity demand.
Note: The power principle of hydrogen fuel cell vehicles
Despite the evident advantages of proton exchange membrane fuel cells, they also have shortcomings. They require very high purity hydrogen and air quality, as the precious metal platinum catalyst is highly susceptible to contamination by impurities such as carbon monoxide and sulfides, which can significantly reduce catalytic activity and greatly shorten the lifespan of the fuel cell.
Alkaline Fuel Cell (AFC)
Alkaline fuel cells (AFCs) originated in the 1960s with the American company P&W, which improved the Bacon fuel cell to create the AFC. These fuel cells were later used in the Apollo program. AFCs can achieve efficiencies of up to 70% and their design is very similar to that of PEMFCs, with the key difference being that AFCs use a strong alkaline aqueous solution as the electrolyte, such as potassium hydroxide or sodium hydroxide. During the electrochemical reaction, hydroxide ions move from the electrolyte solution to the anode, where they react with hydrogen in an oxidation reaction, producing water and electrons. The electrons travel through an external circuit to the cathode, where they react with oxygen and water to produce more hydroxide ions.The working principle of AFC is shown in the figure below:
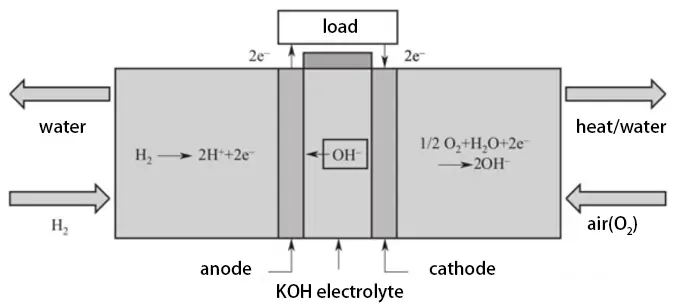
The operating temperature of AFCs is similar to that of PEMFCs, around 80°C. AFCs have a faster start-up speed but their current density is only about one-tenth that of PEMFCs, making them less suitable as portable power sources. AFCs are the lowest cost to manufacture among fuel cells and are often used in small stationary power generation devices. The catalysts used in AFCs can be either platinum or non-precious metal catalysts (such as nickel), making the cost of electrolytes in AFCs much lower than in PEMFCs.
A key challenge for alkaline fuel cells is their susceptibility to carbon dioxide. The formation of carbonates, even from small amounts of carbon dioxide in the air, can significantly affect the performance and durability of the cell. Although AFCs with liquid electrolytes can operate in a recirculation mode to regenerate the electrolyte and help mitigate the impact of carbonate formation, this mode introduces the problem of shunt currents. Liquid electrolyte systems also have other issues, including wettability, increased corrosion, and difficulties in handling pressure differentials.
Molten Carbonate Fuel Cell (MCFC)
Molten carbonate fuel cells (MCFCs) are a highly efficient and sustainable power generation technology with high energy conversion efficiency and clean emissions, making them a promising power generation technology. However, due to their high operating temperature and the special properties of the molten carbonate electrolyte, the development of MCFCs has been hindered.
The electrolyte used in MCFCs consists of lithium carbonate, sodium carbonate, or potassium carbonate solutions. These cells can achieve efficiencies of up to 60% and an operating power of up to 100 MW. Additionally, by utilizing waste heat, fuel efficiency can reach up to 85%. This high efficiency is due to the high operating temperatures of 620-660°C, which allow for more flexible use of various types of fuels and inexpensive catalysts (such as nickel), while ensuring the conductivity of the electrolyte solution.The working principle of MCFC is shown in the figure below:
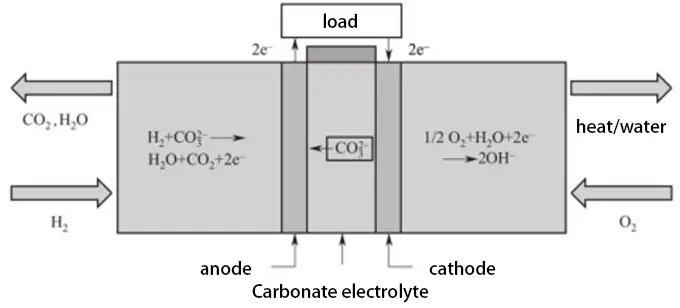
MCFCs can use a variety of fuels, including hydrogen, carbon monoxide, methane, biogas, desulfurized coal gas, or natural gas. The manufacturing processes for MCFC membranes and electrodes are mature, allowing for mass production. However, the high operating temperatures and the corrosive molten environment can cause corrosion and dissolution of the cell materials, significantly reducing their lifespan. Currently, material corrosion is one of the major challenges impeding the development of MCFCs.
Despite issues such as stability in corrosive environments and lower power density compared to other fuel cells, MCFC technology has become the preferred choice for commercial stationary power generation. Multiple companies worldwide are testing kilowatt- to megawatt-scale MCFC power generation systems and providing MCFC systems to industries with relatively smaller power demands. Additionally, there is exploration of MCFC applications in fields such as maritime transport. Due to the rapid development in research and commercialization, MCFCs lead in the number of installed generator units among all fuel cell technologies.
Solid Oxide Fuel Cell (SOFC)
Solid oxide fuel cells (SOFCs), also known as ceramic fuel cells, are the most efficient type of fuel cell, operating at high temperatures of 600-1000°C, which results in very high reaction activity. Among all fuel cell configurations, SOFCs have the highest energy conversion efficiency. They also have several advantages, such as being quiet with no noise, low emissions, and a wide range of fuel options (e.g., natural gas, syngas [a mixture of CO, H2, etc.], biogas such as methane, coal gas, coalbed methane, shale gas, and industrial by-product gas).
An SOFC is composed of an anode, cathode, electrolyte, interconnect, and sealing materials. The primary function of the electrodes is to provide a site for electrochemical reactions and to conduct the electrons needed for these reactions. The main function of the electrolyte is to conduct oxygen ions or protons. The interconnect connects single cells to achieve high power output and prevents direct reactions between air and fuel. Sealing materials keep the fuel and air separated in their respective flow areas.
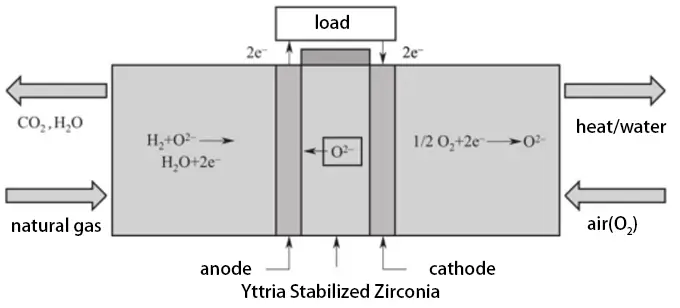
There are two main types of SOFC structures: tubular and planar.
The tubular structure is the earliest SOFC cell structure developed and is currently a relatively mature technology. Tubular cells have high degrees of freedom and are not easily cracked; they use porous ceramics as the support, which makes the structure robust; the cell assembly is relatively simple, making it easy to combine cells in parallel and series to form high-power battery packs. However, tubular SOFCs have relatively thick electrolytes, resulting in high ohmic resistance and thus lower power density.
The planar SOFC structure and preparation process are simpler, which can significantly reduce manufacturing costs. Planar structures use thin-film electrolytes, which significantly reduce the ohmic resistance of the cell and improve its electrochemical performance. However, the edges of the planar cell components need to be sealed to isolate oxidizing and fuel gases, and the bipolar interconnect materials need to be thermally matched with the electrode materials and have good high-temperature oxidation resistance and conductivity.
Due to the reaction temperature of SOFCs being 600-1000°C, the start-up time is relatively long, making them unsuitable for applications requiring immediate on-off operation, such as transportation. Instead, they are more suitable for low-carbon power generation scenarios requiring 24-hour operation, such as data centers, factories, ports, office buildings, hospitals, and remote islands.
Direct Methanol Fuel Cell (DMFC)
Direct methanol fuel cells (DMFCs) are a type of proton exchange membrane fuel cell, characterized by their lightweight, high power, long lifespan, and the use of methanol as a direct fuel source for power generation. DMFCs use polymer membrane electrodes similar to those used in proton exchange membrane fuel cells. During operation, the cell consumes water at the anode and produces water at the cathode. When using pure methanol, the energy density of the cell is relatively high, making it a potential option for electric vehicle applications.
Since DMFCs use methanol directly as fuel, they are as easy to transport and use as gasoline. Methanol is cost-effective and can be sourced from both renewable and non-renewable resources. Known as “liquid sunlight,” methanol offers advantages in terms of self-power generation and long emergency power storage. This makes DMFCs widely applicable in electric vehicles, communication base stations, military applications, marine propulsion, and distributed power stations, with the potential to become mainstream in future portable electronic products.
DMFCs can be categorized into two main types: passive and active. They differ in power output and components. Passive fuel cells generate electricity through the natural flow of liquid methanol within the cell, while active fuel cells use pumps to circulate methanol to the anode. The pump regulates the methanol flow rate, ensuring a constant supply of fuel to the anode. A control system monitors the state of the fuel cell in real-time, adjusting the pump speed and methanol concentration to maintain optimal performance. This approach allows active fuel cells to achieve higher power density than passive fuel cells. The choice between the two types depends on specific application requirements and the trade-off between performance and cost.
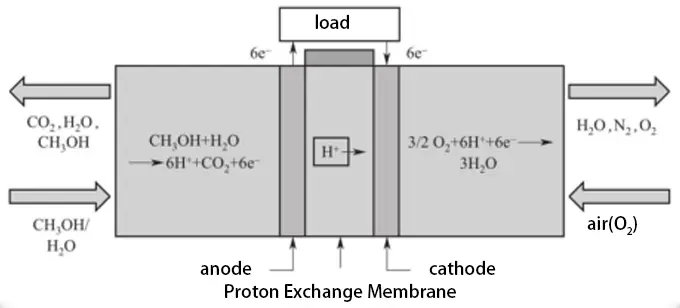
Related articles:
Detailed Explanation of the Structure and Principle of Proton Exchange Membrane Fuel Cells
Practical Applications of Proton Exchange Membrane Fuel Cells