I. Introduction:
With the continuous development of global transportation, the consumption of petroleum by countries around the world is increasing. Among these consumptions, the large-scale popularization of internal combustion engines has led to severe atmospheric pollution and exacerbated the greenhouse effect. To address this issue, the United Nations, the European Union, and the IPCC have unanimously agreed on one thing: we must achieve carbon neutrality by 2050. This decision means that the amount of carbon dioxide emissions must balance with the amount of carbon absorbed in the atmosphere. Therefore, within less than 30 years, we must reduce carbon dioxide emissions to ultimately achieve carbon neutrality and protect the Earth. So, how do we achieve carbon neutrality, and what path should we take?
To achieve this goal, Proton Exchange Membrane (PEM) fuel cells, as a zero-emission clean energy source, will undoubtedly become the main force for carbon neutrality. The Bipolar plate, as one of the core components of the PEM fuel cell, directly influences the utilization rate of reactive gases and the drainage and heat dissipation performance of the fuel cell. This paper collects and summarizes relevant data, organizing the six basic functions that Bipolar plates need to have in fuel cells:
Separate individual cells in the stack;
Transport oxygen and hydrogen;
Provide electrical connection and conduct electricity;
Remove by-products such as water;
Dissipate reaction heat through coolant;
Withstand the clamping force of stack assembly.
Based on the above six basic functions, the design of Bipolar plates needs to meet the following nine basic requirements:
Strong corrosion resistance;
Low resistance and excellent electrical conductivity;
Good thermal conductivity to effectively control cell temperature;
Moderate pressure drop loss at the inlet and outlet;
Easy to process and form;
Strong drainage capacity;
Low weight;
High mechanical strength;
Low cost.
To achieve the above basic functions and requirements, the most important aspect is the structural design of the Bipolar plate. The design of Bipolar plates can be divided into flow field forms and channel structures. The channel structure includes the size of the fluid distribution area, the structure of the diversion area, the length and number of channels, the ratio of channel width to Ridge Width, channel design requirements, and their impact on cell performance.
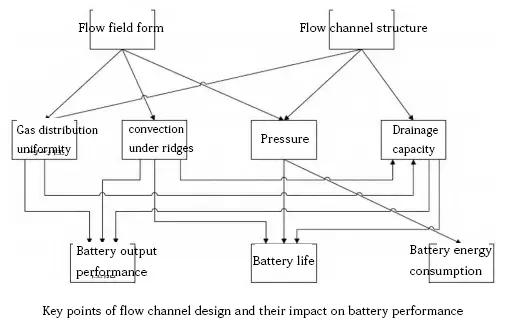
Next, I will provide an overview of the two design key points: flow field form and channel structure of the Bipolar plate. The focus will be on the hotspots and advantages and disadvantages of different channel forms. Through a combination of literature review and simulation studies, I will explain the impact of different channel forms on the performance of the Bipolar plate.
II. Bipolar Plate Channel Forms
Since the early 1970s, the channel shapes of Bipolar plates have been extremely simple, primarily consisting of straight channels and simple serpentine channels. From the 1980s to the present, as researchers delved deeper into the study of Bipolar plate channel structures, they discovered the impact of channel structures on fuel cell performance. More complex channel designs began to emerge, such as multi-serpentine channels, interdigitated channels, grid channels, and even biomimetic channels, as shown in the figure below:
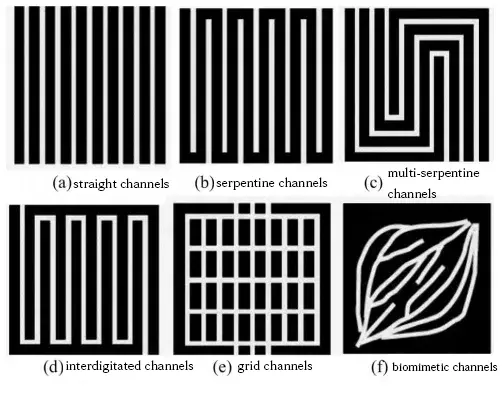
2.1 Straight Channels
Straight channels consist of multiple straight lines distributed in parallel. Their advantages include ease of processing, low flow resistance, and small pressure drop loss at the fluid inlet and outlet. However, due to the parallel design, the pressure difference between channels is small, resulting in weak forced convection between adjacent channels. Consequently, reactive gases mainly rely on diffusion to enter the gas diffusion layer (GDL) for reaction. Moreover, because of the low gas flow rate, liquid water accumulating under the ridges and at the edges of the channels is not easily expelled, leading to electrode flooding, which affects the overall performance of the cell.
Next, based on channels with a depth of 0.4 mm and a width of 0.5 mm, we will study the distribution patterns of pressure drop at the inlets and outlets of channels with different lengths and structures. The figure below shows the relationship between the pressure drop and channel length for channels of varying lengths from 100 mm to 500 mm. It is evident that as the channel length increases, the pressure drop at the inlet and outlet increases linearly. At a flow rate of 10 m/s, the pressure drop increases by about 1.5 kPa for every 50 mm increase in channel length (Note: data sourced from the internet, actual data should be verified accordingly).
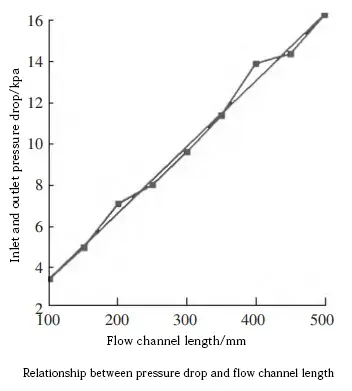
Researchers also compared straight channels of 280 mm length with wavy channels. The study showed that the impact on pressure drop for wavy channels is equivalent to a 200 mm increase in the length of straight channels, proving that wavy channels can increase inlet pressure drop without changing channel length. Additionally, the turbulence caused by the bends in wavy channels results in more uniform fluid distribution. The degree of curvature and the number of bends in wavy channels also affect the pressure drop. This data explains why many manufacturers focus on the improved wavy channel design of straight channels.
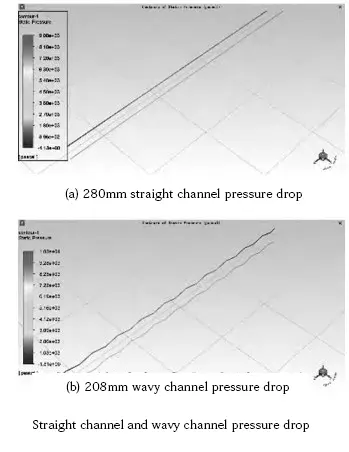
Furthermore, straight channels also include one-into-two and one-into-multiple configurations. The figure below studies the fluid distribution in one-into-two, one-into-four, and one-into-eight scenarios, concluding that a split number of two more easily achieves uniform flow distribution in the flow field.
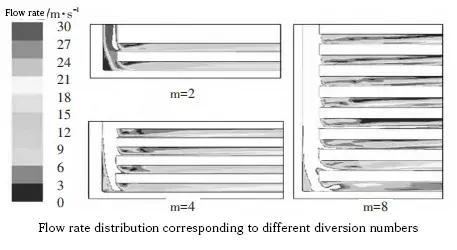
To address the problems with straight channels, channel designers have proposed the following solutions:
1. Reduce the channel size to increase gas flow rate, making it easier to expel generated water and prevent flooding.
2. Introduce abrupt changes in channel cross-sections to increase turbulence, causing gas to expand and contract laterally parallel to the diffusion layer, enhancing the diffusion ability of reactive gases.
3. Add guiding regions to make fluid flow more uniform.
4. Design split flow fields, where fluid is diverted from the main channel into multiple sub-channels and then remerged, increasing pressure drop and improving reactant utilization.
2.2 Serpentine Channels
The single-path serpentine channel was the earliest proposed channel form. This type of channel has the advantages of uniform flow distribution, rapid expulsion of liquid water, and resistance to clogging. However, due to the relatively long length of the serpentine channel, it results in a significant fluid pressure drop, which can easily lead to insufficient mass transfer in the later stages, uneven gas distribution, and non-uniform current density. To address these issues, researchers developed the multi-path serpentine channel design based on the single-path serpentine channel.
While the multi-path serpentine design can improve these issues, it cannot completely solve them. Additionally, the multi-path serpentine channels pose increased processing difficulty. The primary reason is that the serpentine channels are arranged in series and parallel, with a pressure difference between adjacent channels. This causes gas to pass through the Bipolar plate channel ridges and enter another channel via the GDL, leading to a “short-circuit” phenomenon. Moreover, because the length of the serpentine channels remains relatively long, there is still a significant pressure drop at the gas inlet and outlet, resulting in uneven distribution of reactive gases and consequently, uneven current density and heat distribution.
Researchers first studied the impact of single bend positions in serpentine channels on pressure drop. For the same channel length, they examined different bend positions and found that the bend position in serpentine channels has almost no effect on the total pressure drop.
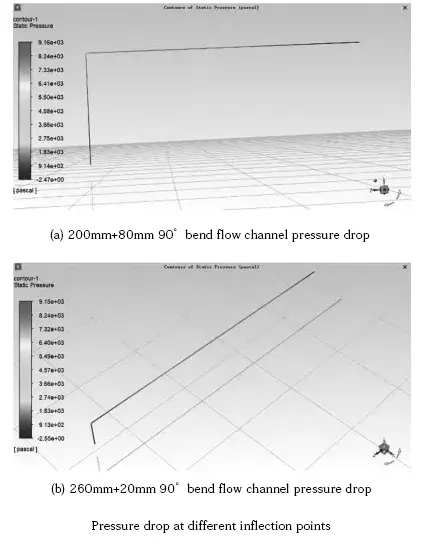
Then, researchers studied the impact of bend angles ranging from 30° to 135° on pressure drop. The results showed that as the bend angle increases, the pressure drop gradually decreases. The pressure drop rate between 30° and 90° is higher than that between 90° and 135°, indicating that the pressure drop rate for acute angle bends is higher than that for obtuse angle bends.
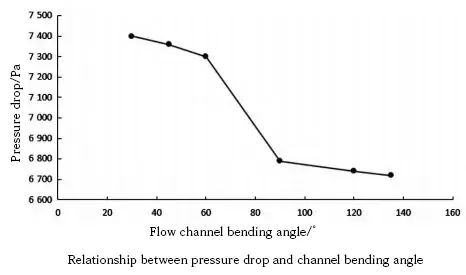
To address the problems with serpentine channels, channel designers have proposed the following solutions:
Densify the channels,
Gradually narrow the middle of the channel,
Expand the outlet,
Add turbulence structures,
Incorporate guiding designs.
These directions aim to optimize the performance and efficiency of serpentine channels.
2.3 Interdigitated Channels
Interdigitated flow fields, also known as discontinuous flow fields, are currently not widely used. This is mainly because the inlet and outlet channels are not connected, requiring the reactive gases to pass through the GDL to exit the channel. This forms strong forced convection under the ridges, expelling water from the GDL and increasing the transport rate of reaction products, significantly enhancing the performance of the fuel cell. However, the forced convection under the ridges results in a very high pressure drop and severe pressure loss at the gas inlet and outlet, which can also damage the catalyst layer. If the design is not reasonable, it is prone to short circuits, reducing the utilization efficiency of reactants and electrodes.
2.4 Grid Channels
Grid channels involve arranging obstacles in a regular pattern on the surface of the Bipolar plate, forming channels that run between the fluid inlet and outlet. This causes the fluid to flow between the obstacles, leading to continuous expansion and contraction of the reactive gases in the flow field, thereby enhancing fluid turbulence. As a result, grid channels enable reactive gases to fully contact the diffusion layer, facilitating efficient heat exchange with the diffusion layer and carrying the heat away. However, because the reactive gases have multiple pathways to choose from, they tend to flow through channels with lower resistance, leading to uneven gas distribution. To address this issue, the shape and layout of the obstacles can be optimized to improve the utilization rate of reactive gases, thereby enhancing fuel cell performance.
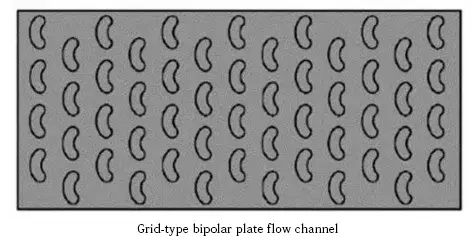
2.5 Biomimetic Channels
Biomimetic channels are typically designed by imitating natural phenomena, such as the distribution of branches on trees, the venation of leaves, or the vascular network in the human cardiovascular system. These designs take full advantage of the uniform fluid distribution found in biological systems, ensuring that the reactive gases are fully utilized. The principle is to arrange the main and secondary channels reasonably, allowing for even distribution of reactive gases. In biomimetic channels, the reactive gases continuously split and merge, creating turbulence and promoting the absorption and utilization of the gases. Although the flow rate in biomimetic channels is lower than in serpentine or interdigitated channels, the pressure drop remains minimal, which further improves the performance of the fuel cell.
III. Structure of Other Parts of the Bipolar Plate
The performance of the Bipolar plate is not only closely related to the channel structure but also influenced by the dimensions of the inlet and outlet areas, the configuration of the reactant transition zone, and the dimensions of the reaction area channels. Next, let’s take a brief look at the impact of the three areas on fuel cell performance.
3.1 Inlet and Outlet Areas
Currently, the inlet and outlet areas of Bipolar plates are mostly located around the periphery. These areas serve as fluid conduction regions, allowing reactive gases and coolant to flow in and out of the Bipolar plate through the channel inlets and outlets. The arrangement and size of these areas are also factors that affect the performance of the fuel cell.
For the arrangement of inlets and outlets, to balance water-thermal management and reactive gas humidity, the inlet and outlet positions of the Bipolar plate are designed such that the low-humidity air inlet is located at the lower temperature side. This allows for humidification through water diffusion from the anode end, while the high-humidity air outlet is at the higher temperature side, corresponding to the low-humidity hydrogen inlet. This overall design is beneficial for the uniform distribution of water content within the fuel cell.
Regarding the dimensions of the inlets and outlets, research indicates that the inlet cross-sectional area should be greater than or equal to the minimum channel cross-sectional area multiplied by the number of channels. Typically, the relative sizes of the inlet and outlet are symmetrical. However, with the development of Bipolar plates, some automotive and power companies have proposed asymmetric fuel cell electrode plates, with the cross-sectional area of the anode and cathode outlets being larger than that of the inlets. This design has shown improved uniformity in the distribution of reactive gases.
3.2 Reactant Transition Zone
The reactant transition zone is the area where reactive gases and coolant enter the reaction zone. Its main function is to guide the flow of these substances into the reaction zone. Some Bipolar plate designs integrate the transition zone with the channels, while others have a separately configured transition zone. The separately configured transition zone often uses a grid/dot matrix distribution of channels, allowing gases to be distributed in the transition zone before entering the channels.
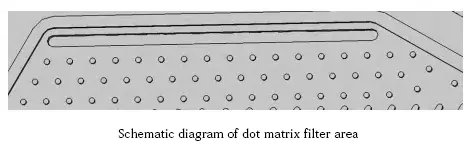
3.3 Reaction Area Channel Dimensions
The dimensions of the channels in the reaction area are crucial parameters that affect the performance of the reactive gases and coolant. The channel dimensions can be divided into channel width, Ridge Width, and channel depth.
3.3.1 Channel Width
Research has shown that different channel widths impact the performance, pressure drop, and gas distribution of the fuel cell as follows:
Reducing the channel width helps to improve the performance of the fuel cell.
A narrower channel width decreases the flow velocity differences between adjacent channels, improving the uniformity of flow distribution.
Reducing the channel size results in a nonlinear increase in the mean oxygen concentration and its uniformity, thereby increasing oxygen conversion rates.
3.3.2 Ridge Width
Based on the conductivity of the electrode and Bipolar plate materials, there is an optimal value for the area of the flow field grooves, meaning the ratio of channel width to Ridge Width has an optimal value. The ratio of groove area to the total area of the Bipolar plate is known as the Bipolar plate’s porosity. Research indicates that the porosity should be between 40% and 75%. A porosity that is too high will lead to excessive contact resistance between the electrode and the Bipolar plate, increasing the cell’s ohmic polarization loss. Conversely, a porosity that is too low will result in an insufficient reaction area due to overly small channel regions.
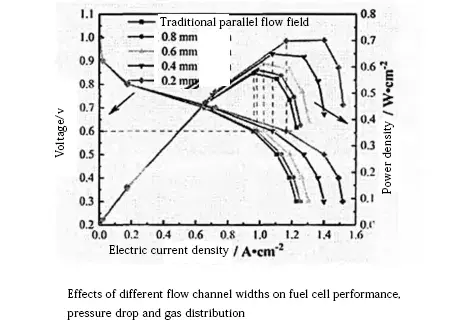
3.3.3 Channel Depth
Studies show that within a certain range, the shallower the channel depth, the better the performance of the fuel cell. However, if the channel is too shallow, it can lead to excessive pressure loss. Considering the effects of channel depth on pressure loss and gas concentration, the optimal performance is achieved when the channel depth is 0.6 mm (this data is based on simulation tests, and actual data may vary with different factors).
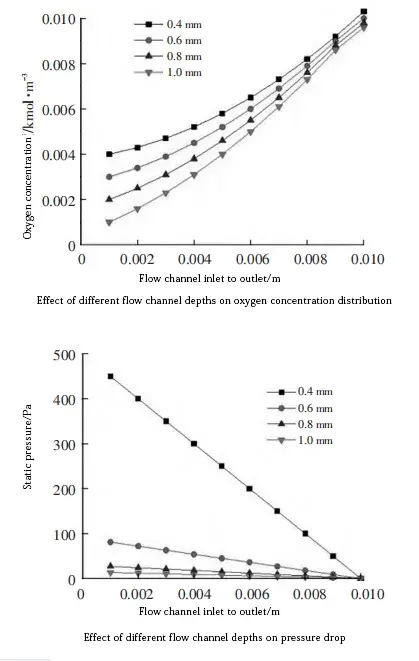
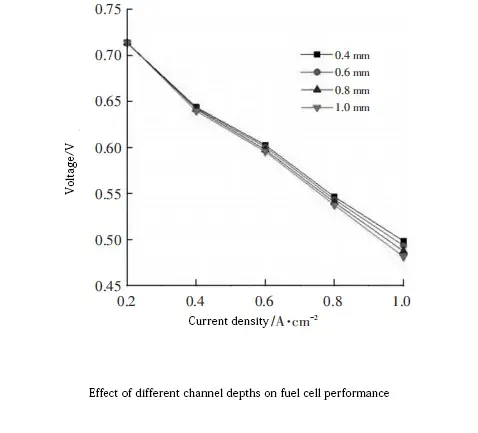
In summary, under conditions of a certain gas flow rate, appropriately reducing the depth and width of the channels can increase gas flow velocity, increase the gas concentration entering the GDL and catalyst layer, and enhance the water drainage and heat dissipation performance of the flow field. However, to avoid excessive pressure loss in the channels and high contact resistance between the Bipolar plate and GDL, the channel width and depth should not be too small.
Outlook
As a crucial component of fuel cells, the Bipolar plate’s channel form and structure directly impact the utilization rate of reactive gases and the performance of the fuel cell. Currently, the most commonly used forms are straight channels and serpentine channels, with improvements mainly focused on the dimensions and structure of these channels.
Among TMN’s custom Bipolar plate clients, in addition to the aforementioned optimizations of channel structure, inlet and outlet areas, reactant transition zones, and reaction area channel dimensions, there are also diverse manufacturing demands for Bipolar plates. Two of the most typical cases are as follows:
Classic Case 1: Surface Coating
This involves electroplating platinum on one side of the Bipolar plate and MMO (Mixed Metal Oxide) on the other side.
Classic Case 2: Dual Depth Channels
This involves etching two different depths of channels on the same side of the Bipolar plate. For example, if the total thickness of the Bipolar plates is 2.0 mm, channels with depths of 0.6 mm and 0.4 mm can be etched on one side, while a 0.5 mm deep channel can be etched on the other side.
TMN invests in research on Bipolar plate manufacturing every year. Manufacturing technology advances with the progress of Bipolar plate development, providing reliable technical support for Bipolar plate R&D. If you are engaged in Bipolar plate research and need technical support, please leave us a message. We will contact you as soon as possible to provide you with the best solutions and advanced technical support.
Learn more about TMN’s bipolar plate technology >>>
Read more related articles:
Understanding Graphite Bipolar Plates: The Key Component of Fuel Cells
Fuel cell bipolar plates materials and manufacturing
Function of bipolar plates in fuel cell
Understanding Metallic Bipolar Plates for PEM Fuel Cells