Sheet metal working is a much broader term that encapsulates numerous processes like punching, bending, welding, gluing, etc. Typically, sheet metal is not a term associated with a specified material. Instead, it is used for the metal taken up to convert into a particular shape. However, the sheet metal working domains are expanding with every passing day and streamlining of newer sheet metal processes and technologies is causing even improved and accurate results.
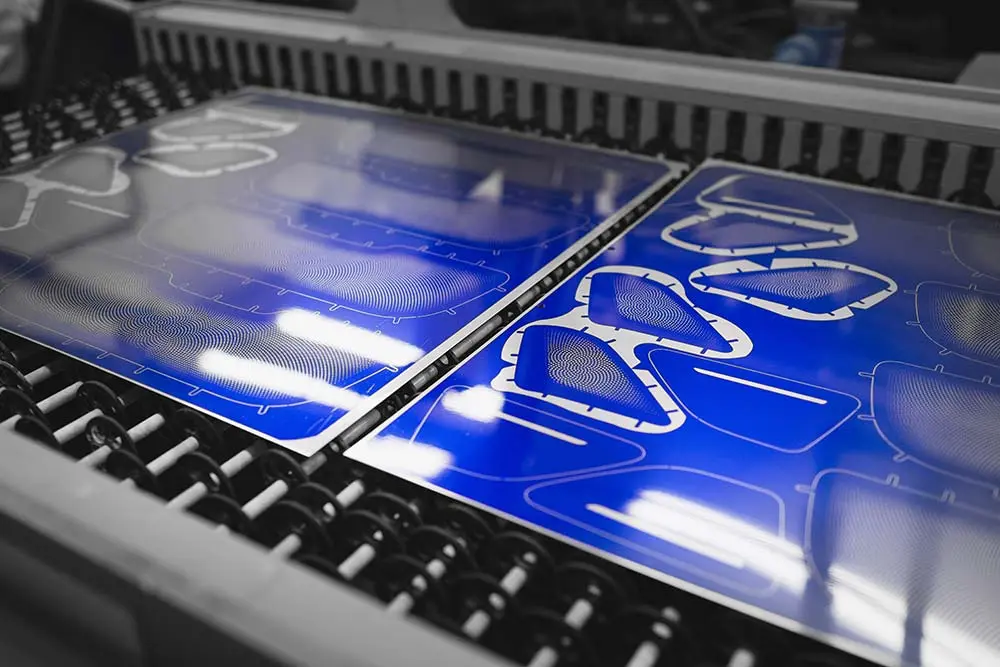
By 2018, the sheet metal market’s global size was around $265 billion, which is expected to grow with a compound annual growth rate of 4.8% by the end of 2025. The real accelerating force behind this much-expected increase in CAGR is the persistent inclusion of new sheet metal technologies.
Though laser technology, waterjets, and flame cutting have done some incredible things for the sheet metal industry, chemical etching is another addition and recently emerged sheet metal technique with its overwhelming benefits. Accordingly, this article will be specified and only talk about chemical etching compared to laser cutting, stamping, and CNC processing.
Chemical Etching Definition: What is Chemical Etching?
Before we move to differentiate chemical etching from laser cutting, stamping, and CNC processing, let us have a brief introduction of chemical etching:
Technically, chemical etching (also known as chemical milling or photochemical etching) is a micro-manufacturing process that uses baths of temperate regulated etching chemicals that remove the material from selective areas on metal workpiece for greater precision and better finishing.
The most appealing aspect of chemical etching is that it can perfectly deal with metals in all shapes, irrespective of their geometry. Metals utilized in chemical etching may include SS steel, titanium, copper, aluminum, nickel, etc.
Secondly, suppose chemical etching is compared with other micro-manufacturing processes like stamping, CNC processing, and Laser cutting. In that case, the earlier will come up as more cost-effective, less time-consuming, and more flexible for the shaping of designs.
By now, chemical etching has become an optimal choice for precise, finished, and accurate metal part manufacturing regardless of industrial production or prototyping. Moreover, many industries, such as aerospace, automotive, electronics, and medical, use metal parts delivered by chemical etching.
Chemical Etching Vs. Laser Cutting
Laser cutting is also a subtractive manufacturing process that supports the same goal supported by chemical etching. To know which is better, let us have a comparison between laser cutting and chemical etching:
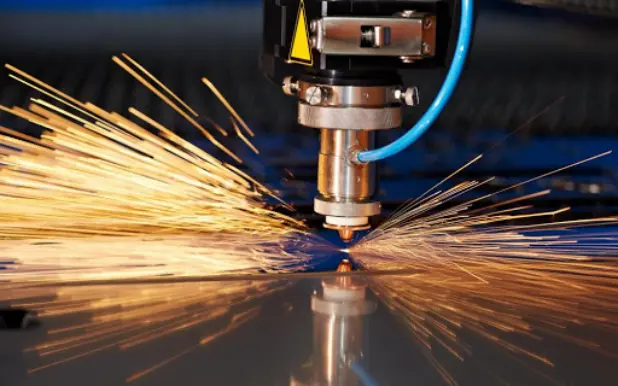
1. Cost-Effectiveness
When it is about prototyping or small volume production, laser cutting comes up as a better choice. However, chemical etching explicitly outclasses laser cutting when it comes to the output at the mass level.
2. Lead Time
The time consumed to form the required product from raw material is called lead time. Laser cutting cannot produce more than one part at a time, while chemical etching supports production at the mass level at one time. When production at a lower level is required, laser cutting may work, but chemical etching is more feasible when production at the mass level is needed.
3. Complexity of Design
As far as complexity of design is concerned, both of the approaches are recommended. But again, laser cutting performs only one operation at a time, while chemical etching offers simultaneous progress for the whole drawing or design.
4. Accuracy
Chemical etching is again the winner in this section as it can harvest ultra-thin metal parts without changing the metal’s internal structure. In contrast, laser cutting brings less accuracy and also causes thermal stresses in the metal.
Chemical Etching Vs. Stamping
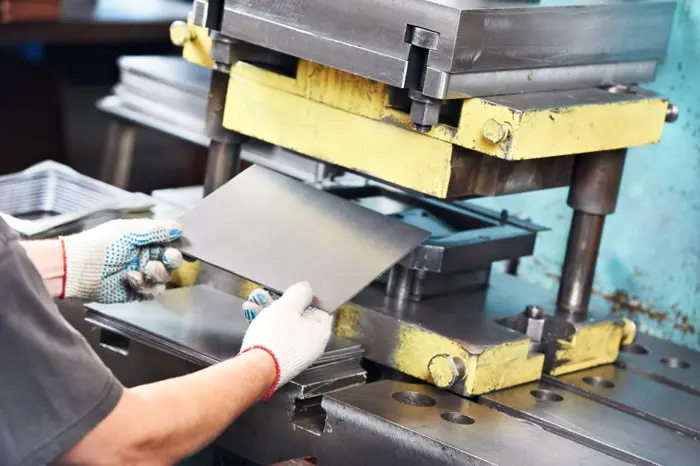
Stamping, which is also known as pressing, is another micro-manufacturing process. This time we will see that if chemical etching is better or stamping:
1. Cost-Effectiveness
For stamping, there needs to incur a massive investment for tooling, and stamping die may involve the acquisition of thousands of dollars. On the other hand, chemical etching does not require these extra costs, so it becomes more cost-effective than stamping.
2. Lead Time
Stamping requires 6-8 weeks only to prepare the tooling, and then more time is needed to set up the tooling in the stamping press. While for chemical etching, it is a matter of few days to get the process completed.
3. Complexity of Design
The flexibility of design might be a standard edge for both of these approaches. Still, tooling costs and lead time of stamping indicate that chemical etching is a better solution to opt for.
4. Accuracy
With stamping, edged parts become burr and rough, and the work-piece accuracy gets damaged. Conversely, chemical etching offers ultra-precise preparation of metal or workpiece.
Chemical Etching Vs. CNC Processing
CNC processing is again a micro-manufacturing process. Let us compare it with chemical etching:
1. Cost-Effectiveness
CNC machines require considerable tooling costs, especially when developing a prototype or production at a smaller scale. Unlike CNC processing, chemical etching adds no cost for tooling. So, chemical etching is more effective than CNC processing regarding costs.
2. Lead Time
Preparing for the tools of CNC is a time-consuming process along with huge costs. CNC processing may consume weeks to get the job done. Paradoxically, chemical etching neither requires tool nor time to set them up, so its lead time is much lower than CNC processing.
3. Complexity of Design
Here chemical etching is again the winner as it offers better options to deal with complex designs. While CNC has certain limitations, and it cannot go beyond these boundaries.
4. Accuracy
With CNC processing, the edges of parts get rough and burr, assigning the finishing work to some extra operations after CNC processing. Nevertheless, chemical etching offers immensely more accurate results than CNC processing.
Conclusion
Chemical etching comes up as one of the most suitable solutions for improved, cost-effective, and less time-consuming results regarding your sheet metal operations. Now, this is the time to quit the conventional approaches to get your sheet metal operations done, as you have much better options in the form of chemical etching.
Concerning that, TMN is an experienced chemical etching company. It has been a long time since we offer our services to our respected customers, creating precision thin and complex metal parts like EMI/RFI shielding, lead frame, speaker grilles, mesh filters, encoder disks, and shims/washers/spacers. In this way, if you are searching for the best and customized chemical etching service or want to learn more about it, our experts are at your service to answer and meet all your requirements.