Summary:The development of Proton Exchange Membrane Fuel Cells (PEMFCs) is showing great potential to become a clean, efficient, and reliable power source. Bipolar plates, one of the key components of PEMFCs, play a critical role by providing electrical connections, delivering reactant gases, dissipating reaction heat, and removing byproducts. However, they are also a significant contributor to the overall cost of PEMFCs.
Depending on the material used for bipolar plates, they can be classified into metallic, graphite, and composite. This article reviews the various bipolar plate materials and their manufacturing processes. Among these, metallic bipolar plates are gaining attention in passenger vehicle applications due to their superior mechanical and physical properties, as well as their cost advantage compared to porous graphite and composite materials. However, the main concerns for metallic bipolar plates are their manufacturing process and corrosion resistance.
Looking ahead, the development of advanced corrosion-resistant and conductive coatings, or innovative metallic materials for bipolar plates, will greatly enhance the adoption of PEMFCs in passenger vehicles.
Due to constraints in durability and cost, Proton Exchange Membrane Fuel Cells (PEMFCs) have not yet achieved large-scale commercial application, with bipolar plates being one of the critical components limiting their feasibility. Typically, bipolar plates account for over 80% of the total stack mass, approximately 30% of the total cost, and occupy most of the stack’s volume.
In terms of structure, bipolar plates in a fuel cell perform six fundamental functions:
1. Separating individual cells within the stack;
2. Delivering reactant gases;
3. Providing electrical connections;
4. Removing water byproducts;
5. Dissipating reaction heat;
6. Withstanding clamping forces.
To meet these functional requirements, the U.S. Department of Energy (DOE) has set specific targets for the characteristics of bipolar plates for the years 2020 and 2025, as shown in Table 1. According to the latest Fuel Cell Technologies Office roadmap, the current cost for bipolar plates is approximately $5.4 per kW, significantly exceeding the DOE’s 2025 target of $2.0 per kW. This indicates that to achieve the DOE’s goals, bipolar plate materials must become more affordable while maintaining high electrical and thermal conductivity, low contact resistance, and good corrosion resistance.
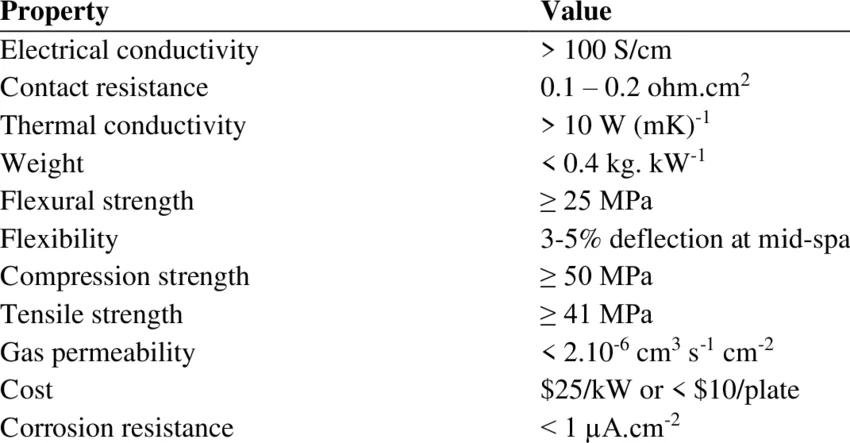
Bipolar plates can be categorized into metallic, graphite, and composite based on the materials used. In China, graphite bipolar plates are currently the most commonly used in Proton Exchange Membrane Fuel Cells (PEMFCs). However, metallic bipolar plates are gaining attention due to their potential for significant cost reduction with large-scale production and their compactness, especially in high-power stacks, compared to graphite plates. On the other hand, composite bipolar plates are being phased out due to challenges in mass production and high costs.
This paper provides a comprehensive review of graphite, metallic, and composite bipolar plates, discussing their characteristics, manufacturing processes, and preparation methods. It also explores the different coatings used for metallic bipolar plates. Finally, the paper outlines the applications of fuel cells based on these various types of bipolar plates.
Graphite Bipolar Plates
Graphite is currently the predominant material used for bipolar plates in China due to its high electrical conductivity, chemical stability, thermal stability, and corrosion resistance. However, as a porous and brittle material, graphite has low strength and high brittleness, which makes it challenging to meet the gas-tightness requirements of bipolar plates. To overcome these limitations, graphite must undergo multiple cycles of impregnation and carbonization to create non-porous graphite plates.
Non-porous graphite plates are typically made by graphitizing carbon/graphite powder and graphitizing resin at high temperatures (around 2,500 °C). This process requires a precise temperature ramp-up schedule, resulting in a lengthy production cycle and high costs. Additionally, the graphitization process can lead to new porosity due to the evaporation of impurities, which can result in a porosity rate of 20% to 30% on the graphite plate surface. The presence of pores increases the risk of PEMFC leaks, which can reduce the concentration of reactant gases and, subsequently, decrease stack performance. To mitigate these risks, the graphite plates are impregnated to reduce porosity and improve surface quality. A widely used solution is the repeatedly impregnated non-porous graphite plate.
Figure 1 illustrates a comparison of current density (J) and voltage (U) curves in a fuel cell stack before and after impregnation. It is evident that the stack’s performance is significantly improved when assembled with impregnated graphite bipolar plates.
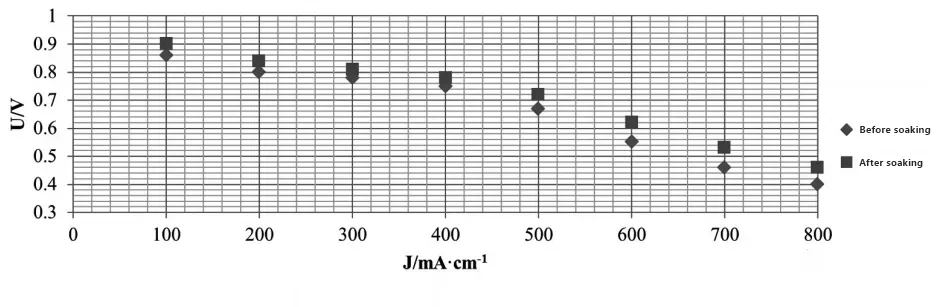
Machined Graphite Plates
Machined graphite plates are typically produced by mechanically processing synthetic graphite. The manufacturing process involves the following key steps:
1. Raw Material Preparation: Coke and pitch are mixed and carbonized at a temperature between 1,000 and 1,300 °C to form carbon material. This material is then impregnated with pitch and baked, followed by graphitization in an electric furnace at temperatures ranging from 2,500 to 3,000 °C.
2. Slicing: The raw graphite material is roughly sliced into plates according to the required dimensions for bipolar plates.
3. Impregnation: The sliced graphite plates are impregnated with resin to fill surface and internal pores. Typically, the plates are immersed in resin for about 24 hours, followed by heat treatment to solidify the resin. Depending on the type of resin used, this process can be divided into phenolic resin impregnation and furfuryl alcohol resin impregnation, among others.
4. Grinding: After slicing and impregnation, the graphite plates require grinding to achieve the desired smoothness. This involves rough, medium, and fine grinding to ensure the correct dimensions and surface quality.
5. Etching/Machining: This step is crucial in the processing of bipolar plates. The precision of the etching or machining process determines the dimensional tolerances and the quality of the flow channels on the plates.
Due to the low strength and brittleness of graphite, this processing method is not ideal for producing ultra-thin bipolar plates (less than 1.5 mm). Additionally, excessive friction between the tooling and graphite can result in suboptimal dimensional accuracy and surface quality. During the machining process, graphite can fracture into small particles and fine dust, exposing cutting tools to high impact and compression stress. The need to machine complex flow channels further adds to the overall cost. As a result, this method has gradually fallen out of favor in many countries, where most manufacturers now use injection molding or compression molding for production.
Injection-Molded Graphite Plates
Injection-molded graphite plates are produced by mixing a specific proportion of graphite with resin. This mixture is fed into an injection molding machine’s hopper, where it is heated and melted. The molten mixture is then injected into a closed mold under pressure, and after cooling and solidification, the product is removed from the mold. To increase the electrical conductivity of these bipolar plates, metal powders can be added to the mixture, and carbon fiber or ceramic fiber can be used to improve mechanical strength. However, injection molding has several drawbacks, such as prolonged debonding times (up to 7 days), cracking in thick sections, size limitations, and defects. Further graphitization can enhance the performance of the plates, but this significantly increases the cost, making this method less suitable for large-scale production.
Compression-Molded Graphite Plates
To address high processing costs and improve scalability, researchers have turned to compression molding for bipolar plate production. This process begins with preparing a mixture of graphite powder and resin, followed by pre-treatment of both the mixture and the mold. Using a specific temperature and pressure, the powder is melted and flows into the entire cavity of the mold, ensuring complete coverage. The bipolar plate is removed from the mold after curing. If the binder is a thermosetting plastic, it generally requires only a few minutes to cure before demolding. If a thermoplastic binder is used, the mold must be cooled to below the binder’s melting point before demolding.
Overall, the market demand for graphite bipolar plates remains high, but issues with porosity, costs, and long processing times still need improvement. Additionally, to reduce resistance to current and heat conduction, bipolar plates should be as thin as possible while maintaining adequate mechanical strength and a good barrier to gases. Considering the current use of hydrogen fuel cell vehicles in China, commercial vehicles like buses, logistics trucks, sanitation vehicles, and forklifts are the primary target markets. The high-frequency use of these commercial vehicles demands greater durability from their components, making graphite bipolar plates a suitable choice for fuel cell applications. Graphite plates are valued for their long lifespan, making them a preferred option for fuel cell commercial vehicles in demonstration operations.
Shanghai Hongfeng, a Chinese company, has developed graphite bipolar plates with a thickness of just 1.4 mm while maintaining performance, reaching power density levels approaching those of Toyota’s first-generation metal bipolar plates.
Metal Bipolar Plate
Compared to graphite bipolar plates, metallic bipolar plates are gaining popularity due to their excellent electrical and thermal conductivity, machinability, fewer manufacturing steps, and potential to produce ultra-thin bipolar plates. Additionally, mass production processes are well-established, allowing for significant cost reductions with large-scale manufacturing. So far, stainless steel, aluminum alloys, titanium alloys, nickel alloys, copper alloys, and metal-matrix composites have been used in the production of metallic bipolar plates. However, metallic plates are prone to corrosion, necessitating protective surface coatings.
Photochemical Etching and Stamping and Hydraulic Forming Processes
Photochemical Etching
Photochemical etching involves the use of chemicals to remove specific areas of a metal plate, creating precise patterns and features. This process is commonly used for its high accuracy and ability to produce intricate designs. Key advantages include:
High Precision: Photochemical etching allows for very fine detail, making it ideal for complex geometries and intricate flow fields.
No Mechanical Stress: As this is a non-contact process, there’s minimal distortion or stress on the metal plate, ensuring dimensional accuracy.
Flexibility: It is easy to change designs without the need for significant tooling modifications, offering flexibility for prototyping and small production runs.
Stamping
Stamping involves using a die and press to shape metal into desired forms. This method is known for its efficiency and cost-effectiveness in large-scale production. Stamping is typically chosen for its:
High Production Speed: Stamping is a quick process, making it suitable for high-volume manufacturing.
Cost-Effectiveness: Once the die is created, the per-unit cost drops significantly, making it a preferred method for mass production.
Consistency: Stamping ensures uniformity across large quantities, maintaining consistent quality and tolerances.
Hydraulic Forming Processes
Hydraulic forming uses hydraulic pressure to shape metal plates, typically by pressing them against a form or die. This method is valued for its ability to create complex shapes and deep contours. Benefits of hydraulic forming include:
Versatility: Hydraulic forming can produce complex geometries and is suitable for a wide range of metal thicknesses.
Reduced Tooling Costs: Compared to stamping, hydraulic forming often requires less complex tooling, which can lead to lower initial setup costs.
Less Material Waste: This process can be more efficient in terms of material usage, reducing scrap and overall costs.
Coatings for Metallic Bipolar Plates
Despite the many advantages of metallic bipolar plates, they are more prone to corrosion, which can adversely affect their performance and durability. Corrosion in metallic bipolar plates occurs because, at the anode, the reducing environment can reduce the protective metal oxide layer, forming hydrides and causing the metal to dissolve in water. This process allows metal to be carried into the fuel stream, potentially increasing the risk of proton exchange membrane contamination and adversely affecting the catalyst layer’s activity. At the cathode, the oxidizing environment significantly increases the corrosion rate, leading to performance degradation and premature stack failure.
Toyota Motor Corporation pioneered the use of metallic bipolar plates with protective coatings in its Mirai fuel cell vehicle, solving various issues such as corrosion, cost, and conductivity. The coatings used on metallic bipolar plates can be broadly categorized into two types:
1. Carbon-Based Coatings: This includes graphite coatings.
2. Metal-Based Coatings: This encompasses precious metal coatings, metal carbides, metal nitrides, and metal oxides.
Several process routes are used to apply these coatings, including electroplating, chemical plating (such as hot-dip plating, spray coating), chemical vapor deposition (CVD), and physical vapor deposition (PVD). In China, PVD is commonly used for metallic bipolar plate coatings due to its high purity, good density, strong adhesion with the substrate, and insensitivity to the base material, making it a preferred surface modification technique.
Composite Bipolar Plates
Composite bipolar plates combine the benefits of graphite and metal plates, offering low density, corrosion resistance, and ease of molding. However, they face challenges with long processing times and limited long-term reliability, affecting their widespread adoption. Composite bipolar plates can be divided into two types: structural composite bipolar plates and material-based composite bipolar plates.
Structural Composite Bipolar Plates
Structural composite bipolar plates use thin metal or other high-strength, high-density conductive plates as separators, with porous thin carbon plates or metal mesh as the flow field plates, bonded with conductive adhesives. This composite structure combines the strengths of metal and graphite plates: metal plates provide strength and durability, while graphite plates create flow channels without needing high density or reinforcement. The inclusion of graphite also reduces the metal’s direct exposure to corrosive environments, mitigating corrosion risks. However, the production process is complex, and sealing is relatively more challenging.
Material-Based Composite Bipolar Plates
Material-based composite bipolar plates are primarily formed by mixing graphite powder/enhanced fibers with thermoplastic or thermosetting resin to create a preform, which is then cured or graphitized. Composite bipolar plates can be further divided into carbon-based composite bipolar plates and metal-based composite bipolar plates. Table 4 provides a comparison between metal-based and carbon-based composite bipolar plates.
Carbon-based composite bipolar plates can adjust conductivity and mechanical strength based on the ratio of conductive fillers to resin, allowing for cost-effective production through compression or injection molding. This approach offers considerable potential for future applications. Metal-based composite bipolar plates usually use metal as the separator, with plastic, polycarbonate, or other materials to reduce weight. Conductive adhesives bond the plastic frame to the metal separator, and porous thin carbon plates or graphite plates, produced through injection molding or sintering, serve as the flow field plates.
Although metal-based composite bipolar plates combine the advantages of graphite and metal plates, their complex structure and production process make mass production challenging, with costs significantly higher than carbon-based composite bipolar plates. This limits their adoption in PEMFC applications, but they offer unique advantages in specific scenarios where their robust structure and durability are needed.