To understand the impact of photochemical etching on precision manufacturing, it’s essential first to clarify what photochemical etching and precision manufacturing are. How are they related? These questions need to be answered step by step to fully recognize the significant role of photochemical etching in precision manufacturing.
What is Photochemical Etching?
Photochemical etching is a high-precision metal processing technology that uses photosensitive materials and chemical solutions to selectively etch metal surfaces. The specific steps are as follows: First, the metal surface is coated with a photoresist, and then UV exposure/development transfers the designed pattern onto the photoresist. Next, the metal material is placed in an etching solution, where the unprotected parts by the photoresist are etched away. Finally, the excess photoresist material is removed, resulting in a precise metal pattern.
Photochemical etching, known for its high precision, ability to process complex patterns, and absence of mechanical stress, is widely used in the field of precision manufacturing. It can process metals at the micron level, making it suitable for producing electronic components, medical devices, and micro-mechanical parts. Additionally, photochemical etching can process various metal materials, including stainless steel, aluminum, copper, and titanium. It offers high efficiency, low cost, and no mold fees, making it particularly suitable for small to medium-scale production and rapid prototyping.
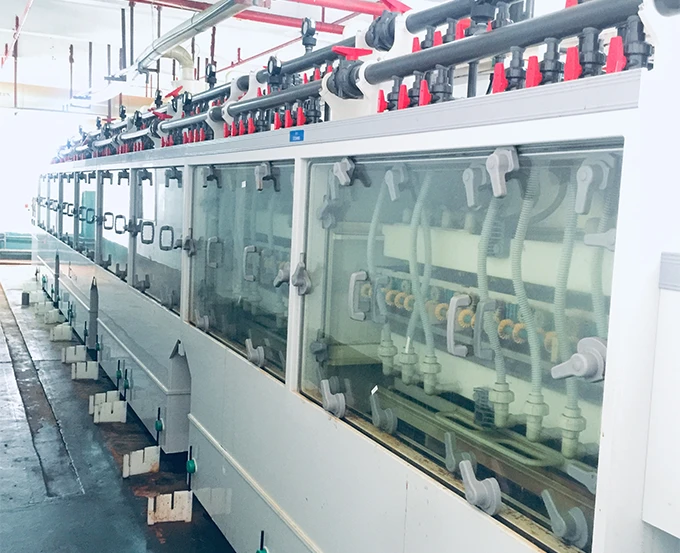
What is Precision Manufacturing?
Precision manufacturing is a technology emphasizing high accuracy and quality, capable of producing components and products with high dimensional accuracy, complex shapes, and excellent performance. The goal of precision manufacturing is to ensure that each component’s dimensions and shape meet the design requirements through high-precision processing methods and strict quality control. This, in turn, satisfies high standards of performance, reliability, and durability.
Precision manufacturing focuses on producing parts and products with high dimensional accuracy, complex shapes, and excellent performance. Its goal is to ensure that each component’s dimensions and shapes meet the design requirements through high-precision processing methods and strict quality control, thereby meeting high standards of performance, reliability, and durability.
Precision Manufacturing Processes
Precision manufacturing encompasses a variety of high-precision processes and technologies, with photochemical etching being a significant technique due to its advantages of high precision, high flexibility, and low stress. It provides an effective method for manufacturing complex and delicate metal parts. Besides photochemical etching, other common processes include:
CNC Machining: CNC machining is a method of high-precision processing controlled by computer programs. CNC technology can handle various materials, including metals, plastics, and composites, and is widely used in aerospace, automotive manufacturing, and medical device industries.
Laser Cutting and Welding: Laser cutting uses a high-energy laser beam to melt and vaporize materials, achieving high-precision cutting and complex shape processing. Laser welding uses a laser beam to rapidly melt and solidify metals, achieving high-strength and high-precision weld joints. This technique is widely used in electronics and the automotive industry.
Precision Grinding: Precision grinding removes small amounts of material from the surface using a grinding wheel to achieve high precision and high surface quality. This process is widely used in manufacturing precision bearings, optical lenses, and aerospace engine parts.
Electrical Discharge Machining (EDM): EDM uses electrical discharge to remove material and is suitable for machining hard alloys and superhard materials. This process is particularly suitable for manufacturing complex shapes and precision microstructures, such as molds and micro parts.
Precision Stamping: Precision stamping is a process where metal sheets are stamped into the desired shape using molds and pressure. It is widely used in electronic components and automotive parts, achieving high consistency and mass production.
Precision Injection Molding: Precision injection molding is a process where plastic or other materials are injected into a mold and solidified through high temperature and high pressure. This process can produce plastic parts with high dimensional accuracy and complex shapes, widely used in consumer electronics, medical devices, and automotive components.
Photochemical etching, as a high-precision and highly flexible processing technique, along with CNC machining, laser cutting and welding, precision stamping, and precision injection molding, constitutes the core technologies in the field of precision manufacturing. Each process has its advantages and can be selected and applied based on specific processing requirements and material characteristics, ensuring that precision manufacturing meets the high-quality and complex part demands of various industries.
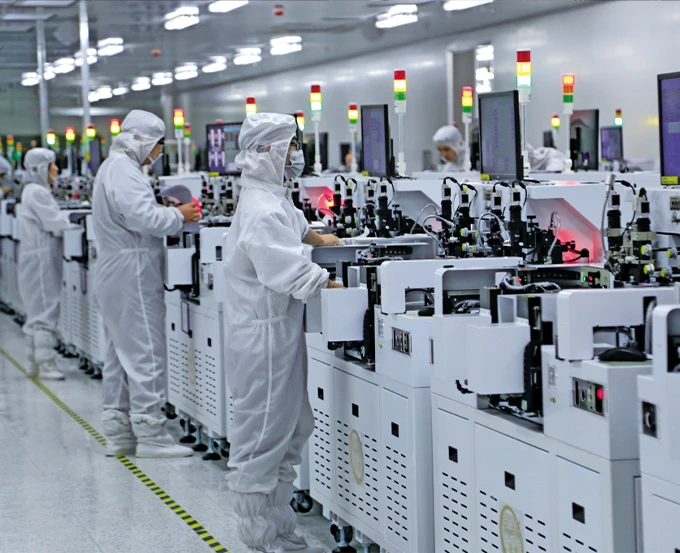
The Impact of Photochemical Etching on Precision Manufacturing
With the advancement of societal processes, components are becoming increasingly smaller, and precision is becoming more critical. Traditional manufacturing processes often struggle to meet these emerging demands. As a result, precision manufacturing has become a hot topic, focusing on how to maintain high precision and consistency at a microscopic level, posing a significant challenge to the manufacturing industry.
Challenges in Precision Manufacturing
In precision manufacturing, the challenges extend beyond issues of size and accuracy to include material selection and process control. Traditional mechanical processing methods such as turning, milling, and grinding, although capable of providing high precision, are limited in efficiency and precision when dealing with complex geometries, ultra-thin structures, and micro features. This limitation is particularly pronounced in high-tech fields such as electronics, medical devices, and aerospace, where the demand for miniature components is continually increasing, making it difficult for traditional manufacturing processes to meet these high standards.
Advances in Photochemical Etching Technology
Photochemical etching is a precision machining method based on photolithography technology. It uses photosensitive materials and chemical etching processes to achieve high-precision micro-machining on both metal and non-metal materials. Compared to traditional mechanical processing, photochemical etching has the following significant advantages:
High Precision and Complex Pattern Processing: Photochemical etching can easily achieve micron-level precision and process complex two-dimensional and three-dimensional patterns. This provides unique advantages in microelectronics, micro-electro-mechanical systems (MEMS), and precision instrument manufacturing.
No Mechanical Stress and Thermal Effects: During photochemical etching, there is no mechanical contact or heat generation, thus avoiding the introduction of mechanical stress and thermal deformation, ensuring high precision and high performance of the processed parts.
Wide Material Compatibility: Photochemical etching is suitable for various materials, including stainless steel, copper, aluminum, titanium, and some non-metallic materials such as glass and ceramics. This offers a broader range of material choices for precision manufacturing.
High Efficiency and Low Cost: Photochemical etching can mass-produce high-precision parts in a short time, reducing production costs and increasing production efficiency.
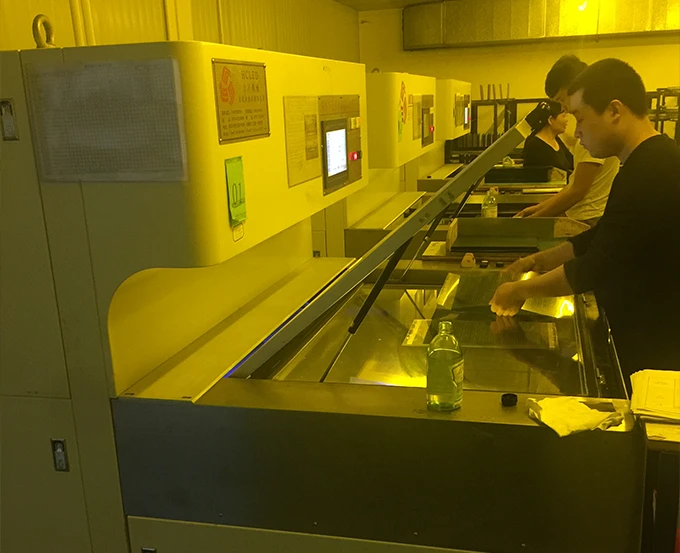
Photochemical Etching Drives the Development of Precision Manufacturing
As photochemical etching technology continues to evolve, many challenges in the precision manufacturing industry have been effectively addressed. The widespread application of this technology has not only improved the manufacturing precision and complexity of components but also significantly shortened the product development and production cycles. TMN has summarized several key impacts of advancements in photochemical etching on precision manufacturing:
Promoting Miniaturization and High Integration: Photochemical etching can achieve ultra-small size and high-density integration of components, enabling the development and production of miniaturized and highly integrated products.
Improving Product Reliability and Performance: Since photochemical etching does not produce mechanical stress or thermal effects during the process, the manufactured components have higher reliability and stability, extending the product’s lifespan and enhancing overall performance.
Driving Innovation and Diversified Applications: The high precision and flexibility of photochemical etching play a crucial role in the development of new materials, new processes, and new products, driving continuous innovation and diversified applications in precision manufacturing technology.
The continuous advancement of photochemical etching technology provides robust support for precision manufacturing. By overcoming the limitations of traditional processing methods, photochemical etching has driven the development of precision manufacturing, leading to breakthrough progress in various fields. With the ongoing development and refinement of this technology, photochemical etching is expected to achieve sub-micron level processing in the future, playing an even more critical role in precision manufacturing.
Read more:
Photochemical etching: an efficient, precise and flexible solution
How To Choose Between Metal Etching and Metal Engraving?
Stainless Steel Etching Process: How to Choose Stainless Steel Etching