The stainless steel etching process involves creating a photomask on the metal using a photoresist, and then selectively removing unwanted stainless steel metal through chemical agents to produce precision components. Stainless steel is a popular metal material in both traditional metal processing and the photochemical etching field. So why choose the photochemical etching process? What are its advantages?
Advantages over traditional metal sheet processing techniques:
1. Avoids deformation or material property changes: Since the process doesn’t involve pressure or cutting, no force or heat is generated during processing, perfectly preserving the characteristics of stainless steel.
2. High precision: The process uses computer-designed patterns and markings, allowing the production of extremely fine and complex parts, ideal for high-precision applications such as medical devices and electronic components.
3. High flexibility: It can process stainless steel materials of any thickness or shape, especially thin metal sheets, which traditional metal processing techniques are not suitable for.
How the stainless steel etching process works:
First, the required images are designed/created using computer CAD software. The stainless steel plates are prepared, cleaned, and coated with a photosensitive photoresist layer. Then, the designed pattern is exposed onto the photoresist using ultraviolet light, engraving the required design. Next, the stainless steel is etched using an etching solution, and finally, the formed stainless steel components are removed, cleaned, and inspected.
Since the design is done using computer CAD software, no metal molds are required, significantly saving on expensive mold costs. When you need to optimize or adjust a part of the image, you can easily and quickly make adjustments and proceed with production without incurring any additional costs.
These advantages enable you to achieve low-cost, high-efficiency design and optimization. Therefore, if you have needs for stainless steel design or customization, you can confidently choose the stainless steel etching process. At this point, you can learn about TMN’s stainless steel etching process.
Chemical Etching Makes Your Stainless Steel Products More Refined
Chemical etching is a symbol of economy and efficiency in metal processing. No matter how complex or fine the product is, it can be manufactured at the lowest cost and completed within a few days.
Etching Stainless Steel Components
The stainless steel etching process is suitable for manufacturing any stainless steel components with a thickness between 0.1 mm and 2.0 mm. Over more than a decade of metal processing, TMN has produced the following types of products.
Filter Meshes and Screens
Using stainless steel etching to manufacture filter meshes has significant advantages, allowing the production of high-precision, diverse, and aesthetically pleasing filter mesh products. No matter how complex the patterns and shapes are, there is no need for expensive custom molds, thus producing filter meshes with uniform and consistent apertures.
Compared to stamping, which requires mold costs and has limited capabilities for complex patterns; compared to laser cutting, which generates a heat-affected zone during cutting, altering material properties and having a slow processing speed; and compared to water jet cutting, which may not be as fine and efficient as photochemical etching when dealing with thin metal stainless steel, stainless steel etching stands out.
Learn more about TMN’s Filter Meshes and Screens >>>
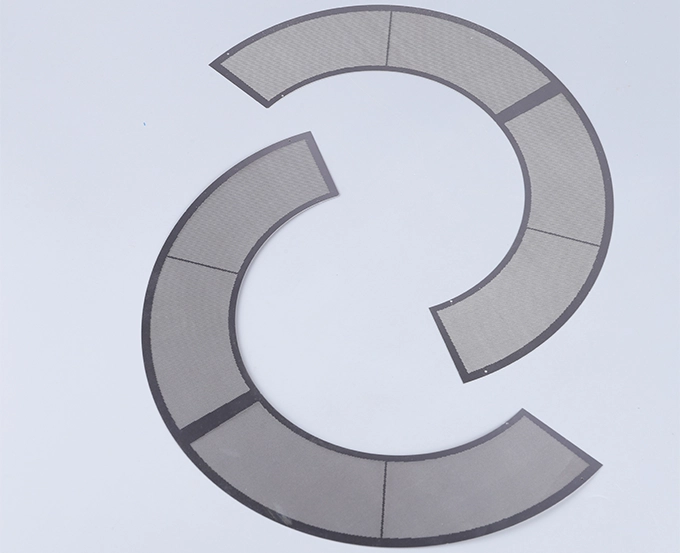
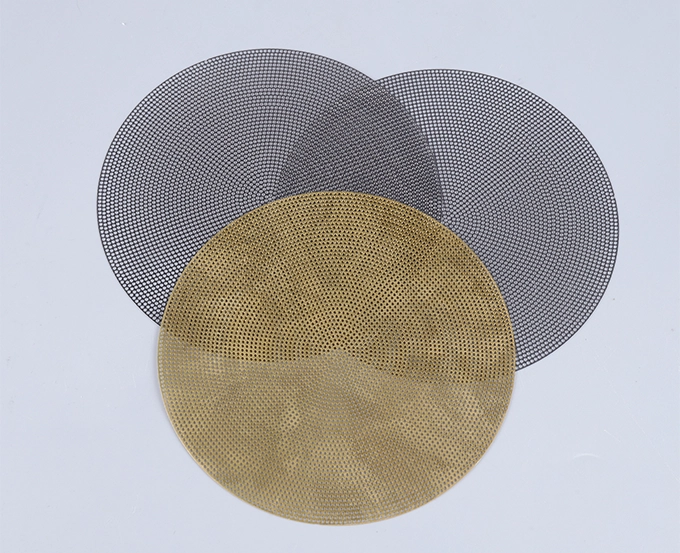
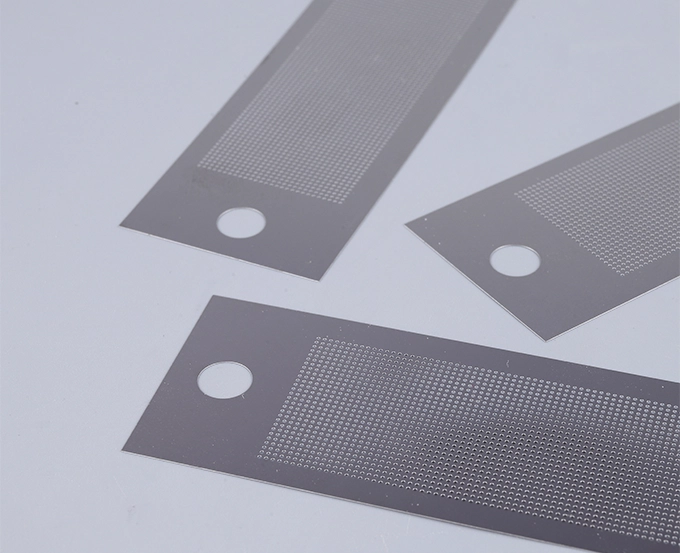
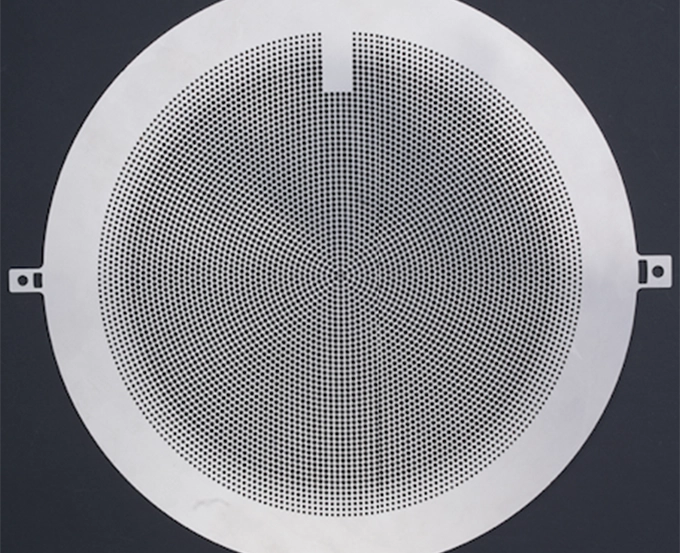
Nameplates, Signs, and Decorations
In the manufacturing of nameplates, signs, and decorations, it is essential to ensure that these metal products are corrosion-resistant, highly precise, and especially aesthetically pleasing and clear. The stainless steel etching process can easily meet these requirements. During processing, there is no contact between metals, no deformation due to uneven force, and no heat-affected zones altering material properties, ensuring that the surface of the produced nameplates, signs, and decorations is smooth, burr-free, aesthetically pleasing, and tactile.
Although stamping and laser engraving are also suitable for manufacturing nameplates, signs, and decorations, stamping has lower precision, easily produces burrs requiring subsequent processing, applies high mechanical pressure leading to deformation, and has high mold costs. Laser engraving is slower and generates heat-affected zones, affecting the overall project development progress and incurring higher costs.
Learn more about TMN’s Nameplates, Signs, and Decorations >>>
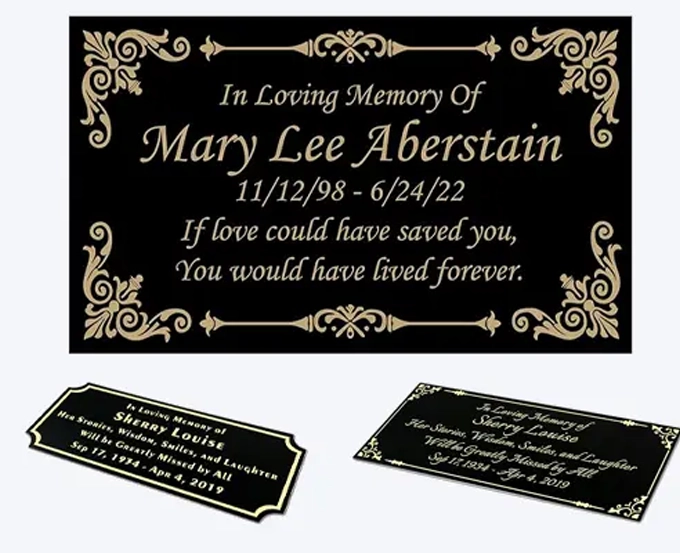
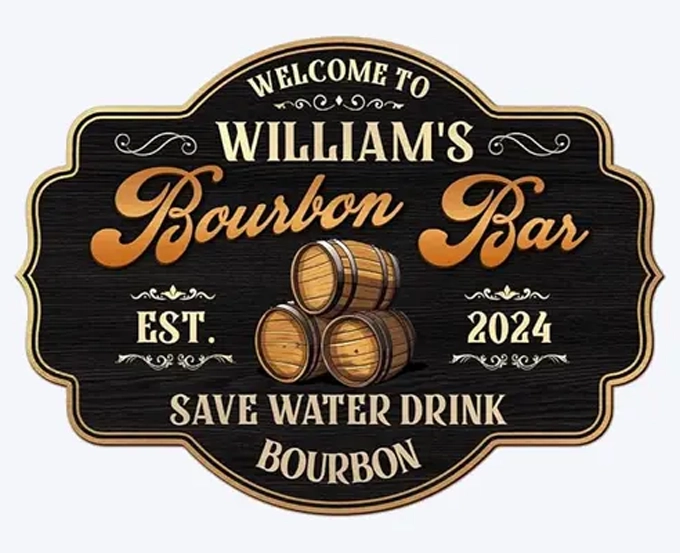
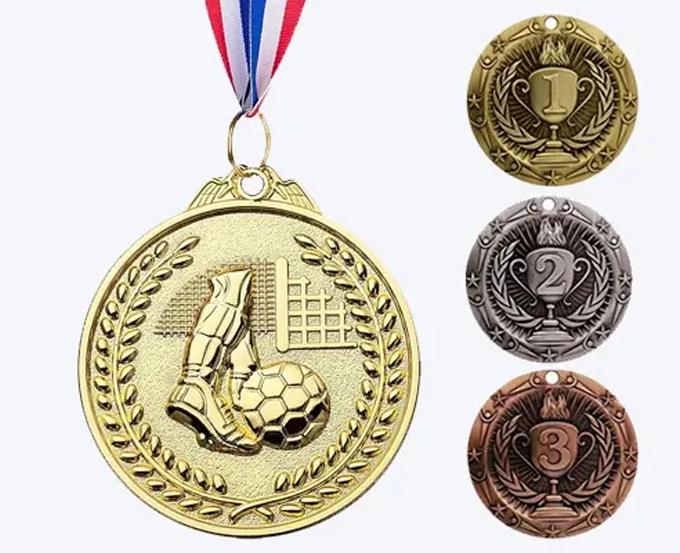
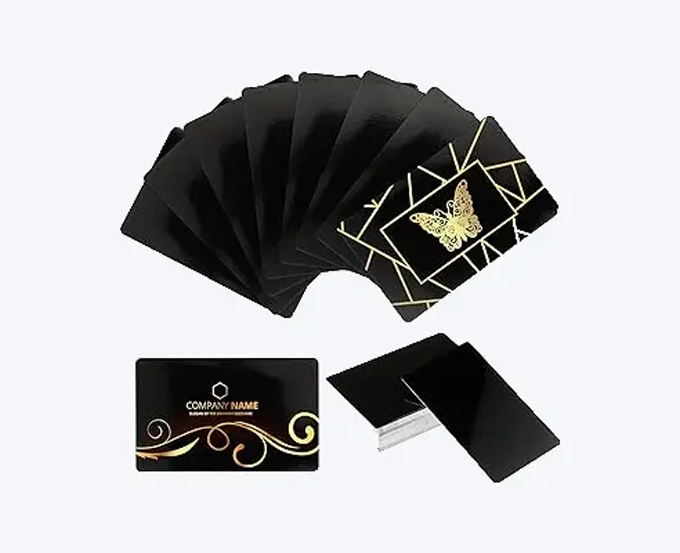
Fuel Cell Bipolar Plates
With the development of new energy vehicles, the manufacturing of fuel cell bipolar plates has become increasingly stringent. If the flow channel precision of the bipolar plates is poorly controlled due to the choice of processing technology, it will significantly reduce the overall performance of the fuel cell.
The stainless steel etching process can achieve the extremely high precision requirements for bipolar plates, suitable for processing complex structures and fine channels. After processing, both the channels and the metal surface are extremely smooth, burr-free, and have neat edges, reducing the resistance to gas or liquid flow and improving the performance of the fuel cell.
In comparison, although CNC machining and stamping are also suitable for manufacturing bipolar plates, their high mechanical stress during processing may lead to material deformation and burr generation. Additionally, most bipolar plates may be in the development stage, and any modification to the channel structure cannot be done as efficiently and cost-free as with photochemical etching. Therefore, photochemical etching is more suitable for the manufacturing of bipolar plates.
Learn more about TMN’s fuel bipolar plates >>>
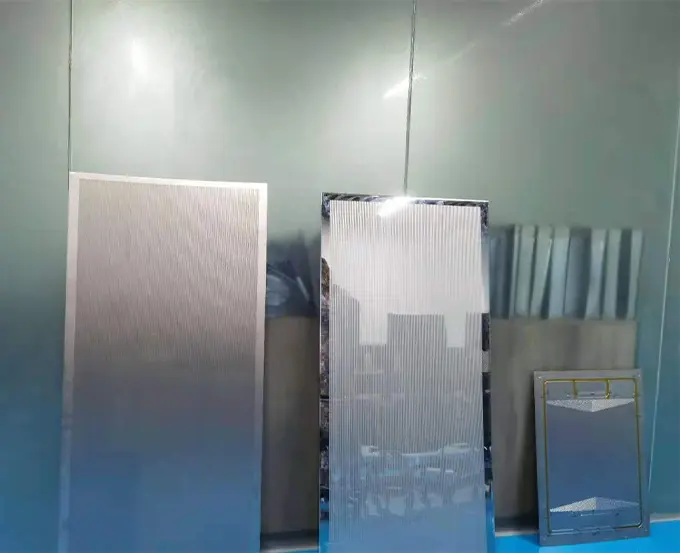
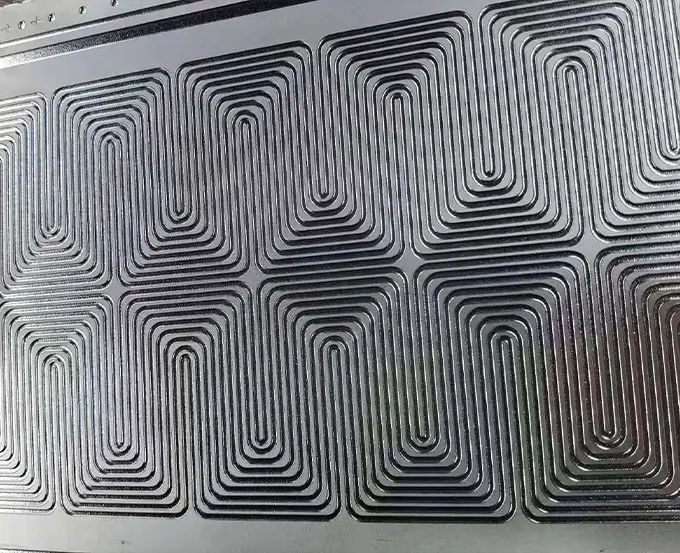
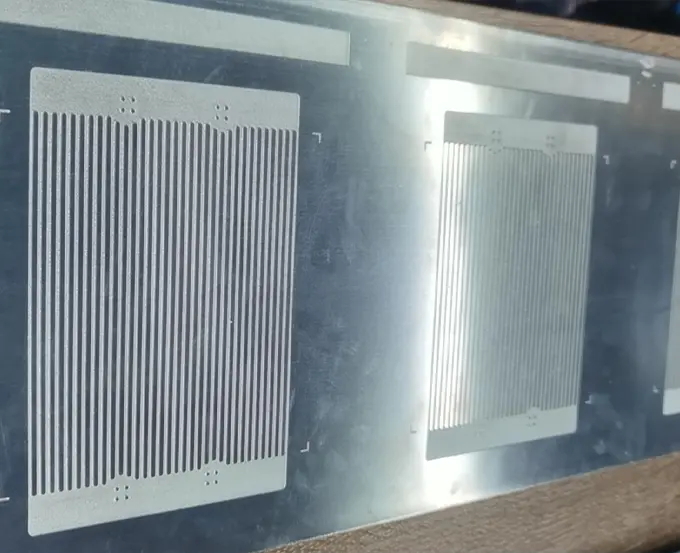
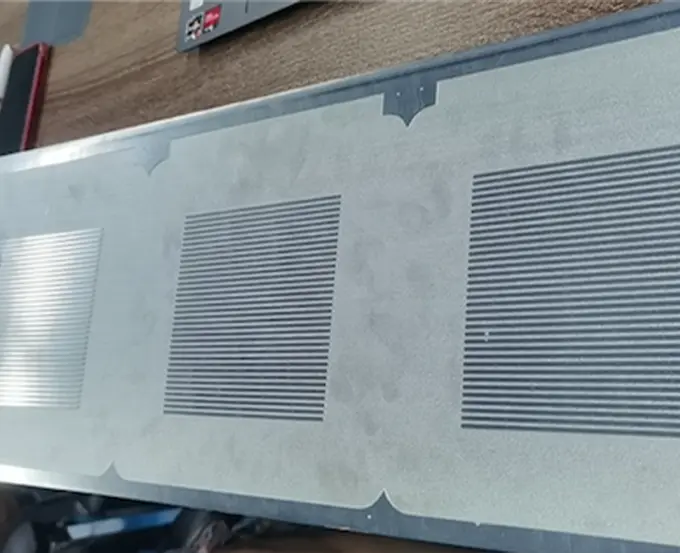
Medical Device Parts
The medical industry obviously needs to achieve the absolute highest standards in precision metal components to ensure the smooth operation of medical devices without obstacles. Metal components in medical applications must also be corrosion-resistant, have mechanical strength, and material biocompatibility. These components usually need to be complex, small parts. Stainless steel etching can guarantee this quality and reliability.
As mentioned with previous products, stainless steel etching ensures the finished product is burr-free and stress-free, thus requiring almost no post-processing. Since the etchant only corrodes unwanted materials, the metal does not become brittle or thermally deformed due to high-energy processes like laser or mechanical stamping, which would alter the metal’s structure.
Learn more about TMN’s Filter Meshes and Screens >>>
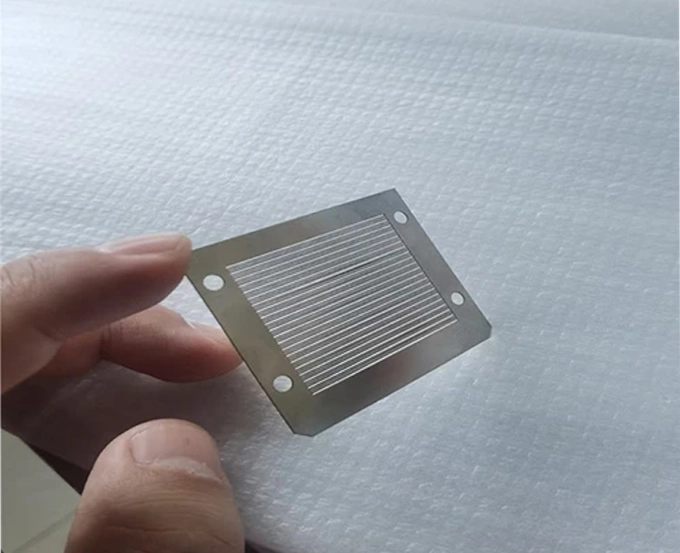
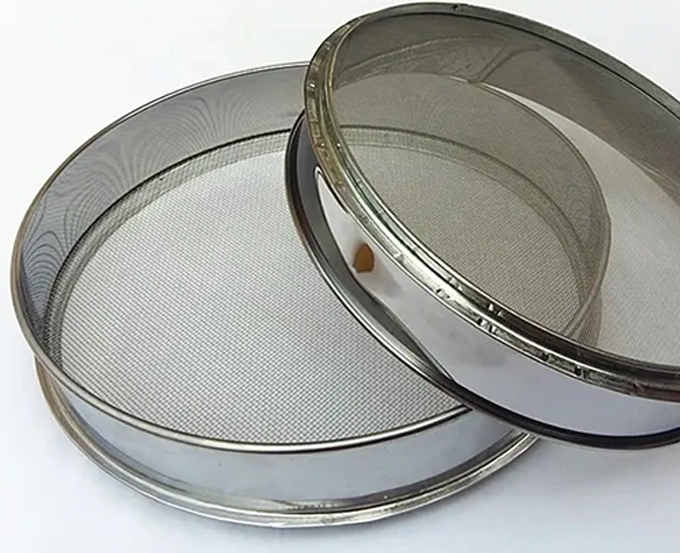
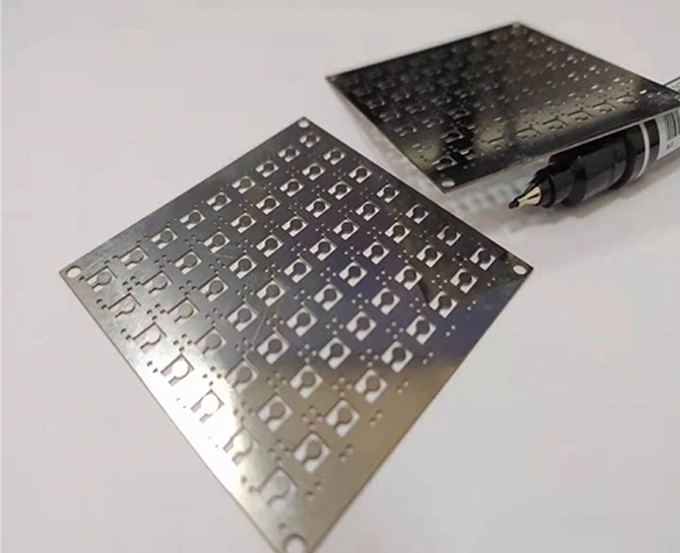
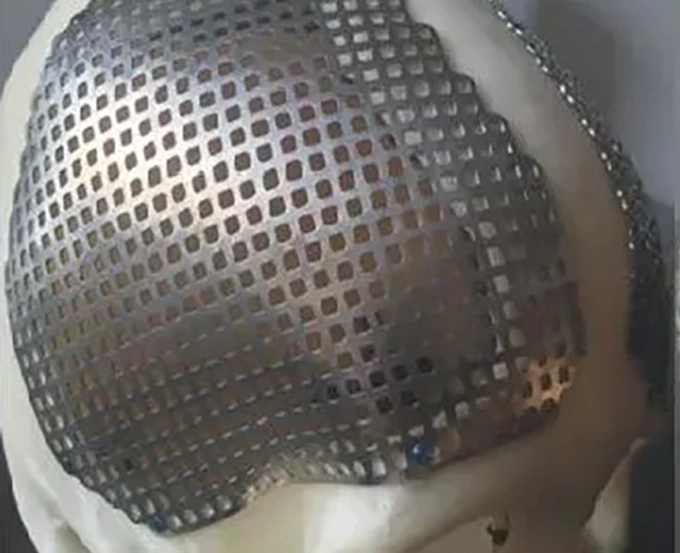
Summary:
The characteristics of stainless steel make it widely used, and the photochemical etching process can provide better products and services for stainless steel component merchants, including:
1. Avoiding material deformation and performance changes: No pressure or heat during processing, preserving the original characteristics of stainless steel.
2. Quick adjustments: Using computer-designed patterns and markings, extremely fine and complex parts can be processed.
3. No mold costs: No need for expensive metal molds, with low design and adjustment costs.
4. High flexibility: Suitable for stainless steel materials of various thicknesses and shapes, especially thin plate materials.
5. Rapid production: Delivery time can be completed in just a few days, rather than weeks or even months.
The versatility of stainless steel etching, combined with TMN’s process technology and experience, makes us stand out among many metal processing manufacturers.
Learn more about TMN’s Stainless Steel Etching >>>