Using laser welding to join hundreds of bipolar plates is an advanced technology that is increasingly being adopted by fuel cell manufacturers.Laser welding uses a high-energy-density laser beam to rapidly melt the contact surfaces of two metal plates and completely fuse them together to form a strong weld. This technology demonstrates exceptional advantages in industries such as aerospace, automotive manufacturing, electronics, and energy. This article will detail why bipolar plates need to be welded, how laser welding enhances bipolar plates, and whether TMN can provide laser welding services for bipolar plates.
Why Use Welding Technology to Weld Bipolar Plates
Welding technology plays a crucial role in the manufacture of bipolar plates. It not only enhances the overall performance of fuel cells but also improves their safety, reliability, and service life. If aspects such as sealing, structural strength, conductivity, thermal management, and manufacturing precision do not meet the required standards during the production of bipolar plate stacks, the overall performance of the fuel cell will be significantly reduced.
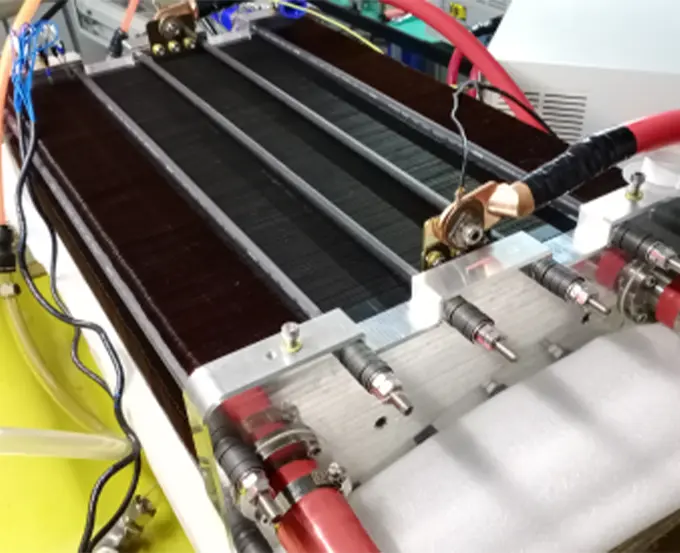
What is Laser Welding?
Laser welding is a high-efficiency precision welding method that uses a high-energy density laser beam as the heat source. In the 1970s, this technology was mainly used for welding thin-walled materials and low-speed welding. The welding process is of the heat conduction type, where the laser radiation heats the workpiece surface, and the surface heat diffuses inward through thermal conduction. By controlling parameters such as laser pulse width, energy, peak power, and repetition frequency, the workpiece melts, forming a specific molten pool. Currently, laser welding has been successfully applied to the precision welding of micro and small parts.
Comparison with Traditional Welding Technology
Compared to traditional welding technology, laser welding performs better in the following aspects:
Welding Precision: The laser beam used in laser welding can be focused into a very small spot, making it highly suitable for fine welding and microstructures. Precise welding control can be achieved by adjusting the laser power and focus position, which is difficult to achieve with traditional welding.
Welding Speed: Laser welding can concentrate high energy in a short time, requiring no prolonged heat input, thus completing the welding process quickly and significantly improving production efficiency.
Heat Affected Zone: Laser welding can precisely control the amount of heat input, resulting in a very small heat-affected zone, reducing material deformation and thermal stress. TMN’s research has found that stable heat input control is a key factor in ensuring welding process stability, effectively solving the issue of ultra-thin metal bipolar plates’ sensitivity to laser-generated heat during welding.
Material Compatibility: Traditional welding technology often performs poorly on certain materials, such as metals with high thermal conductivity or high reflectivity, whereas laser welding excels, particularly for thin sheet materials, preventing penetration and burning.
Welding Quality: The weld quality of traditional welding is heavily influenced by the welding process and operator skill, often requiring subsequent grinding and cleaning. In contrast, laser welding produces high-quality welds with smooth surfaces, eliminating the need for post-processing, reducing contamination and oxidation during the welding process, and resulting in purer weld quality.
Automation and Flexibility: Traditional welding methods have a low degree of automation, requiring significant manual intervention, and lack flexibility for complex and precision welding tasks. Laser welding, integrated with CNC machines and robots, can achieve automated production, suitable for welding complex and precise structures.
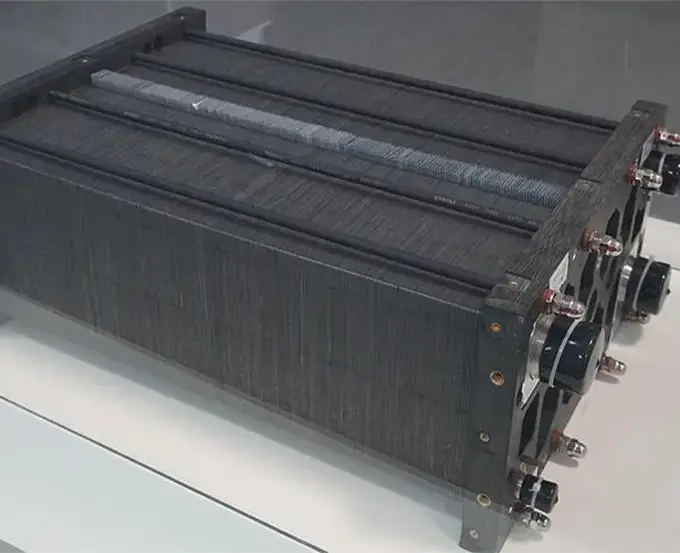
Can TMN Provide Laser Welding Services for Bipolar Plates?
Laser welding technology showcases exceptional advantages in the manufacturing of fuel cell bipolar plates. These include high welding precision, fast welding speed, small heat-affected zone, strong material compatibility, high weld quality, and high levels of automation and flexibility. TMN has successfully utilized this technology to manufacture bipolar plate stacks for multiple clients, becoming increasingly proficient in its application. To date, TMN has successfully welded electrode stacks containing up to 500 bipolar plates and has received positive feedback from customers.
Here are two typical cases that further demonstrate TMN’s excellence in laser welding:
Case 1: Laser welding of 0.15mm bipolar plates, welding 176 layers with no weld scars, false welds, or bubbles, and maintaining a flatness of 0.08mm.
Case 2: Welding bridges on both the cathode and anode plates to achieve flow channel closure, resulting in weld surfaces with no visible scars and a flatness control of 0.08mm.
In addition to outstanding performance in laser welding, TMN also offers other bipolar plate processing services:
Dual-depth Channel Etching: For example, a bipolar plate with a total thickness of 2.0mm can have channels etched to depths of 0.6mm and 0.4mm on one side, and 0.5mm on the other side.
Surface Coating: TMN can plate one side of the bipolar plate with platinum and the other side with MMO.
If you have custom requirements for bipolar plates, please leave us a message or comment, and we will contact you as soon as possible to provide the best solution.
Learn more about TMN metal bipolar plate manufacturing >>>
Related products display
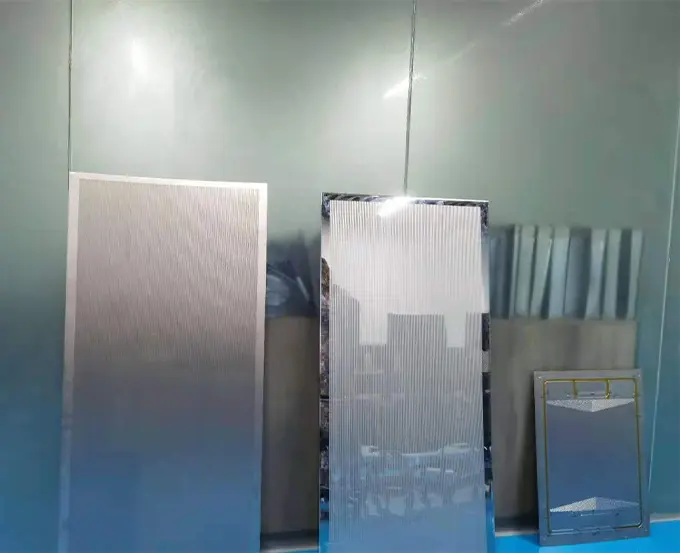
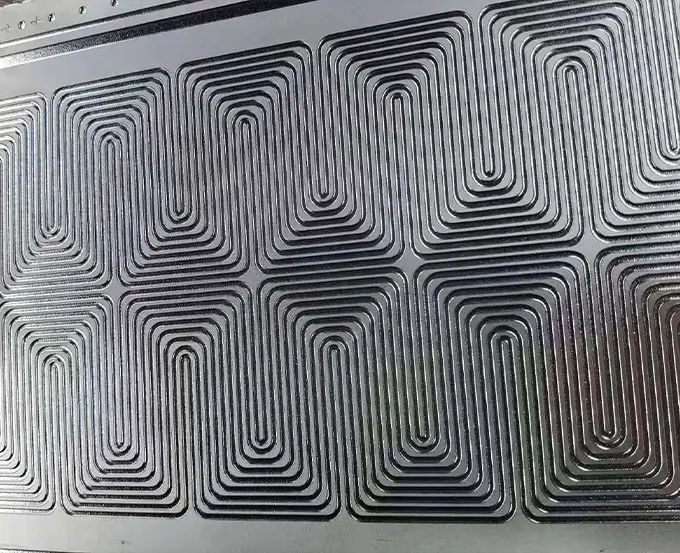
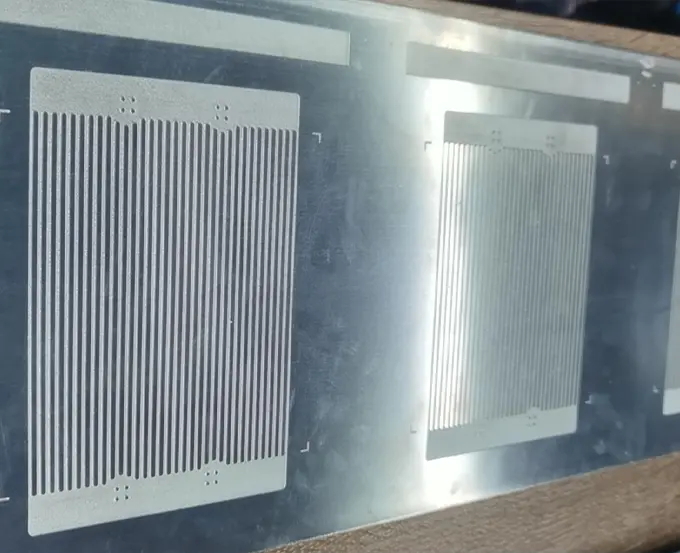
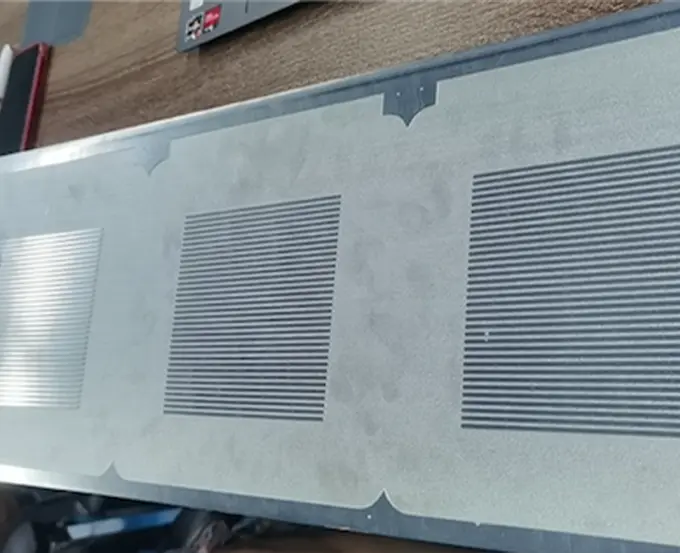