Bipolar plates, often referred to as current collectors, are indispensable components within fuel cell technology. Positioned between membrane electrode assemblies and sealing components, these plates play a multifaceted role that is essential for the efficient operation of fuel cells.
Functionally, bipolar plates serve as critical links within the fuel cell stack, performing a range of tasks that ensure the seamless conversion of chemical energy into electrical power.
First and foremost, they act as barriers, effectively separating the fuel and oxidant streams while preventing gas crossover, thus maintaining the integrity of the electrochemical reactions occurring within the cell. Additionally, these plates facilitate the transportation of reaction gases to and from the electrodes, enabling efficient electrochemical reactions.
Moreover, bipolar plates play a crucial role in providing electrical connectivity, ensuring the smooth flow of current through the cell stack. They also contribute to the removal of water by-products generated during the electrochemical reactions, preventing flooding and maintaining optimal cell performance.
Furthermore, the design and machining of flow channels within bipolar plates are engineered to evenly distribute gases to the electrode’s reaction layer, promoting uniform electrochemical reactions. They also aid in dissipating heat effectively, thus helping to regulate temperature within the fuel cell stack.
In terms of construction, bipolar plates exhibit characteristics ideal for their application. They are characterized by thin profiles and lightweight construction, contributing to the overall efficiency of the fuel cell system. Furthermore, they offer cost-effective manufacturing options, making them suitable for large-scale production.
Material selection for bipolar plates is paramount, with materials needing to exhibit high strength, corrosion resistance, good gas tightness, and high conductivity to optimize both power output and longevity of fuel cell systems. Currently, bipolar plates in the market are generally classified into three categories: graphite bipolar plates, metal bipolar plates, and composite bipolar plates.
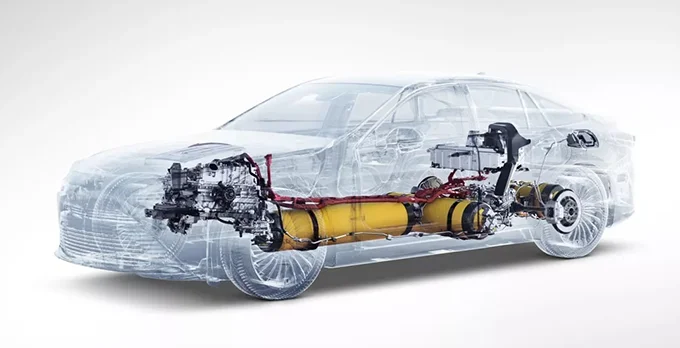
Graphite bipolar plate
Graphite bipolar plates are essential components in fuel cell technology, primarily composed of graphite powder and expanded graphite.
1. Graphite Powder:
Graphite powder serves as one of the primary raw materials for graphite bipolar plates. It is finely ground graphite, characterized by its high conductivity and corrosion resistance properties.
2. Expanded Graphite:
Expanded graphite, another crucial component, undergoes a process of expansion to increase its volume. This results in a porous structure with enhanced thermal and electrical conductivity, making it an ideal material for bipolar plates.
The production and processing of graphite bipolar plates typically involve two main methods:
– The first method involves the molding or injection molding of graphite powder mixed with resin materials. This process utilizes the characteristics of the graphite powder-resin mixture to achieve hydrophobic properties on the product surface.
– The second method utilizes expanded graphite composite materials to produce plate-like structures. This process involves steps such as light pressing, molding, resin impregnation, sulfurization, bonding, and sealing. By utilizing expanded graphite materials, the resulting products exhibit high conductivity and thermal conductivity, meeting the requirements for bipolar plate geometry, surface contour, and mechanical dimensions.
Graphite bipolar plates offer several advantages, including high durability, corrosion resistance, and relatively low cost. They are particularly suitable for commercial vehicles such as buses, logistics vehicles, sanitation vehicles, and forklifts. However, graphite bipolar plates also have some drawbacks, such as low compressive and flexural strength, which may lead to fragility, assembly challenges, and larger dimensions.
Note: Learn more about the materials and manufacturing process of graphite bipolar plates
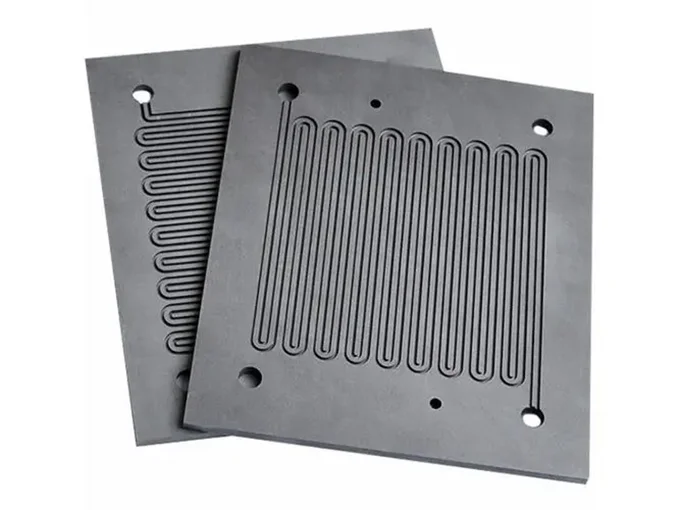
Metal bipolar plates
Metal bipolar plates are essential components in fuel cell technology, gradually emerging as the mainstream choice due to their cost-effectiveness and superior mechanical properties. These plates are crafted from a variety of metals and metal-based composite materials, each offering unique advantages in fuel cell applications.
A Detailed Understanding of the Working Principle, Manufacturing Process, and Metal Materials of Metal Bipolar Plates >>>
Materials such as stainless steel, aluminum alloys, titanium alloys, nickel alloys, copper alloys, and metal-based composites find extensive use in the manufacturing of metal bipolar plates. Traditional stamping or photo etching processes are employed to produce ultra-thin metal sheets as thin as 0.1mm for bipolar plate fabrication.
Metal plates, being relatively thinner, exhibit higher volume power density, making them well-suited for high-power-density fuel cell stacks. They are widely utilized in passenger vehicles and other applications requiring high power output. However, metal plates may suffer from reduced durability, higher production costs influenced by material selection, and susceptibility to oxidation reactions and corrosion in acidic environments or high-temperature conditions.
It’s worth noting that achieving large-scale production of metal bipolar plates could significantly reduce production costs, making it a focal point of research in the industry. As advancements continue, metal bipolar plates hold promise for further optimizing fuel cell technology, contributing to the advancement of clean energy solutions.
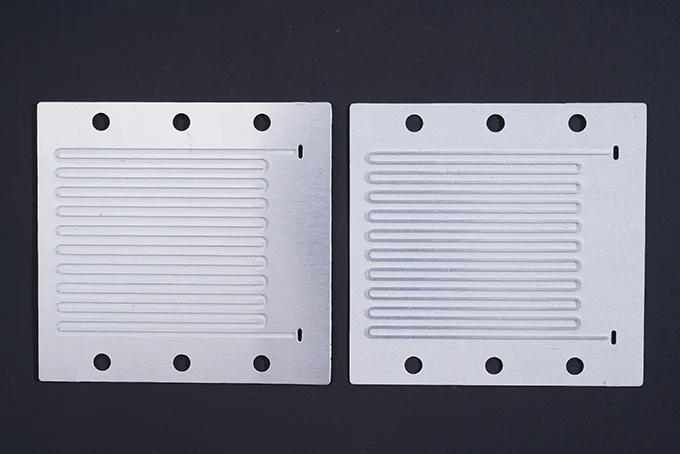
Composite bipolar plates
Composite bipolar plates represent a pioneering advancement in fuel cell technology, composed of two or more materials synthesized to create innovative solutions. Let’s delve into what makes composite bipolar plates stand out.
Composite bipolar plates feature a blend of materials, notably carbon/carbon composites and graphite/polymer composites. These combinations aim to leverage the corrosion resistance of graphite materials with the processability and high hardness characteristics of metals, addressing the limitations inherent in individual materials.
Current research focuses on surface modifications of anode plates made of aluminum alloys, carbon steel, or stainless steels like 316L and 310L. Surface modification techniques include carbon-based coating, metal nitride coating, and polymer coating, enhancing their performance and durability.
Despite their potential benefits, composite bipolar plates face certain challenges. Their extended processing cycles and complex production processes, coupled with reliability issues over prolonged usage, limit their widespread adoption in fuel cell applications.
Moreover, surface coating technologies demand stringent equipment requirements, particularly for processes involving precious metal electroplating, which significantly adds to production costs.
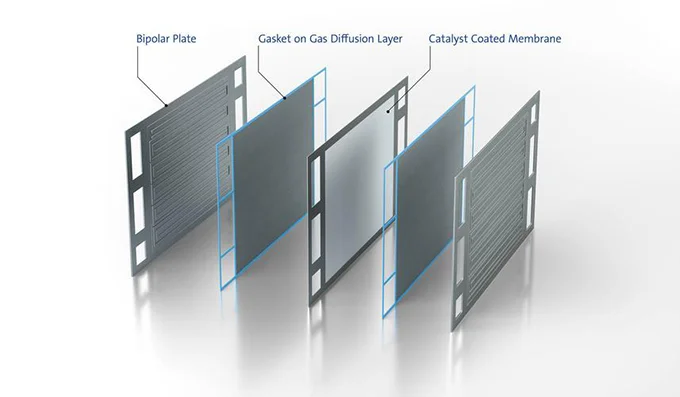
Bipolar plates are vital components of fuel cells, and the search for high-performance and cost-effective new materials and fabrication methods for bipolar plates is crucial for the industrialization of fuel cell vehicles. Among various bipolar plate materials, metal bipolar plates have advantages in conductivity, fatigue resistance, etc., compared to graphite bipolar plates, making them more conducive to miniaturization and significantly significant for increasing the power density of fuel cell stacks.
In the future, the development of excellent corrosion-resistant and conductive coatings or new types of metal materials for bipolar plates will greatly promote the application of PEMFCs in the passenger vehicle field. Moreover, technological advancements driving cost reduction are equally critical, and accelerating the transformation of bipolar plate products from laboratory achievements to industrial products is the most direct path to cost reduction and efficiency enhancement.