Copper Etching
What Is Copper Etching?
Copper etching, a chemical process involving the selective removal of copper material to create intricate patterns and designs, plays a crucial role in electronics, automotive, aerospace, and beyond. Particularly in the electronics sector, copper etching enables the precise fabrication of printed circuit boards (PCBs), enhancing signal routing and device functionality.
Market leaders like TMN demonstrate expertise in precision copper etching, catering to diverse industry demands with efficiency and versatility. With ongoing advancements driving innovation, copper etching remains a cornerstone in modern manufacturing, poised to continue shaping technological advancements and industry growth.
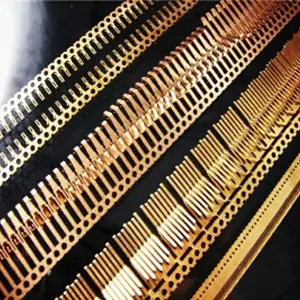
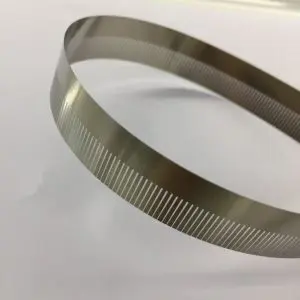
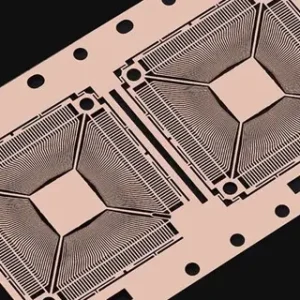
The process steps of chemical etching of copper
TMN etches copper chemically in several steps. Here's a general overview of the process:
Surface Preparation
Clean the copper substrate thoroughly to remove any contaminants or oxides.
Application of Resist
Apply a resist material onto the copper surface to protect areas that should not be etched.
Exposure and Development
If using a photoresist, expose the resist-coated copper to UV light through a photoetched, then develop the resist to reveal the desired pattern.
Etching
Immerse the prepared copper substrate into an etchant solution that selectively removes exposed copper areas while leaving resist-protected areas intact.
Rinsing and Cleaning
Rinse the substrate to remove etchant and residual resist material.
Stripping of Resist
Remove the resist material to reveal the etched copper features.
Optional Post-Etching Treatment
Additional treatments such as passivation, polishing, or plating may be performed as needed.
Quality Control
Inspect the etched copper parts for dimensional accuracy and surface finish.
Following these steps allows for the precise etching of copper to create desired patterns and features while ensuring quality and reliability.
Benefits of Etching Copper
Smooth Profiles
Bid farewell to jagged edges and uneven surfaces. Our process guarantees a smooth edge and surface etch profile, eliminating surface burrs and ensuring consistency in every batch.
Tight Tolerances
Precision is our forte. Achieve tolerances as tight as ±10% of material thickness, allowing for meticulous detailing and intricate designs without compromise.
Versatile Geometries
Embrace complexity without hesitation. Our method accommodates complex geometries at no additional cost, offering the freedom to explore intricate patterns and configurations.
Exceptional Capability
Break barriers with our comprehensive range of capabilities. From 1:1 aperture aspect ratios to thicknesses spanning from 0.07mm to 2.5mm, we cater to diverse needs with ease.
Expansive Size Range
Think big, produce bigger. With part sizes up to 1500mm x 600mm, our process empowers you to scale your operations without limitations.
Swift Turnaround
Time is of the essence. Benefit from our fast turnaround times, ensuring prompt delivery without compromising on quality or precision.
Scalable Production
From prototypes to serial production, our process seamlessly transitions across volumes, offering scalability without sacrificing efficiency.
No Heat-Affected Zones
Preserve material integrity. Our process eliminates heat-affected zones, safeguarding the structural integrity and properties of your copper components.
Partner with us and unlock the full potential of chemically etched copper. Experience the precision, reliability, and cost-effectiveness that redefine industry standards.
main application of copper etching
The versatility and precision of copper etching make it indispensable across a wide range of industries, contributing to the production of diverse products and technologies.
Some examples will be given below:
Printed Circuit Boards (PCBs)
Copper etching is used to create conductive pathways on PCBs for the transfer of electrical signals between components.
Electronics
Copper etching produces intricate patterns for various electronic components including antennas, connectors, sensors, and integrated circuits (ICs).
Microelectronics
Etching is vital for producing MEMS, microfluidic devices, and miniaturized electronic components with high precision and fine detail.
Decorative Items
Etching allows artisans to create intricate designs on copper surfaces for jewelry, art pieces, and architectural ornaments.
Metallic Stencils
Copper etching fabricates metallic stencils used in screen printing, spray painting, and etching onto other materials.
Heat Exchangers
Etched copper plates enable efficient heat transfer in HVAC systems, refrigeration units, and industrial processes.
Flexible Circuits
Etching creates flexible conductive traces on polymer substrates for applications like wearable electronics and medical devices.
Photovoltaic Cells
Copper etching is used to create grid lines and contacts in photovoltaic cells for efficient capture and conduction of solar energy.
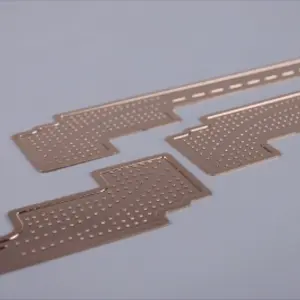
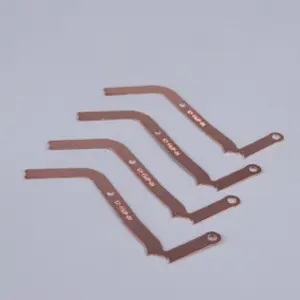
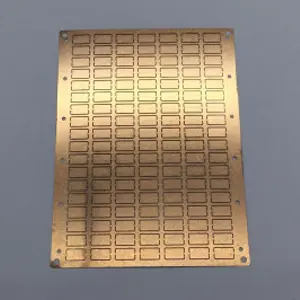
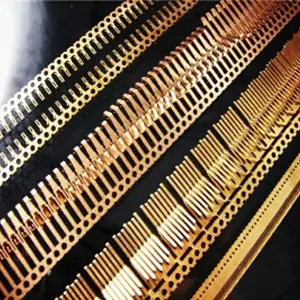
Common copper numbers suitable for chemical etching
Alloy | Composition | Properties | Suitability for Chemical Etching |
---|---|---|---|
C11000 | 99.9% Cu | High electrical and thermal conductivity, malleability | Excellent |
C26000 (Cartridge Brass) | 70% Cu, 30% Zn | Good machinability, corrosion resistance | Excellent |
C28000 (Muntz Metal) | 60% Cu, 40% Zn | Good corrosion resistance (especially in marine env.) | Excellent |
C35300 (High Leaded Brass) | Cu, Zn, Pb | Improved machinability | Good with proper conditions |
C36000 (Free-Cutting Brass) | 60% Cu, 40% Zn | Excellent machinability | Good with proper conditions |
C46400 (Naval Brass) | 60% Cu, 39.2% Zn, 0.8% Sn | Good corrosion resistance (especially in seawater) | Excellent |
C51000 (Phosphor Bronze) | Cu, Sn, P | Good corrosion resistance, high strength | Excellent |
C54400 (Phosphor Bronze) | Cu, Sn, P | Excellent corrosion resistance, high strength | Excellent |
C70600 (Cu-Ni 90/10) | 90% Cu, 10% Ni | Excellent corrosion resistance (especially in seawater) | Good |
C71500 (Cu-Ni 70/30) | 70% Cu, 30% Ni | Good corrosion resistance, high strength | Good |
C75200 (Cu-Ni-Silver) | Cu, Ni, Ag | Good corrosion resistance, electrical conductivity | Good |
how to protect the surface of copper etching parts to be oxidized ?
Are you concerned about the surface of metal parts oxidizing after copper chemical etching? Don't worry! With proper treatment, the metal parts' surface can be protected. There are several methods available to prevent oxidation of the metal surface.
Polishing the Surface
Polishing the copper surface can help remove any oxidation and provide a smooth, shiny finish. This can be achieved through mechanical polishing techniques or chemical polishing processes.
Plating
Electroplating or electroless plating with metals such as nickel, tin, silver, or gold can provide a protective layer on the copper surface, preventing oxidation and enhancing the appearance and durability of the part.
Coating with Paint or Oil
Applying a coat of paint or oil to the copper surface can provide a protective barrier against oxidation. This method also offers the added benefit of adding color and aesthetics to the part.
Surface Passivation
Passivation is a chemical process that involves treating the copper surface to create a protective oxide layer, which helps prevent further oxidation and corrosion. This method is commonly used in industrial applications to protect metal surfaces.
Applying Organic Film
Coating the copper surface with an organic film that is easy to remove can provide temporary protection against oxidation during storage or transportation. This film can be easily peeled off before further processing or use of the parts.
Each of these methods has its advantages and suitability depending on the specific requirements of the application, including durability, appearance, and cost. It's essential to consider factors such as the intended use of the parts, environmental conditions, and desired aesthetics when choosing the most appropriate surface protection method for copper etched parts.
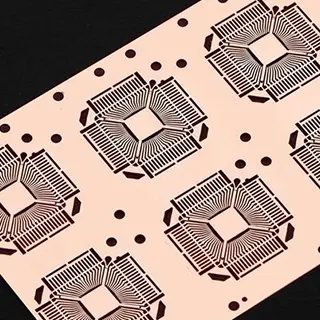
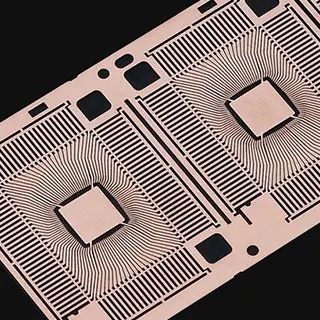
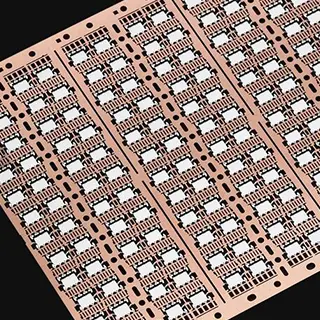
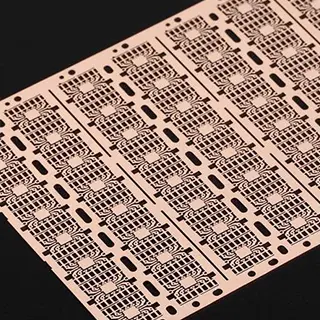
Send us a message