When precision applications require materials that are both strong and lightweight, aluminum and its alloys are often the metals of choice. Aluminum not only boasts an excellent strength-to-weight ratio but is also naturally corrosion-resistant, making it ideal for use in extreme environments. While aluminum’s good ductility and high electrical conductivity are advantageous, they can pose challenges in certain manufacturing processes.
Aluminum’s ductility can lead to tool wear and material tearing in some machining processes, and it can harden during stamping. Its high reflectivity makes laser cutting difficult. During chemical etching, aluminum can react exothermically with corrosive chemicals, potentially affecting process efficiency and accuracy, and leading to reduced product quality or equipment damage. Over the past decade, TMN has continuously conducted technical analysis and research, and the precision aluminum etched components we now offer are comparable to stainless steel etched components in terms of precision, adhering to industry standards.
What is Etching Aluminum?
Etching Aluminum, also known as chemical etching, is a process that uses an etching solution to selectively and precisely dissolve metal to create the desired components. It is commonly used to create precise patterns or features on aluminum or to remove excess parts.
Etching Aluminum can replace traditional sheet metal processing techniques, including stamping, laser cutting, and waterjet cutting, providing a cost-effective, high-precision, and rapid manufacturing alternative. The specific reasons are as follows:
Cost-effectiveness: Traditional stamping processes require expensive mold making, while the etching process only requires creating a photomask, eliminating mold costs. Furthermore, the etching process efficiently utilizes materials when processing aluminum, reducing waste.
High precision: The etching process can achieve micron-level precision and intricate details, which are difficult to achieve with stamping and cutting processes. It is particularly suitable for manufacturing complex shapes and small aperture parts.
Speed: Etching is a chemical process that does not require complex mechanical setup and tuning, allowing for a quick transition from design to production, making it suitable for rapid prototyping and mass production.
In addition to these three points, Etching Aluminum also has significant advantages in stress-free processing, design flexibility, and environmental friendliness, making it an effective alternative to traditional sheet metal processing techniques.
Precision Components Manufactured by Etching Aluminum
With years of experience in Etching Aluminum manufacturing, and continuous technical analysis and development, TMN has provided precision components that exceed industry standards to clients in many countries and industries, earning high praise from customers. Here are some of the precision components we most commonly process:
PCB-Level EMI & RFI Shielding
In electronic devices, PCB-level EMI & RFI Shielding is crucial. Aluminum, as a commonly used material, is widely applied in the EMI & RFI shielding of PCBs (Printed Circuit Boards) primarily because of the following key characteristics:
1. Electromagnetic Shielding Effectiveness (SE): This is an important indicator for measuring the ability of shielding materials to block electromagnetic and radio frequency interference. Aluminum, with its excellent conductivity, can effectively block electromagnetic waves and reduce interference.
2. Lightweight Property: Aluminum’s lightweight nature is a significant consideration, especially in applications where reducing the overall weight of the equipment is essential. Aluminum’s low density is particularly advantageous.
3. High Thermal Conductivity: Aluminum’s high thermal conductivity aids in heat dissipation, effectively preventing electronic components from overheating, thereby extending the lifespan of the equipment.
4. Excellent Corrosion Resistance: Aluminum maintains stable performance under various environmental conditions, which is especially important for electronic devices used over a long period.
Due to these required characteristics, TMN highly recommends our Etching Aluminum process. Firstly, the etching process is a precise manufacturing technology that can achieve high-precision patterns and structural processing, meeting design requirements for different thicknesses and shapes. Secondly, compared to traditional sheet metal processing techniques, Photochemical Etching applies less stress to aluminum materials, preventing deformation and ensuring that PCB-level EMI & RFI Shielding retains its shape and performance during processing and use.
Note: Learn more about TMN’s EMI & RFI Shielding process
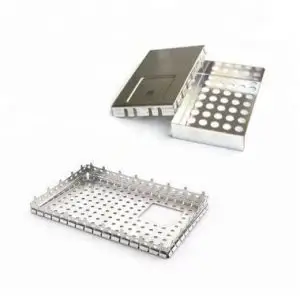
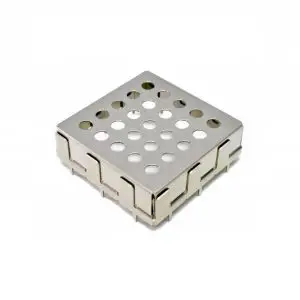
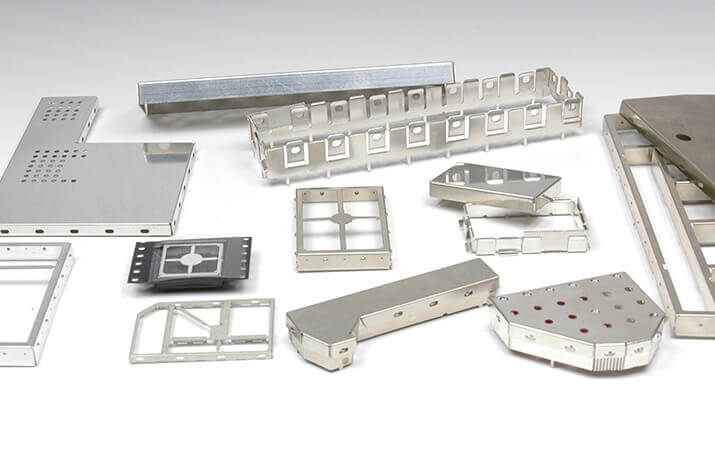
Encoder
Encoders are widely used in industrial automation, robotics, and precision instruments. To ensure their performance and reliability, the manufacturing of encoders must meet several key requirements:
1. Accuracy and Resolution: The primary function of an encoder is to accurately measure rotational angles or positions, demanding high levels of precision and resolution.
2. Lightweight and Strength: Encoders are often used in high-speed rotating mechanical systems. A lightweight design helps reduce rotational inertia, improving system response speed and efficiency.
3. Corrosion Resistance and Durability: Encoders operate under various environmental conditions, making the corrosion resistance and durability of materials crucial.
4. Thermal Conductivity and Heat Dissipation: In high-performance applications, encoders need to handle significant heat. The high thermal conductivity of aluminum aids in rapid heat dissipation, preventing overheating and thus protecting the encoder’s performance and longevity.
TMN’s Etching Aluminum process can produce highly detailed and precise encoders, ensuring high resolution and accuracy. Moreover, the surface treatment process induces no stress, reducing surface defects and micro-cracks, thereby preserving the inherent properties of aluminum to the maximum extent.
Note: Learn more about TMN’s Encoder Disk process
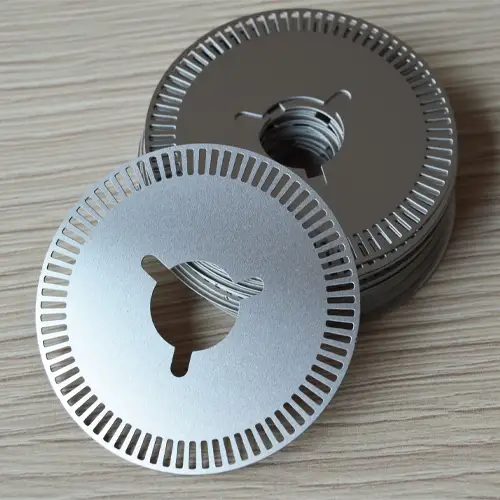
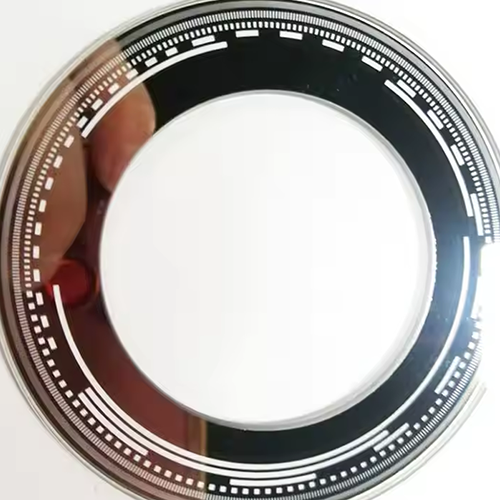
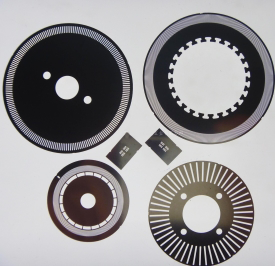
Filter Mesh
In addition to stainless steel, aluminum Filter Meshes also hold a significant position in many applications, including air filters, water filters, and industrial liquid filters. To ensure the performance and efficiency of Filter Meshes, their manufacturing must meet several key requirements:
1. Precise Aperture and Uniformity: The aperture size and uniformity of the Filter Mesh directly affect its filtering effectiveness.
2. High Strength and Durability: Filter Meshes must maintain structural integrity and be resistant to damage during use.
3. Corrosion Resistance: Many filtering applications involve corrosive environments, such as chemical filtration or seawater filtration.
4. Lightweight: In certain applications, such as portable filtering equipment or aerospace fields, the weight of the Filter Mesh is a crucial consideration.
Aluminum Filter Meshes are characterized by high strength and durability, corrosion resistance, and lightweight properties. TMN’s high-precision Etching process ensures precise aperture size and uniformity, and the stress-free processing effectively meets these key requirements, providing a reliable solution for manufacturing high-quality Filter Meshes.
Note: Learn more about TMN’s Metal Filter Mesh process
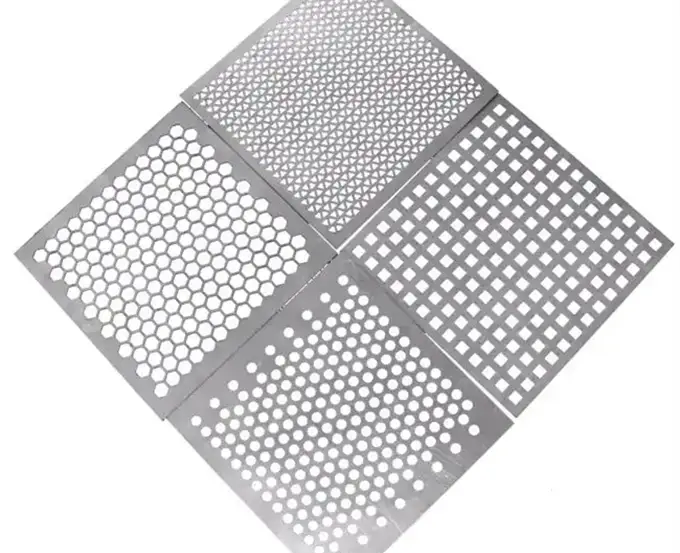
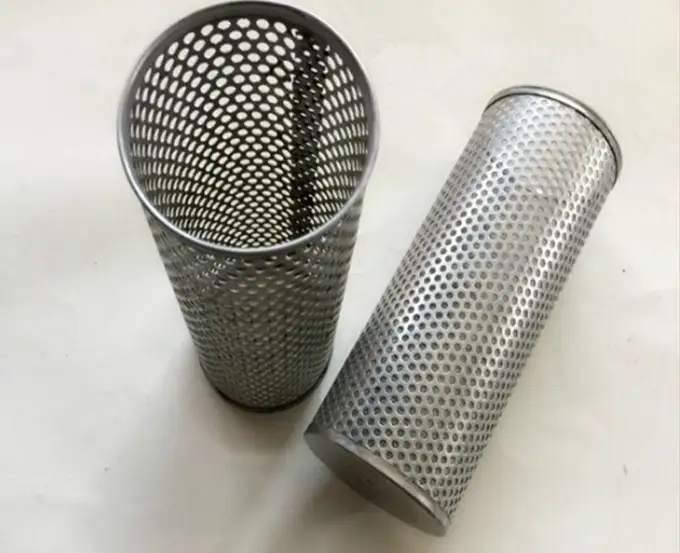
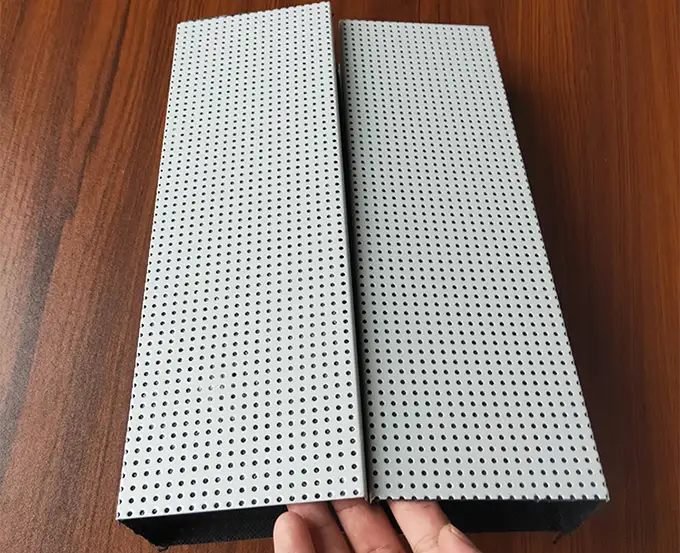
Bipolar Plates
Stainless steel is the most commonly used material for metallic Bipolar Plates. However, with ongoing research and experimentation, aluminum Bipolar Plates have begun to be used in fuel cells and electrolyzers as conductive and structural components. Currently, the application of aluminum Bipolar Plates is still in the research and testing phase.
Although aluminum has many excellent properties, its stability in corrosive environments needs to be addressed. Current research mainly focuses on surface treatment and coating technologies to enhance the corrosion resistance and durability of aluminum Bipolar Plates. With advancements in technology, the application prospects of aluminum Bipolar Plates will become broader.
TMN’s Etching Aluminum technology can achieve high-precision patterning and structural processing. For aluminum Bipolar Plates, this means the ability to manufacture complex and intricate flow channels and conductive paths, optimizing the performance of fuel cells. Furthermore, after producing qualified Bipolar Plates, secondary processing technologies such as surface treatment and coating can be provided. This includes options like platinum plating on one side and MMO coating on the other, offering robust support for the research and testing of aluminum Bipolar Plates.
Note: Learn more about TMN’s Bipolar Plates process
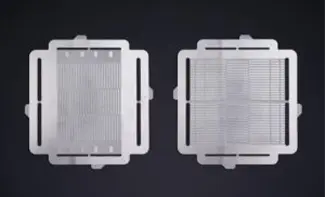
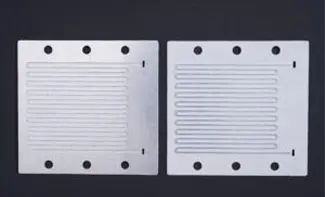
About TMN
TMN is a photochemical etching manufacturer with over ten years of experience. Through continuous technological innovation and development, we have successfully provided high-quality aluminum etched precision components for various industries across multiple countries. Whether it is EMI & RFI Shielding for electronic devices, Encoder Disks in industrial automation, or Filter Mesh and Bipolar Plates for diverse applications, our Etching Aluminum process meets the high standards of our customers, providing reliable and efficient solutions. TMN will continue to focus on technological advancements and innovation, creating greater value for our customers and driving industry development.
If you need customized high-precision, complex, stress-free aluminum components, TMN’s Etching Aluminum process is undoubtedly your best choice. Whether you have questions about the etching process or about TMN, we welcome you to easily contact us via phone, WeChat, or WhatsApp at +8613603056883, or by sending an email to lydia.sales1@tmnetch.com
Note: Learn more about TMN>>>
Related articles:
How To Choose Between Metal Etching and Metal Engraving?
Copper Etching: Reasons for using photo etching for copper metal
Stainless Steel Etching Process: How to Choose Stainless Steel Etching