Metal bipolar plates manufactured using photochemical etching processes, followed by diffusion welding, offer several advantages.
Firstly, the photochemical etching process can create highly complex bipolar plate channels on the metal surface while ensuring a high degree of precision. Additionally, photochemical etching has minimal impact on the metal material, avoiding the stress and deformation that might occur with mechanical processing.
Diffusion welding technology, when used to weld metal bipolar plates, controls high temperature and pressure to facilitate the diffusion of metal atoms. This forms a strong metallurgical bond at the contact surface without the need for any filler materials, ensuring high strength and airtightness of the welded joint.
The combination of these two processes not only enhances the manufacturing precision and consistency of metal bipolar plates but also improves their mechanical performance and durability. This is one of the manufacturing techniques commonly used by TMN customers.

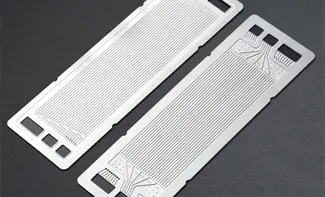
What is Photochemical Etching?
Photochemical etching is a metal processing technique that combines photolithography and chemical etching to precisely remove metal material, forming complex and intricate patterns or structures. TMN offers the best solutions for custom metal bipolar plates using this process. The following outlines TMN’s service process for custom metal bipolar plates:
Step 1: CAD Design Drawing
Receive the designer’s CAD drawings, analyze and confirm details.
Step 2: Metal Selection and Preparation
Choose the appropriate metal based on project requirements and clean the metal surface.
Step 3: Photoresist Coating
Apply photoresist material evenly on the metal surface to form a protective layer.
Step 4: UV Exposure
Expose the coated metal plate to UV light using a phototool, transferring the CAD design pattern onto the metal surface.
Step 5: Development
Place the exposed metal plate in a developer solution to remove the photoresist in the unexposed or exposed areas, leaving only the protected photoresist, forming the desired pattern.
Step 6: Etching
Place the developed metal plate into an etching machine where the etching solution dissolves the metal parts not protected by the photoresist, forming the required pattern.
Step 7: Photoresist Stripping
After etching, remove the remaining photoresist from the metal plate to reveal the final metal pattern.
Step 8: Cleaning and Inspection
Finally, clean the metal plate to remove any chemical residues from the etching process, and conduct a final quality inspection to ensure the etched components meet design requirements.
Note: Learn more about TMN bipolar plate customization process
Why Choose Photochemical Etching for Custom Bipolar Plates
Besides photochemical etching, many businesses are most familiar with the traditional die-casting process. The biggest drawback of die-casting is the expensive mold cost and the difficulty in modifying design drawings. Additionally, with increased processing quantities, accuracy may be compromised.
The principle of photochemical etching primarily involves using photoresist to protect the parts of the metal that do not need to be etched, then removing the excess metal parts with a suitable chemical etching solution. If design modifications are needed, adjustments can be made directly in the drawing software without any mold costs. TMN also has five fully automatic production lines, each 39 meters long, enabling rapid mass production with all product precision tolerances controlled within +/-0.05mm.
What is Diffusion Welding
Diffusion welding is a welding process that involves tightly contacting the metal surfaces to be welded under high temperature and pressure, causing the metal atoms to diffuse at the contact interface and form a strong metallurgical bond. This process does not require filler materials and does not produce noticeable melting or liquid phases, thereby maintaining the high strength and airtightness of the welded joint. Diffusion welding is particularly suitable for welding metal components with high precision and performance requirements, such as in fuel cells, aerospace, and electronic devices.
After the production of metal bipolar plates is completed, custom clients need to have them welded using diffusion welding. TMN also offers this welding process. The following outlines TMN’s service process for welding metal bipolar plates using diffusion welding:
Step 1: Confirm Welding Quantity
Confirm the number of metal bipolar plates to be welded with the custom client to appropriately arrange the processing steps and time.
Step 2: Surface Cleaning
Clean the surfaces of the metal bipolar plates to be welded, removing oxides, grease, and other impurities to ensure welding quality.
Step 3: Assembly and Positioning
Assemble the metal bipolar plates to be welded according to requirements, ensuring accurate alignment of all parts and securing them with fixtures.
Step 4: Pressurizing and Heating
Apply appropriate pressure based on the material characteristics and welding process requirements, then slowly heat to the predetermined temperature in a vacuum or inert gas environment.
Step 5: Waiting
Wait for the predetermined time to allow sufficient diffusion of metal atoms, forming a strong metallurgical bond.
Step 6: Cooling and Depressurizing
While maintaining pressure, gradually lower the temperature. Once cooled to a certain temperature, gradually release the pressure to complete the welding process.
Step 7: Quality Inspection
Conduct final inspections, such as appearance inspection, non-destructive testing, and airtightness testing, to ensure compliance with standards.
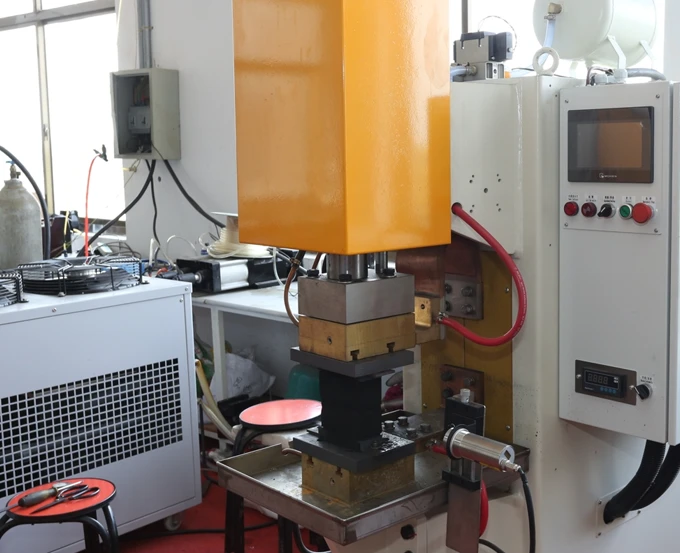
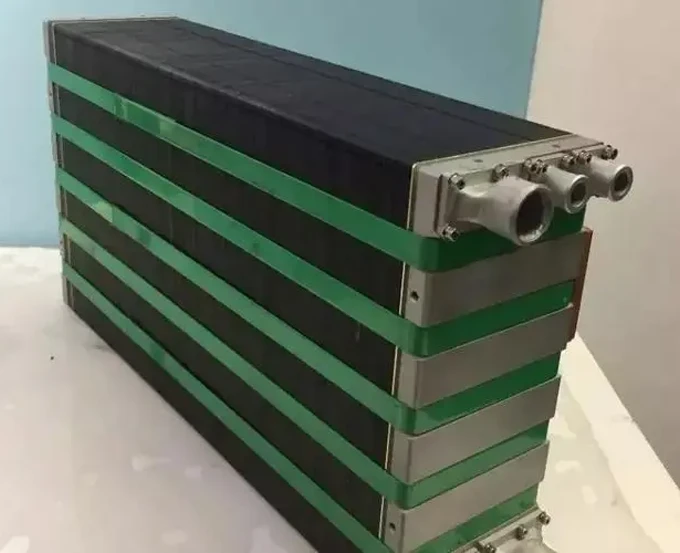
About TMN’s Metal Bipolar Plate Manufacturing
TMN has over ten years of experience in metal plate processing and international trade. Our high-precision custom metal components produced through photochemical etching have been exported to numerous countries, including the UK, USA, Germany, Switzerland, Hungary, and Estonia. We serve clients dedicated to the research and production of fuel cell stacks and water electrolyzers. Additionally, we prepare relevant documents and Certificates of Conformance (COC) for delivery to assist with customs clearance and import inspection.
Custom Bipolar Plate Services Include:
Customizable Channel Patterns: Both sides of the metal plate can have the same or different bipolar plate channels.
Customizable Channel Depths: Both sides of the metal plate can have the same or different channel depths. It is also possible to customize two different channel depths on the same side. For example, if the total thickness of the bipolar plate is 2.0mm, one side can be etched with channels 0.6mm and 0.4mm deep, and the other side can have channels 0.5mm deep.
Flexible Design Modifications: All channel designs can be flexibly modified during customization to support your project.
Surface Coating Options: Bipolar plates can support platinum and MMO coatings, as well as other complex surface treatments. It is even possible to plate one side with platinum and the other with MMO.
Prototype Samples Available: We can provide 1-2 prototype samples to verify the acceptability of your new design.
This is an introduction to TMN’s photochemical etching and diffusion welding processes for custom metal bipolar plates. If you have any questions or custom requirements, feel free to contact us via phone, WeChat, or WhatsApp at +8613603056883, or send an email to lydia.sales1@tmnetch.comÂ
Note: Learn more about TMN>>>