What is Photochemical Etching?
I believe TMN, as a factory with over ten years of experience specializing in providing photochemical etching services, is most familiar with this process. Photochemical etching is a high-precision manufacturing process used to etch complex patterns or fine structures on the surface of thin metal sheets. This process is widely applied in various fields, including household appliances, automotive, medical devices, electronics, aerospace, and industrial automation. It offers the advantages of high precision and high resolution.
Advantages of Photochemical Etching
High Precision: Photochemical etching can achieve micron-level processing precision, which is crucial for fields requiring high accuracy, such as electronic components, semiconductors, and medical devices.
TMN’s etching technology precision can reach +/-0.03mm.
Complex Pattern Processing: Photochemical etching can create complex, intricate patterns on metal surfaces. With advanced fully automated etching machines, the processing can be precisely controlled. This makes it suitable for manufacturing parts with complex geometries, such as filter meshes, bipolar plates, and 3D model assembly components.
TMN has five 39-meter fully automated etching production lines, enabling efficient and precise processing.
Wide Material Applicability: Photochemical etching is suitable for various metal materials, including stainless steel, copper, brass, aluminum, titanium, and nickel.
TMN has its own large warehouse, storing various raw materials with thicknesses ranging from 0.01mm to 2.0mm, ready for rapid production.
High Repeatability and Consistency: The photochemical etching process is highly repeatable, ensuring that parts produced in the same batch maintain a high degree of consistency, meeting strict quality control requirements.
TMN uses fully automated etching machines during the etching process, ensuring that each precision part remains consistent.
Flexibility: Photochemical etching allows for quick conversion from design drawings to final products. Design drawings can be adjusted during the process, reducing development time and costs, making it ideal for product development and modification.
TMN can quickly provide 1-2 prototype samples to verify the feasibility of new design solutions, without any mold costs.
Low Cost: Compared to some high-precision processing techniques (such as laser cutting or EDM) and mold-requiring processing techniques, photochemical etching has the advantages of no mold requirements and lower operating costs, making it particularly suitable for mass production.
Stress-Free Processing: Unlike mechanical processing, etching technology does not apply mechanical stress, preventing material deformation, stress concentration, or cracks, helping maintain the dimensional accuracy and material properties of parts.
No Heat-Affected Zone: Since the processing does not involve high-temperature treatment, the metal material surface will not produce a heat-affected zone, avoiding changes in material properties due to heat treatment.
These advantages enable TMN to serve clients across various fields, including electronics, medical, automotive, fuel cells, and household appliances, especially those needing high-precision and structurally complex precision parts.
Note: Learn more about TMN’s photochemical etching services
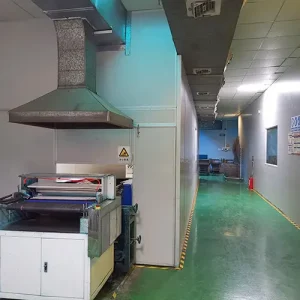
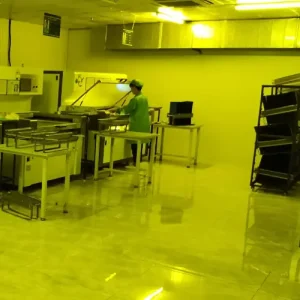
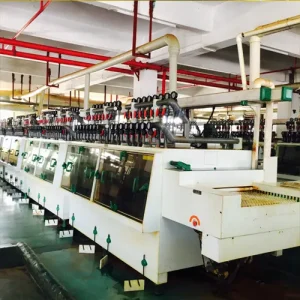
What Types of Products are Suitable for Photochemical Etching?
Due to the high precision and low cost advantages of photochemical etching, TMN has served clients across various industries since its establishment. Below, I will provide detailed examples:
Metal Filter Mesh
The metal filter meshes produced by TMN are widely used in household appliances, medical devices, aerospace, and other fields. Different fields have varying requirements for the precision and performance of filter meshes.
Ordinary Metal Filter Mesh is typically used in household appliances. The manufacturing process is relatively simple, focusing mainly on the corrosion resistance and mechanical strength of the materials. The mesh size and shape are relatively less stringent, making them suitable for equipment such as range hoods, air conditioners, water purifiers, and hair dryers.
In high-demand fields, such as medical devices and aerospace, metal filter meshes require extremely high precision and consistency. These fields commonly use high-precision microporous filter meshes, which have more stringent manufacturing requirements, with pore sizes usually at the micron level. Traditional punching and stretching processes cannot meet these precision demands, necessitating the use of advanced photochemical etching technology.
TMN’s photochemical etching manufacturing technology ensures that all metal filter meshes have extremely high pore size accuracy and consistency. It also guarantees the dimensional precision and material properties of the filter meshes, significantly enhancing their performance and promoting technological advancement and application expansion in related fields.
Note: Learn more about our metal filter mesh etching services
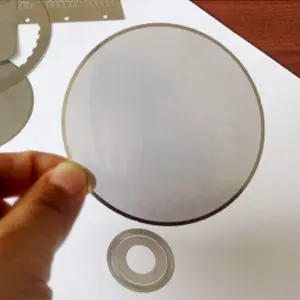
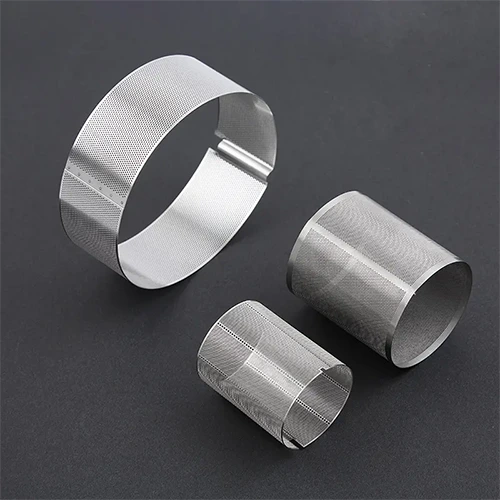
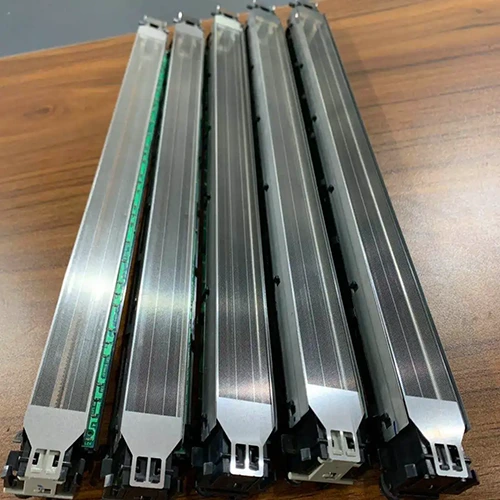
Fuel Cell Bipolar Plate
The bipolar plate is a key component in fuel cells, responsible for current conduction, gas distribution, and water management. It has been widely applied in automotive, stationary power generation, and portable power sources. However, achieving large-scale commercialization requires continuous optimization and improvement by researchers. By enhancing the conductivity, corrosion resistance, and mechanical strength of bipolar plates, and further improving the precision and consistency of the manufacturing process, the performance and lifespan of fuel cells can be significantly improved. Photochemical etching shows great potential in these aspects, providing strong support for the further development of fuel cell technology.
TMN’s photochemical etching process can achieve high-precision and complex microstructure processing (e.g., double-depth channels on the same side), forming complex flow channels and gas distribution networks on the surface of the bipolar plate. This ensures the uniform distribution of fuel and oxidant within the cell. Additionally, TMN offers complex surface coatings (plating platinum on one side and MMO on the other), laser welding, diffusion bonding, and other secondary processing techniques.
Note: Learn more about our Fuel Cell Bipolar Plate etching services
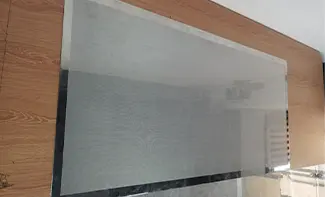

Speaker Grille
Metal speaker grilles play an important role in modern audio equipment, not only protecting the speaker units from external damage but also contributing to aesthetics and acoustic performance. Ordinary speaker grilles are mainly used in home and car audio systems, requiring a certain level of strength and rigidity while ensuring uniform grille openings to guarantee even sound distribution and unaffected sound quality.
In high-end audio equipment, professional audio, and stage sound systems, the requirements for metal speaker grilles are more stringent. Besides protective functions, they also need to consider acoustic transparency, interference resistance, and aesthetics, which traditional processes can hardly meet.
Photochemical etching enables high-precision processing, creating intricate and complex patterns and uniform micro-perforations. This not only enhances acoustic performance but also imparts unique aesthetic effects to the products.
Note: Learn more about our Speaker Grille etching services
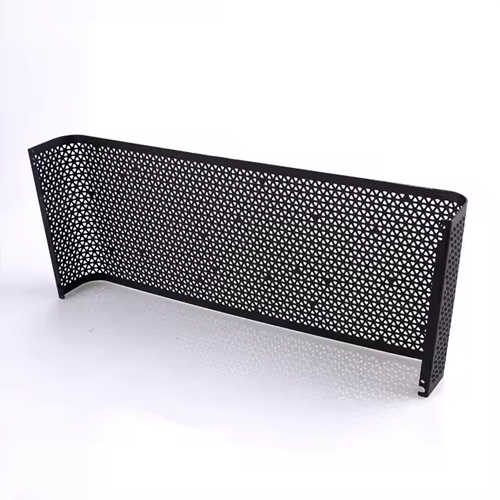
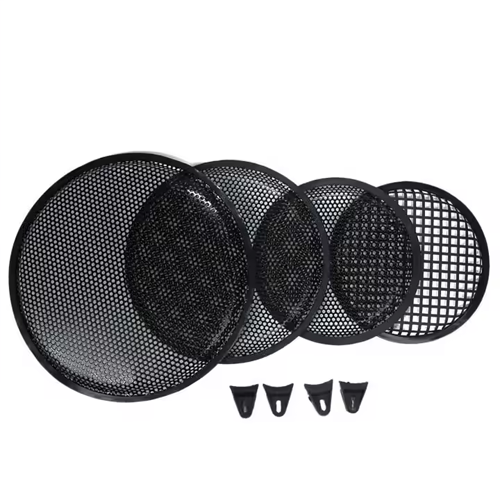
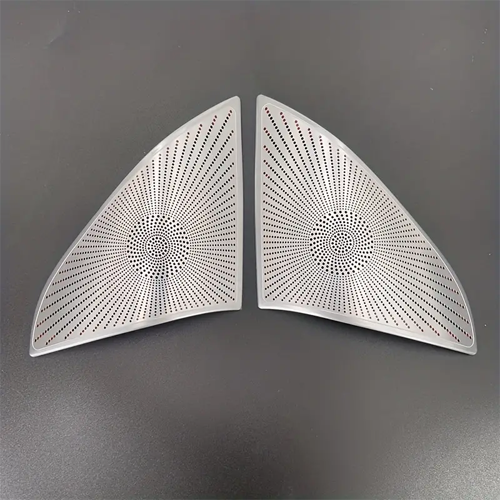
Vapor Chamber
The Vapor Chamber (VC Heat Sink) is an advanced thermal management solution widely used in electronic devices such as computers, phones, and tablets to improve their heat dissipation performance. The Vapor Chamber uses the principle of phase change through liquid evaporation and condensation to rapidly transfer heat from high-temperature areas to low-temperature areas, effectively reducing the operating temperature of the device. Compared to traditional heat pipe cooling, the Vapor Chamber offers higher thermal conductivity and more uniform heat distribution.
The manufacturing process of Vapor Chambers requires extremely high standards. First, the selection of suitable materials is crucial to ensure good thermal conductivity and mechanical strength. Secondly, the internal structure design is essential, requiring precise machining techniques to create internal microporous structures that ensure rapid evaporation and condensation of the liquid inside.
TMN’s photochemical etching process perfectly meets the high manufacturing requirements of Vapor Chambers, effectively ensuring the quality and performance of each Vapor Chamber.
Note: Learn more about our Vapor Chamber etching services
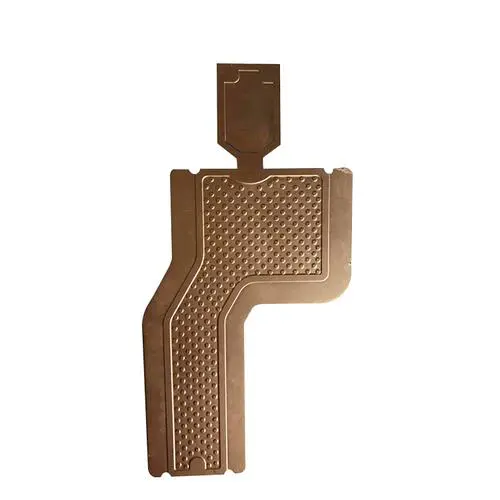
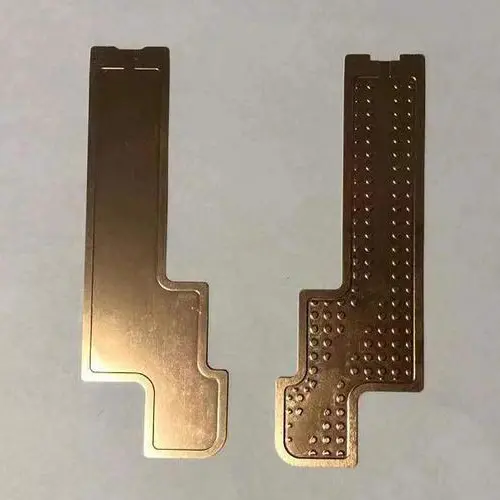
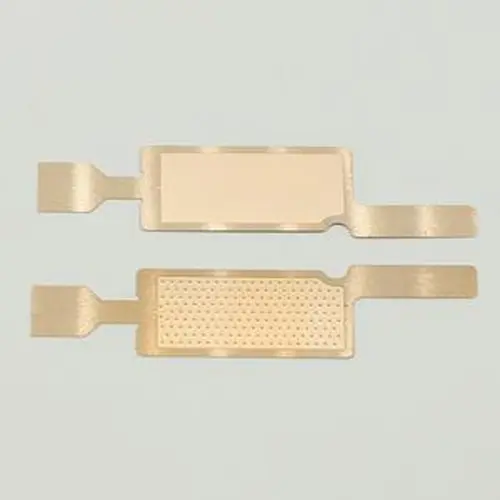
Nameplates/Doorplates/Signs
The production processes for metal nameplates, doorplates, and signs vary depending on their use and design requirements. For metal nameplates/doorplates used for identification and decoration, the process must ensure a smooth surface, clear text, and patterns, as well as good weather resistance and corrosion resistance. High-end metal nameplates and signs used for commercial displays and public places require processes that can accurately depict complex patterns and fine text.
From ordinary metal nameplates and doorplates to high-end signs, photochemical etching not only allows precise control over etching depth and pattern details but also creates clear and durable markings without damaging the metal material.
Note: Learn more about our Nameplates/Doorplates/Signs etching services
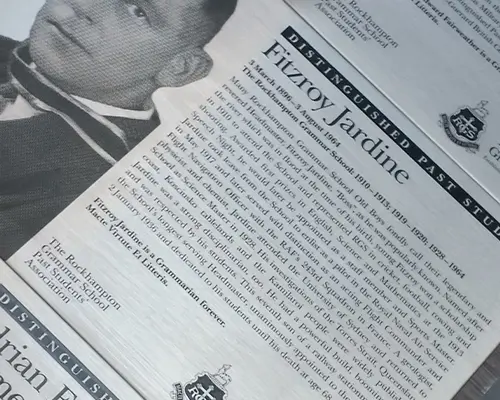
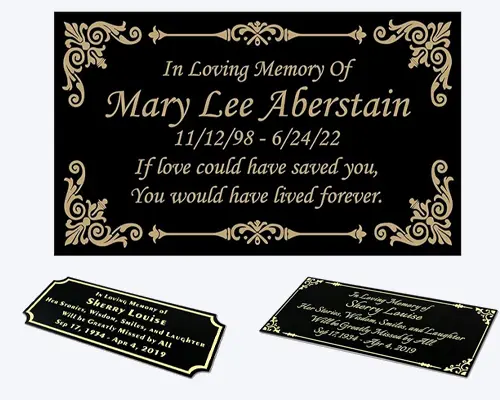
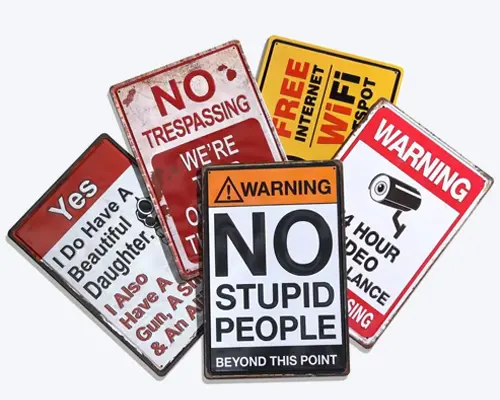
3D Metal Jigsaw Puzzles
3D metal jigsaw puzzles are products created by processing individual components on one or more metal sheets, which are then assembled to form a three-dimensional model. These puzzles are widely used in education, entertainment, and decoration. They not only help users develop hands-on skills and spatial thinking but also have ornamental and collectible value. The design and production of 3D metal jigsaw puzzles require highly precise craftsmanship to ensure that each part can be accurately assembled.
To ensure that each part can be accurately assembled, the production of 3D metal jigsaw puzzles must meet strict technical requirements. Each component must be precise to ensure seamless assembly. TMN’s photochemical etching process can achieve micron-level precision, creating intricate and complex puzzle pieces while preserving the original strength and toughness of the material. This makes 3D metal jigsaw puzzles not only more aesthetically complex in design but also more precise and reliable in actual assembly, providing users with a better experience.
Note: Learn more about our 3D Metal Jigsaw Puzzles etching services
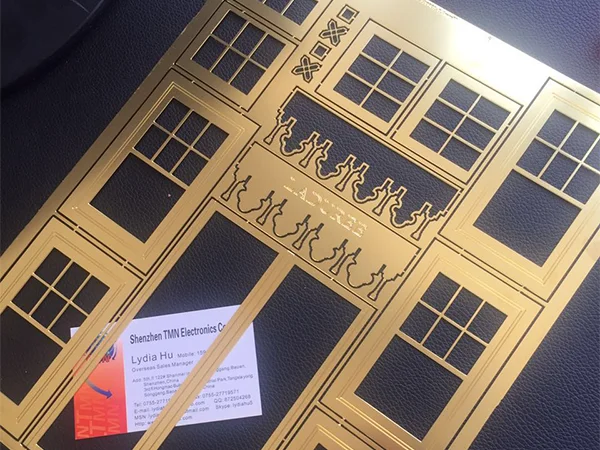
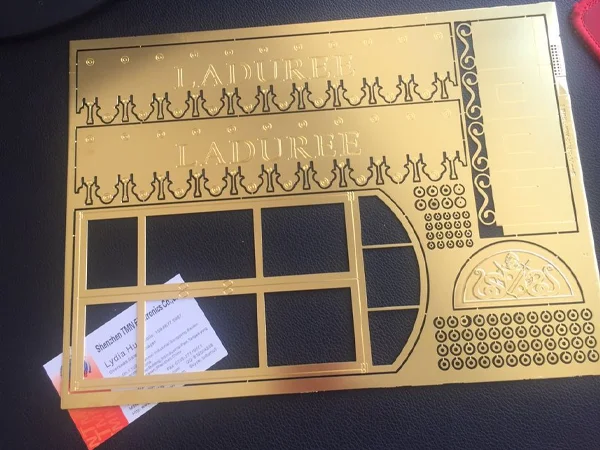
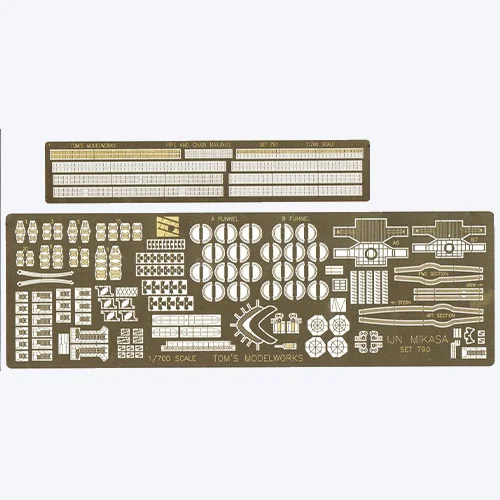
EMI & RFI Shielding
EMI & RFI shielding is a key component used to protect electronic devices from electromagnetic interference (EMI) and radio frequency interference (RFI). These shields are widely used in various electronic devices and systems, including communication equipment, computers, medical instruments, and aerospace equipment. They effectively prevent external electromagnetic waves from interfering with the internal circuits of the device, and also prevent the device itself from emitting electromagnetic radiation that could affect surrounding electronic devices. Therefore, EMI & RFI shielding typically requires metal materials with good conductivity and magnetic permeability (such as copper, aluminum, and nickel alloys) to effectively shield electromagnetic waves while also having good mechanical strength and corrosion resistance.
In terms of materials, TMN’s large warehouse covers hundreds of metal materials. In metal processing, photochemical etching provides an efficient, precise, and flexible solution for the manufacture of EMI & RFI shielding, significantly improving product performance and reliability. Additionally, TMN offers extra metal surface treatments, such as electroplating, painting, and oxidation, to enhance the anti-oxidation capabilities of the shielding covers and extend their service life.
Note: Learn more about our EMI/RFI Shielding etching services
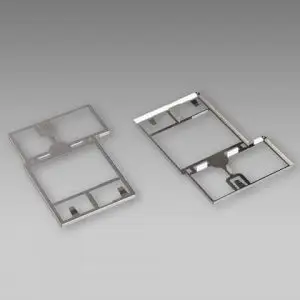
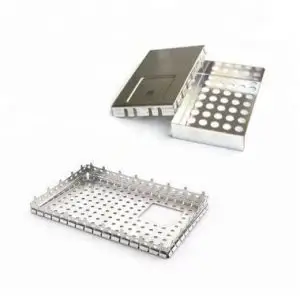
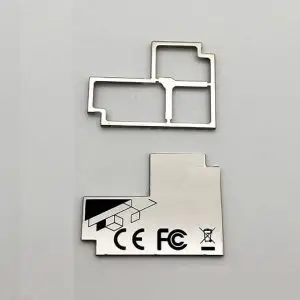
Lead Frame
A lead frame is a crucial component of integrated circuit (IC) packaging, connecting the chip to external circuits and ensuring the stable transmission of electrical signals. Lead frames are widely used in the semiconductor industry, especially in computers, communication devices, automotive electronics, and consumer electronics. They need to have excellent conductivity and maintain stability under high temperatures and mechanical stress.
The manufacturing process for lead frames is very stringent. First, material selection is critical, typically using conductive materials such as copper alloys, stainless steel, and aluminum to ensure stable signal transmission and high conductivity. Secondly, high-precision manufacturing processes are required to ensure the dimensional accuracy and conductivity of the lead frames.
TMN’s photochemical etching process offers significant advantages in manufacturing lead frames. It can achieve nano-level processing precision, allowing for the creation of complex geometries to meet various design requirements. It is cost-effective, can quickly respond to market demands and design changes, and shortens production cycles.
Note: Learn more about our Lead Frame etching services
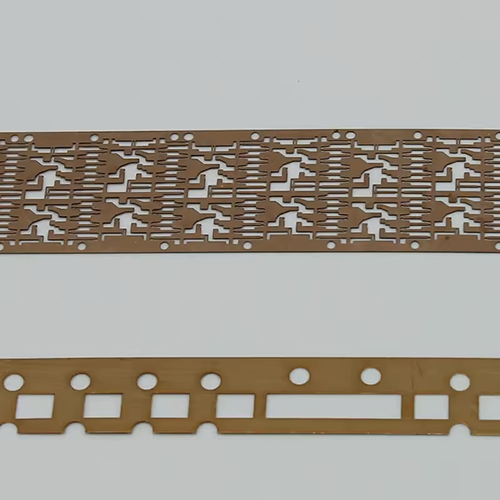
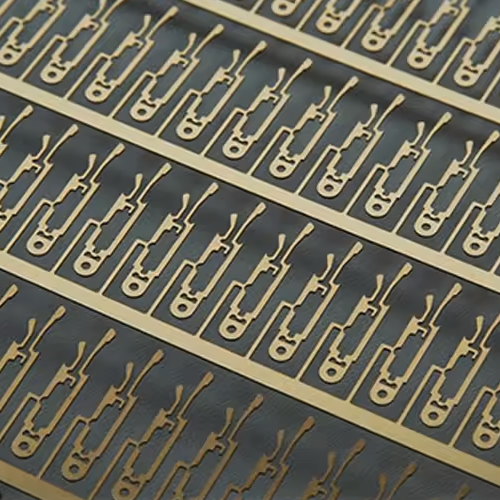
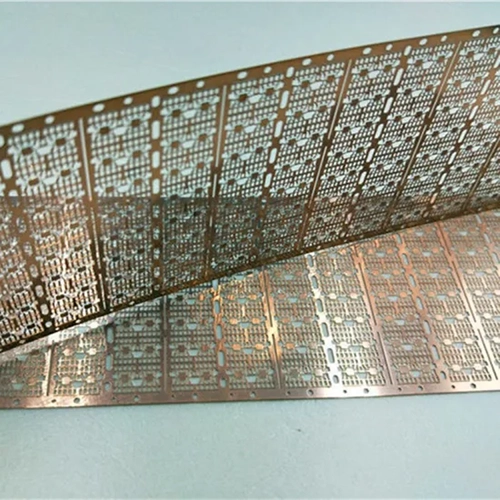
Metal Gaskets/Washers
Metal gaskets and washers are common fastening and sealing components in mechanical and electronic equipment, used to prevent leaks, reduce vibrations, and distribute pressure to prevent damage due to stress concentration. They are widely used in automotive, aerospace, medical, and industrial equipment.
Manufacturing metal gaskets and washers also requires strict process standards. Material selection is critical, with common materials including stainless steel, copper, aluminum, and alloys. These materials need to have high-temperature resistance, corrosion resistance, and high strength. Precision manufacturing processes, such as TMN’s photochemical etching, ensure the dimensional accuracy and surface smoothness of gaskets and washers. Additionally, surface treatments like electroplating, painting, or heat treatment are provided to enhance the durability and corrosion resistance of gaskets and washers, making them suitable for various harsh working environments.
Note: Learn more about our Metal Gaskets/Washers etching services
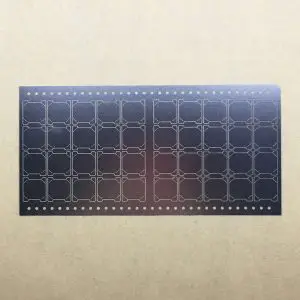
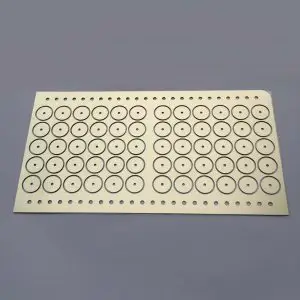
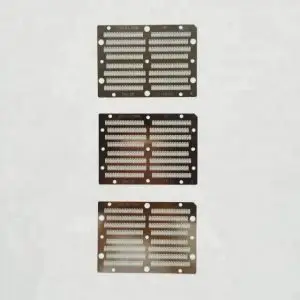
Encoding Disk
An encoding disk is a precision component used for data encoding and decoding, widely applied in secure communication, data storage, and authentication. It encrypts and decrypts data through the rotation or movement of specific encoding disks, ensuring the security and confidentiality of information transmission. Encoding disks are particularly important in military, financial, and high-security data storage systems, effectively preventing unauthorized access and data breaches.
Due to its specialized application, the manufacturing of encoding disks requires extremely high precision and complex processing techniques. Photochemical etching provides an efficient, precise, and flexible solution for the production of encoding disks, significantly enhancing the performance and reliability of the products. Encoding disks produced using this process offer better protection for sensitive information, ensuring security and reliability across various application scenarios.
Note: Learn more about our Encoding Disk etching services
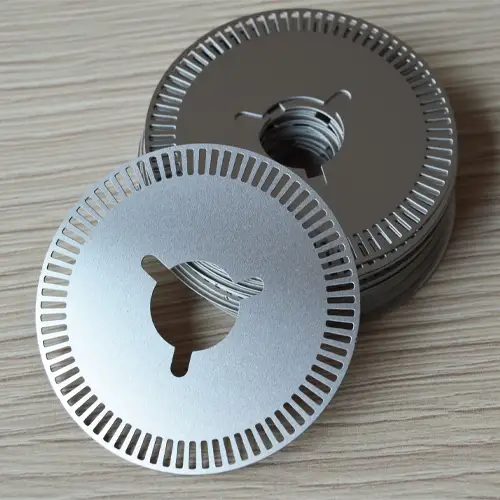
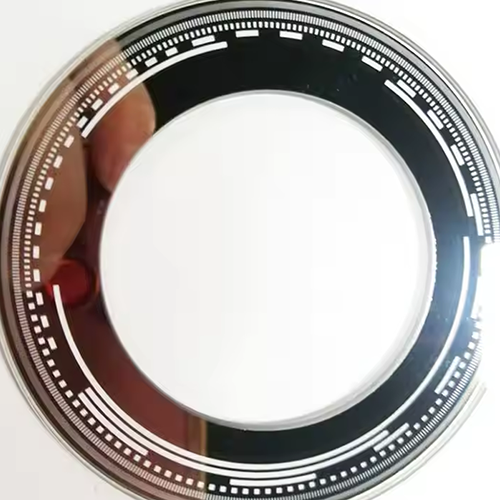
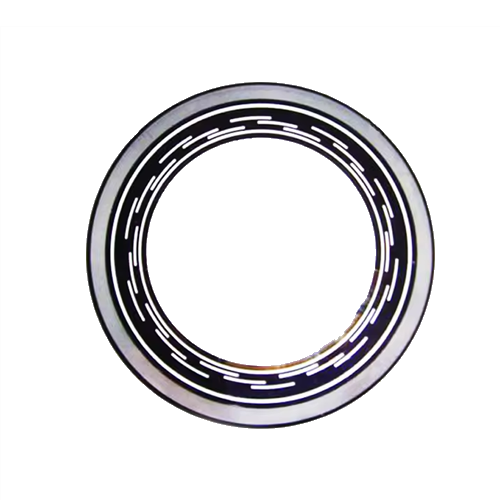
Summary
The examples provided illustrate the custom products TMN has manufactured over the past decade using photochemical etching technology, showcasing the broad applicability and excellent performance of photochemical etching across various fields. With our technological advantages and extensive experience, TMN can offer customers a one-stop service from design to production, ensuring that each component meets the highest quality standards.
Whether for startups or large enterprises, TMN is committed to continuously innovating and optimizing manufacturing processes to meet the demands for high-precision, complex structures, and reliable components. We believe that through close collaboration and technology sharing with our clients, we can jointly drive technological advancement and development across industries.
If you have any needs for metal etching, you can easily contact us by phone, WeChat and WhatsApp at +8613603056883; for inquiries, please email lydia.sales1@tmnetch.com.
Note: Learn more about TMN’s metal etching process technology
Related articles:
Stainless Steel Etching Process: How to Choose Stainless Steel Etching
Copper Etching: Reasons for using photo etching for copper metal
Etching Aluminum: The Most Cost-Effective High-Precision Process