Photochemical Etching
Photochemical etching, also referred to as chemical milling, stands out as a precise and adaptable technique essential for economically manufacturing intricate metal components. It involves the selective etching of metal using corrosive chemicals, thereby removing unwanted metal from the sheet while retaining the desired part shape.
Page wizard
Photochemical Etching specialists
TMN is one of the leading Photoc Etching companies in China. For over ten years, we have focused on developing groundbreaking metal etching technology. So far, we have provided service to customers from different fields worldwide.
TMN also has a lot of experience in import and export trade, allowing us to efficiently arrange delivery and prepare documents for customs clearance, import inspections, and COC certificates.
Photochemical Etching processing range
Photo-chemical etching has a very wide range of applications, covering products such as, but not limited to, semiconductors, precision medical devices, decorative art pieces, luxury goods, and automotive parts.
As specialists in the field, TMN has already produced excellent parts for customers from many different industries.
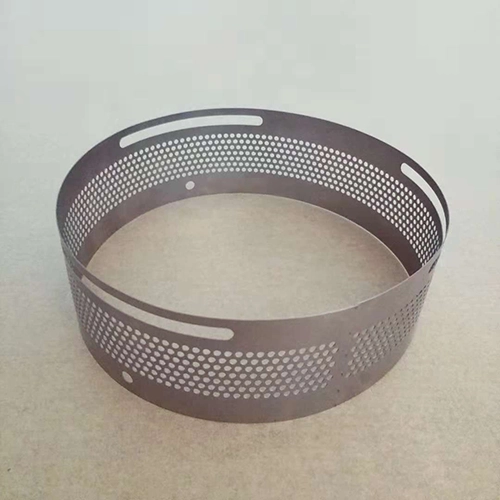
smoke alarm bug screen
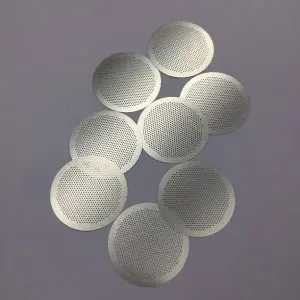
stainless steel mesh
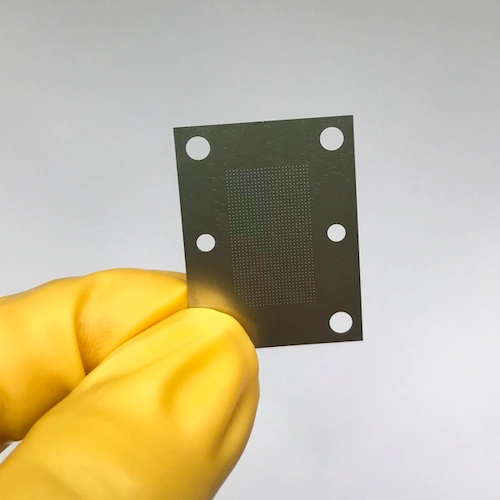
micro mesh
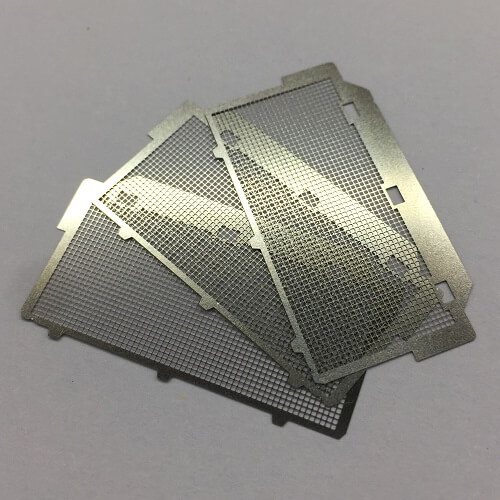
perforated plate
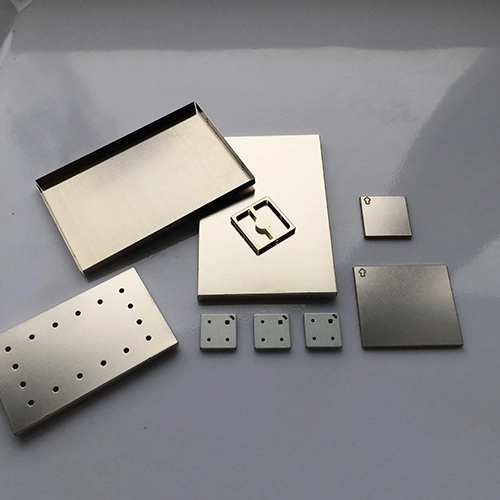
wifi internet shield
Advantages of Photochemical Etching
Photochemical Etching technology offers benefits like burr-free results, super-fast and low-cost design iterations, and no need for expensive mold-making, which traditional sheet metal machining technology cannot achieve. In addition to these technological advantages, TMN has the following features that make us more specialized than most chemical etching companies.

Industry and trade integration

Multiple metal types

Rapid production within 3 days

24 hours online

Advanced etching equipment
Comprehensive range of materials
The photochemical etching process can etching almost any metal, regardless of its hardness or shape. As the business has grown, TMN has its own large warehouse, which stores metal raw materials of varying thickness, from 0.01mm to 2.0mm. Once we confirm the product details with our clients, we can quickly start machining the raw materials and create a product prototype within 6 hours.
Photochemical Etching Machining Process
Photochemical Etching is a process that uses ultraviolet light to expose metal materials, causing a chemical reaction to remove material from specific areas. TMN has its own advanced machining production line, allowing us to control the entire process from material selection to final product inspection. This ensures we maintain high efficiency and quality during machining.
TMN have 4 full automatic etching machines with 20 meters long ,and some other supportive automatic production equipments ,such as coating machines ,explosure machines,developinng machines ,19 sets in total.
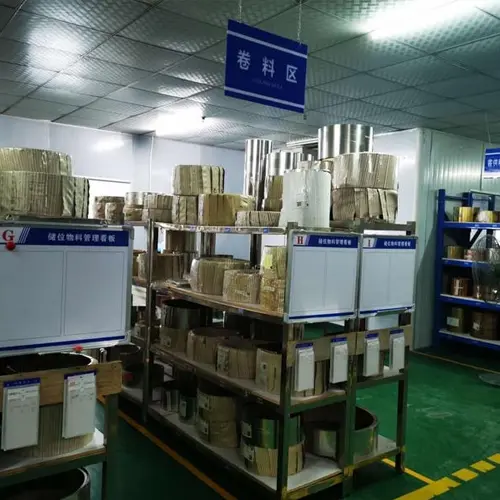
Metal prep
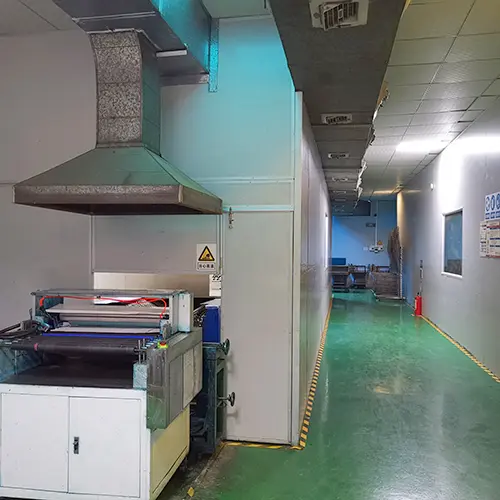
Glue plating/Exposure

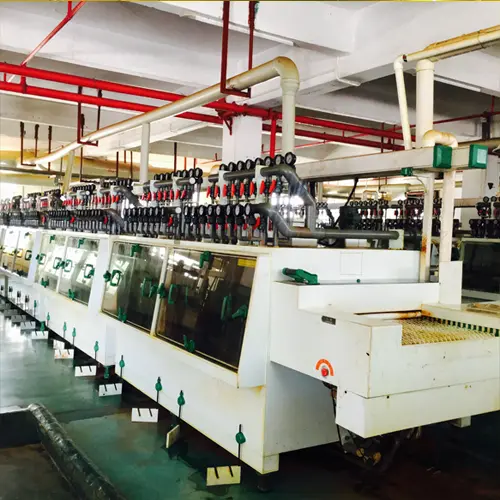
Develop/Etching
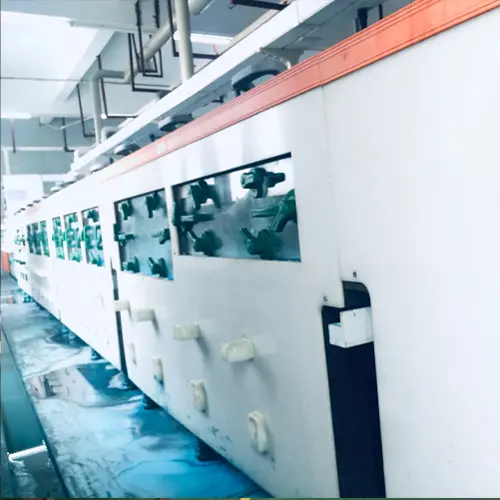
Degumming / Cleaning
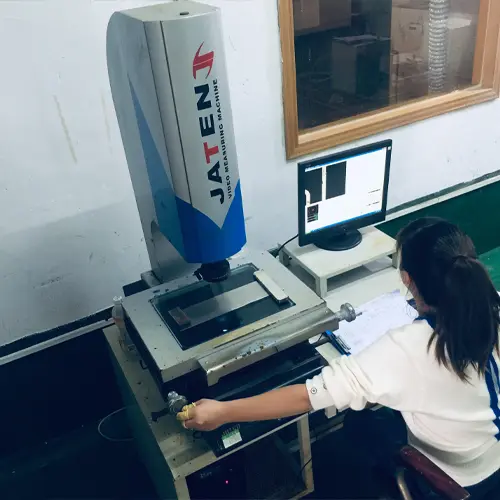
FQC/OQC
Samples of TMN etched
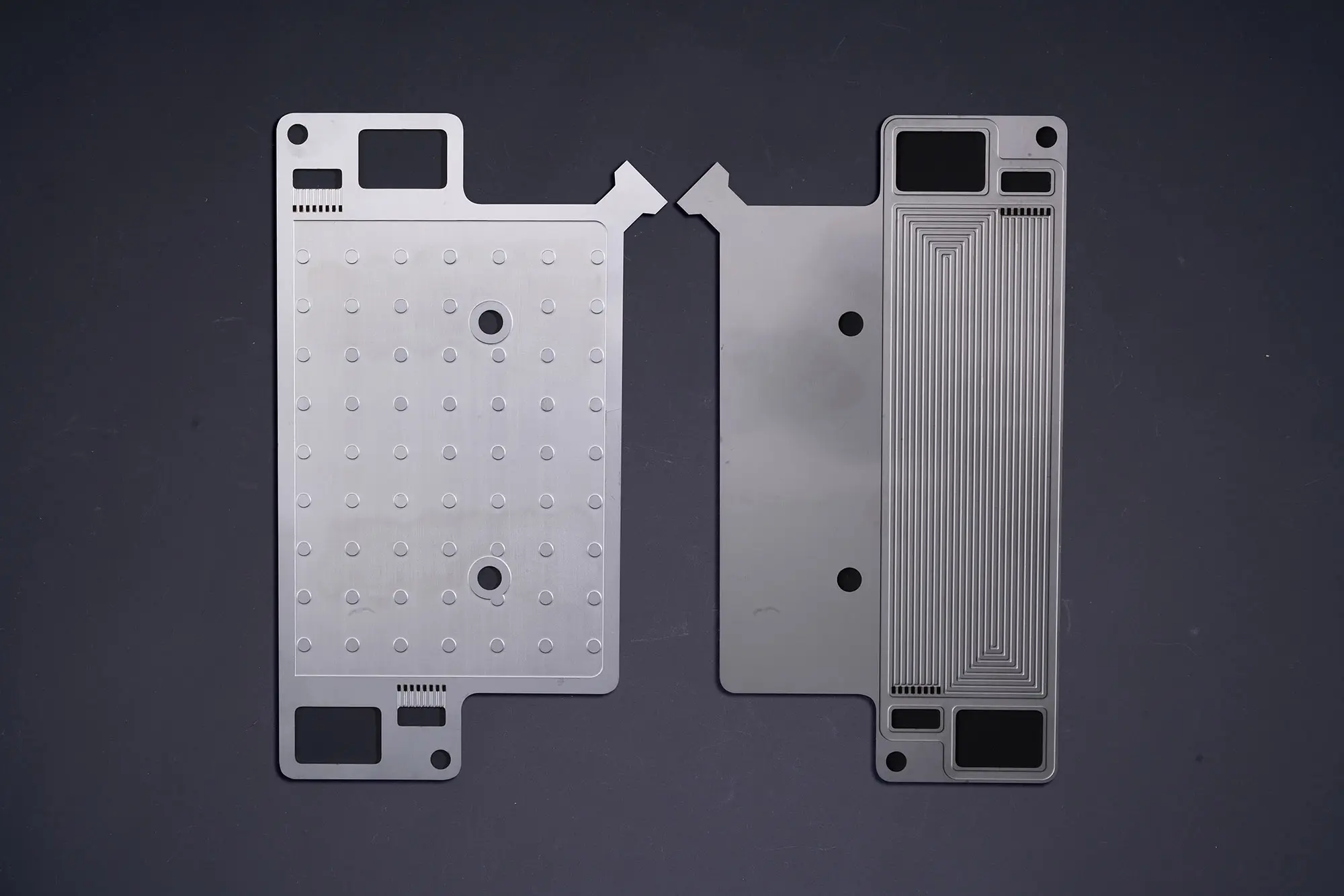
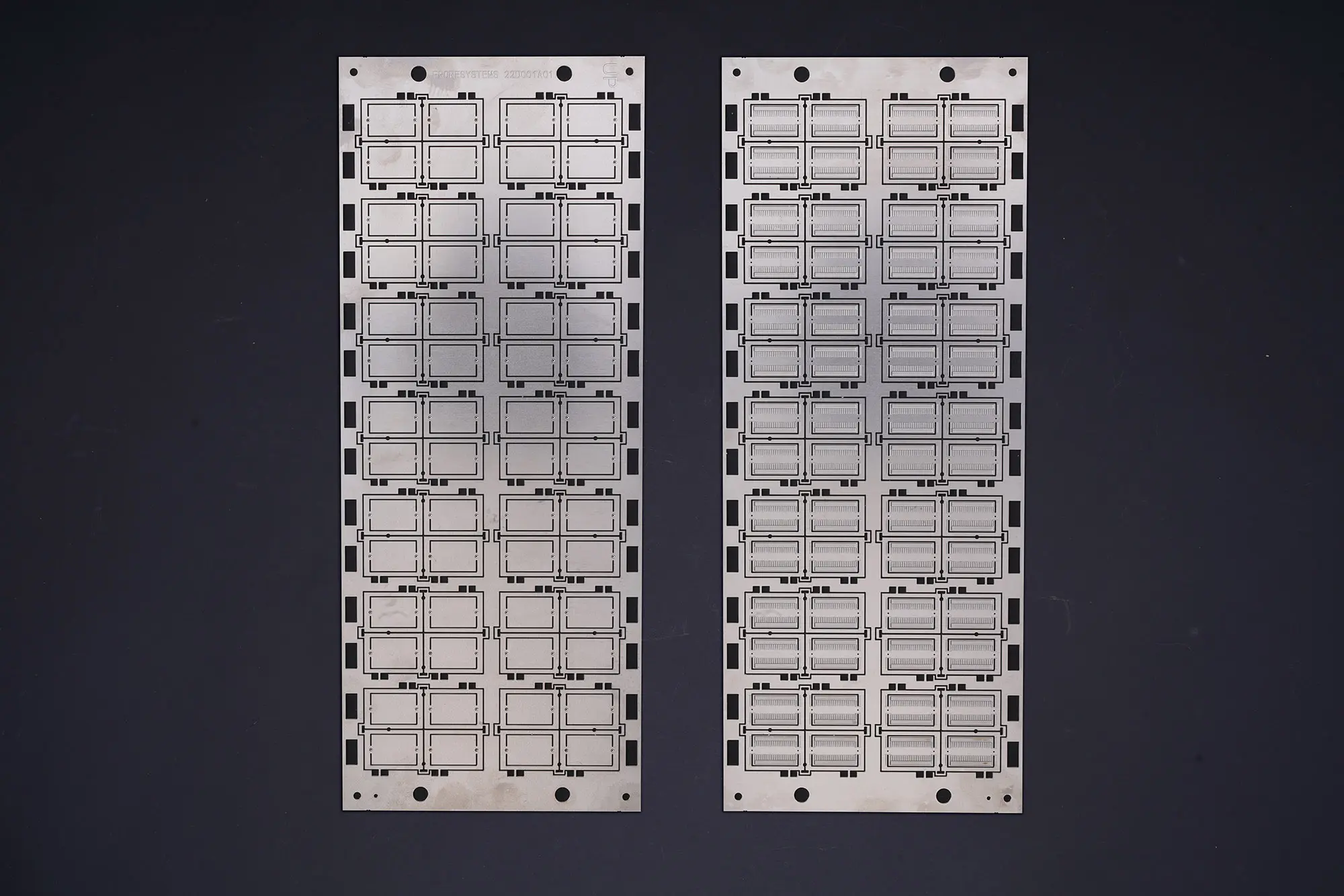
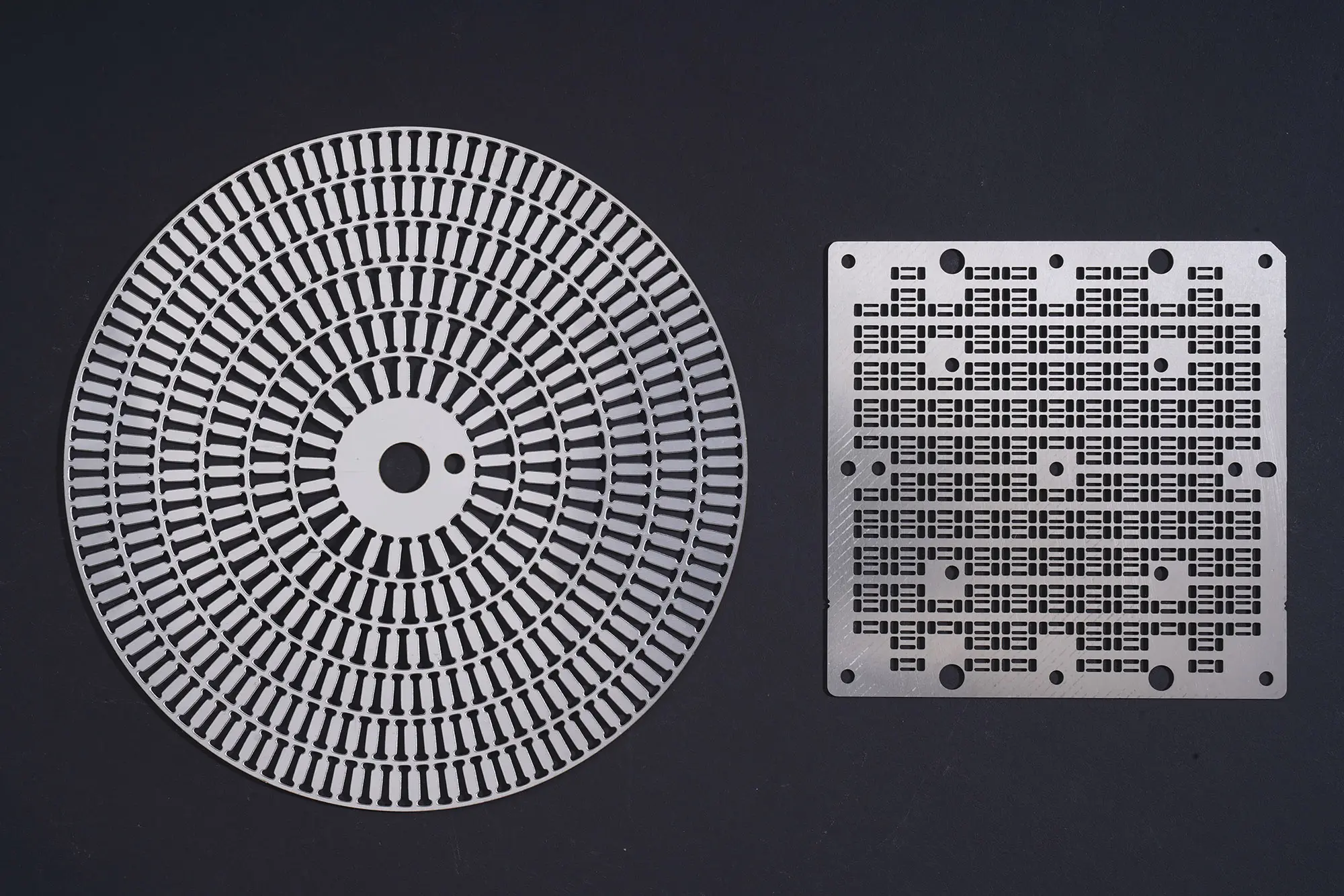
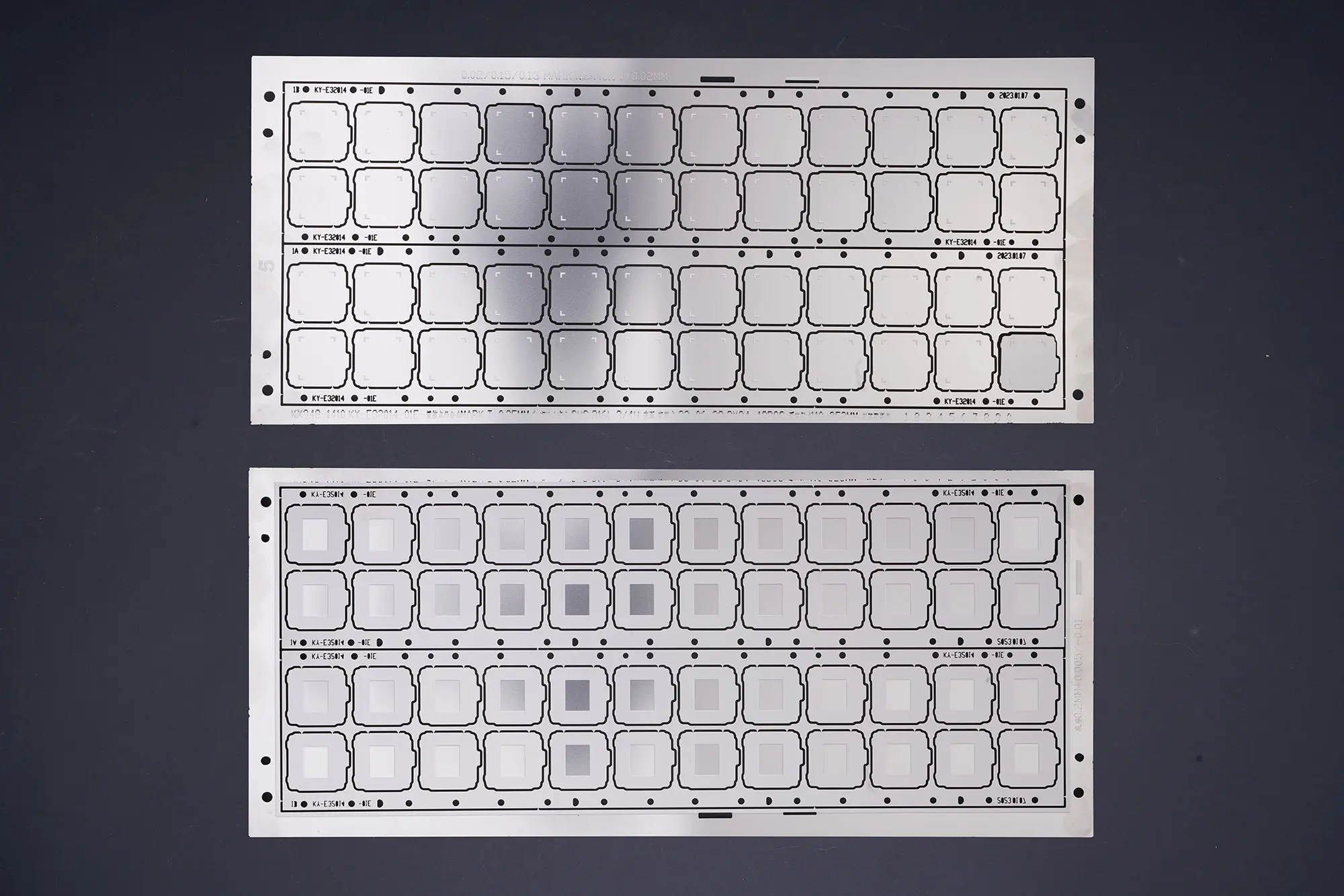
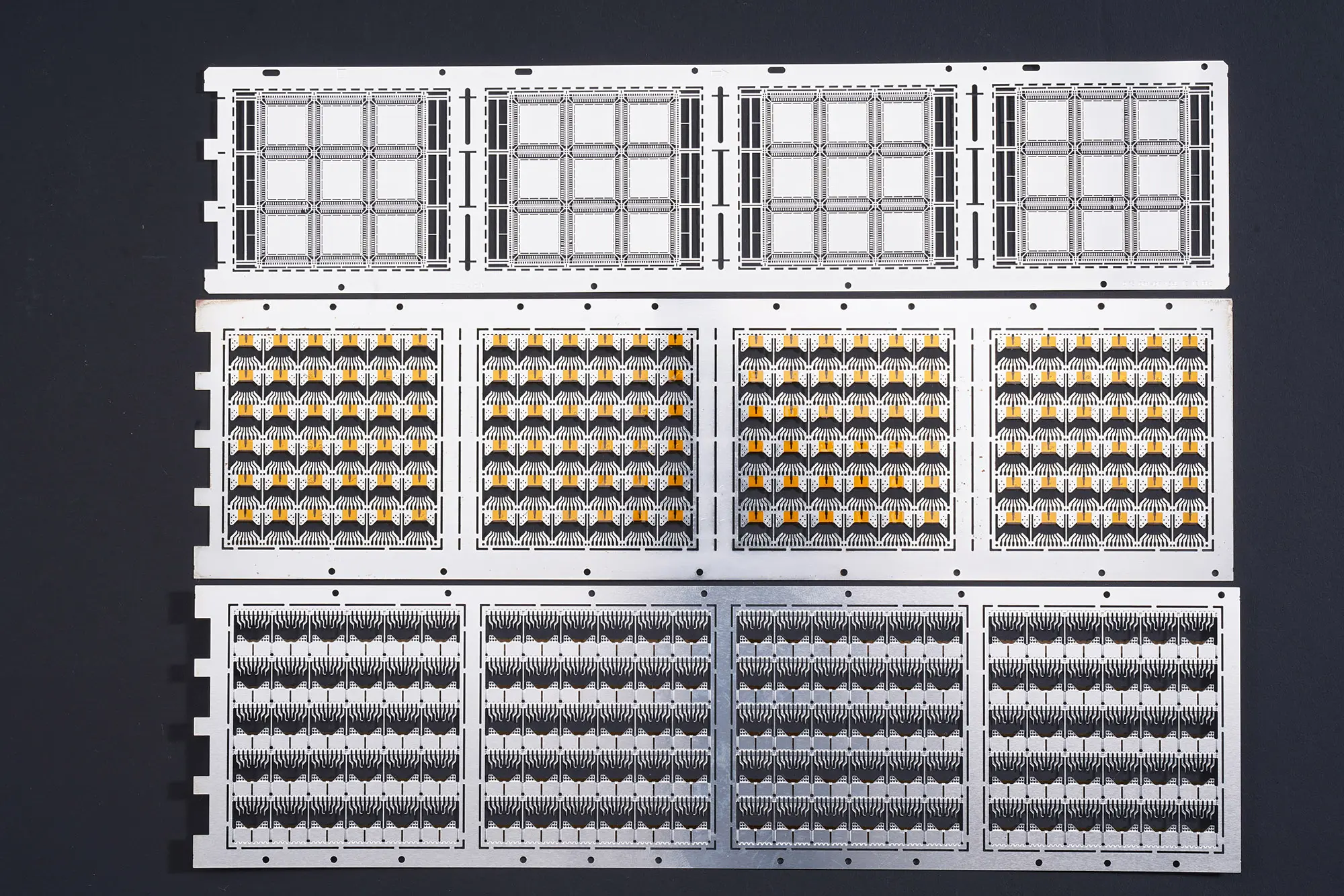
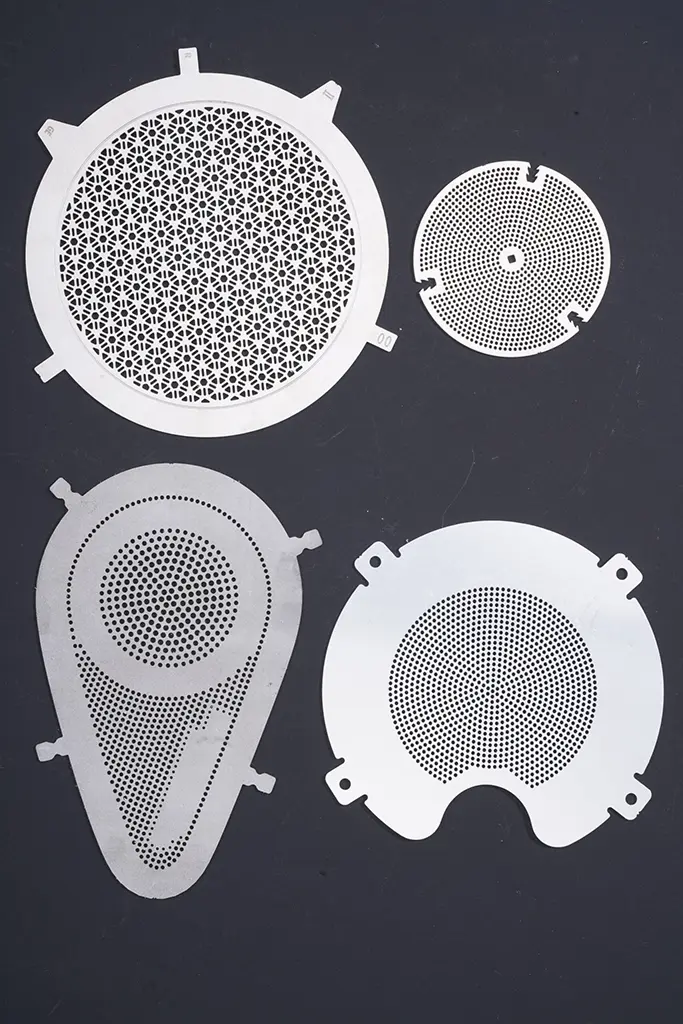
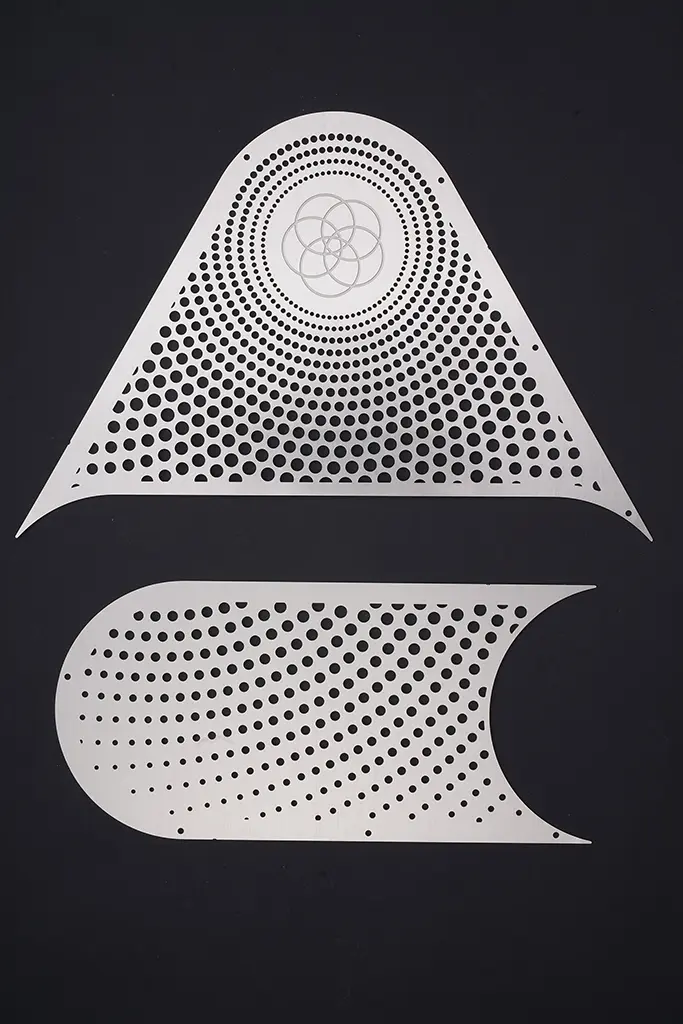
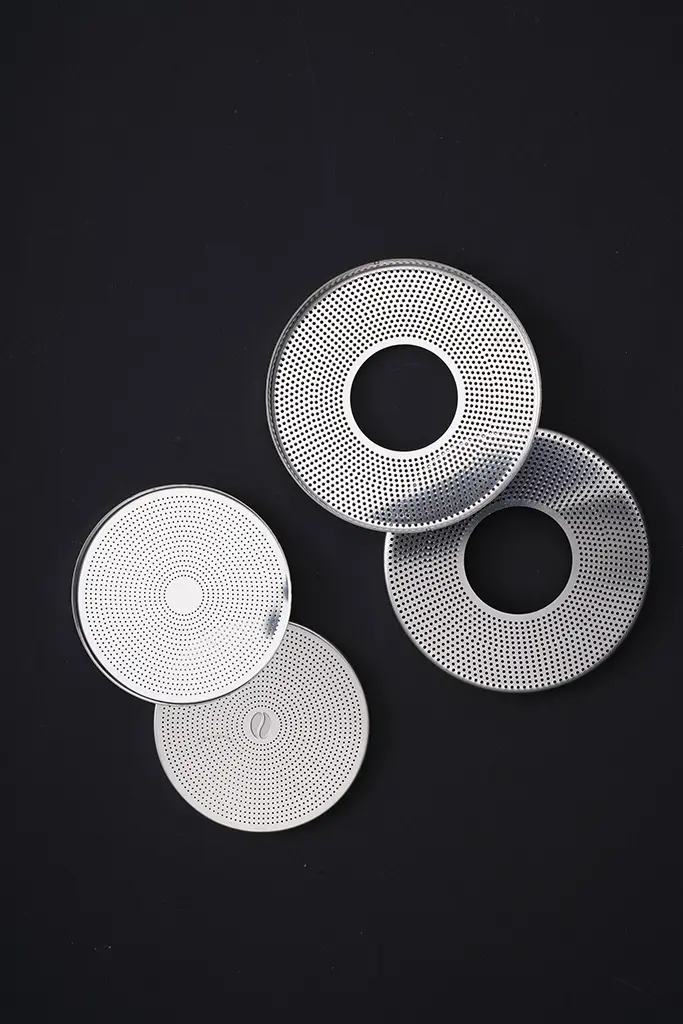
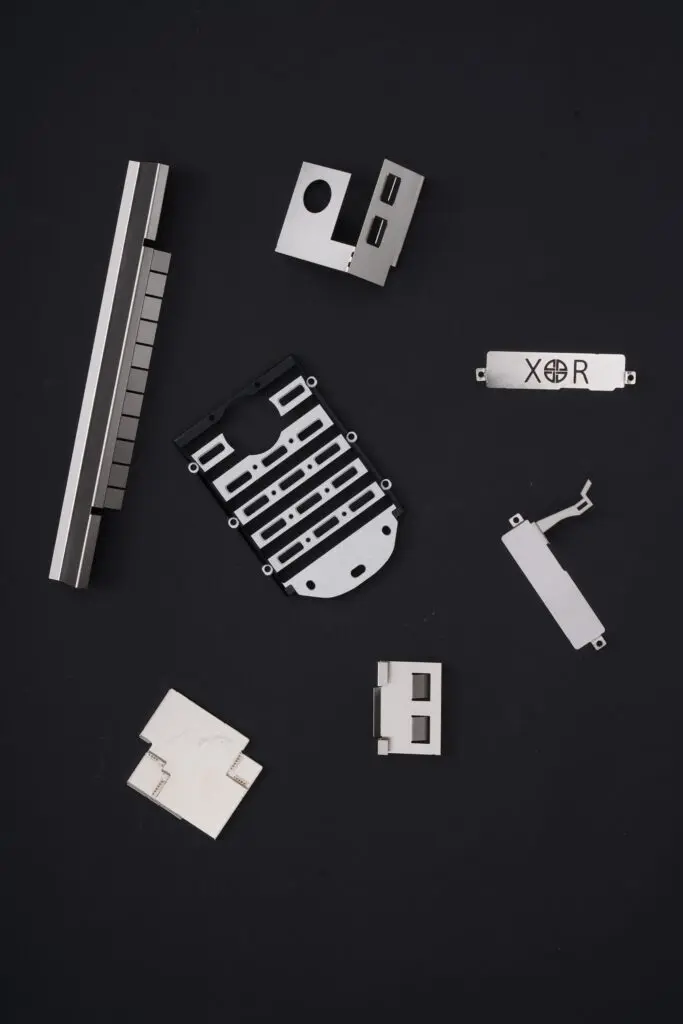
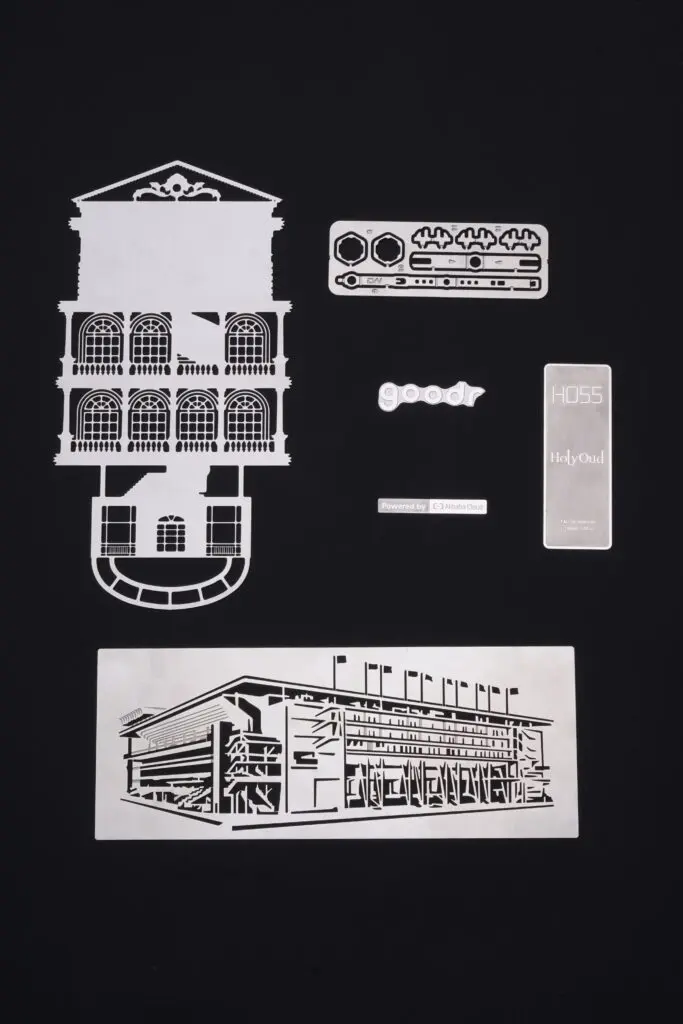
Photochemical Etching FAQs
What is the maximum/minimum size for parts suitable for photochemical etching?
The range of part thickness it can handle is typically between 0.01mm and 2.5mm, with outer dimensions up to 600*1500mm. Within this range, parts can be machined with high precision, allowing for complex shapes and detailed features through the photo-chemical etching process.
How precise is photochemical etching?
It depends on several factors, including the chemical solvent used, the etching time, the temperature, and the precision of the photosensitive pattern. Generally, the standard minimum etching tolerance is ±10% of the etched metal's thickness, but it can be as low as ±0.025 millimeters.
How many days does photochemical etching take to complete?
Photochemical etching is relatively fast and usually can be completed in a few days, unlike traditional machining methods which might take weeks or even months.
TMN can quickly produce complex components for your next project in just 3 days.
What are the Two Main Types of Etching?
1. Wet Etching: Also known as photochemical etching, wet etching refers to the process of dissolving the metal surface by exposing it to a chemical solution after removing the metal etch protective film. This forms precise patterns. With continuous innovations in process equipment technology, wet etching has expanded into the aerospace, mechanical, and chemical industries, as well as semiconductor manufacturing processes, the production of precision metal etched products, and thin electronic components.
2. Dry Etching: Dry etching mainly includes plasma etching and chemical etching. Its etching effect depends on the interaction between ions in the plasma or chemicals and the surface atoms of the material to be etched. Dry etching is an anisotropic etching process with good directionality but poorer selectivity compared to wet etching. Its main advantage is the ability to etch in specific directions. However, dry etching has relatively low selectivity due to its physical interactions, where ion impacts can remove the etching film and potentially affect the stability of the photoresist mask.
What Can I Use to Etch Metal?
In metal etching and cleaning processes, various chemical solutions are used. Here are four common chemical solutions:
1. Phosphoric Acid: The industry commonly uses phosphoric acid at a concentration of 86%, with process temperatures ranging from 150-180°C. Phosphoric acid provides a uniform etching effect and is relatively simple to operate, often used in precision manufacturing and surface treatment.
2. Ferric Chloride: Ferric chloride is commonly used for etching copper and stainless steel. It offers a fast etching speed and high solution stability. To achieve the best etching results with ferric chloride, it's essential to control the concentration and temperature of the solution.
3. Nitric Acid: Nitric acid is a strong acid typically used for etching stainless steel, copper, aluminum, and other metals. Due to its high corrosiveness, nitric acid etches very quickly and can easily lead to over-etching. Therefore, strict control of etching time is required, along with proper safety precautions.
4. Hydrofluoric Acid: Hydrofluoric acid is a highly corrosive acid mainly used for etching silicon, glass, and titanium materials. It provides excellent etching results but is highly dangerous, requiring strict adherence to safety protocols during handling.
What is the Difference Between Etching and Engraving Metal?
Metal Etching is a chemical process, whereas engraving metal is a physical carving process. This is the fundamental difference between the two techniques. Additionally, in terms of production, etching is suitable for mass production, intricate patterns, and complex designs. Engraving, on the other hand, is typically used to achieve deeper grooves and three-dimensional effects, but it may not be as precise as etching for very fine details.
In terms of efficiency, etching is more suited for large-scale production and is more efficient. Engraving, especially hand engraving, tends to be less efficient and more costly.
Is Metal Etching Cheaper than Engraving?
The cost difference between metal etching and engraving depends on various practical factors, including the project scale, materials, and the level of detail required. Generally speaking, metal etching tends to be cheaper, especially when using wet etching methods, which can be automated and are suitable for mass production. However, for small quantities and less detailed products, engraving might be a good choice.
Send us a message