Résumé : Le développement des piles à combustible à membrane échangeuse de protons (PEMFC) montre un grand potentiel pour devenir une source d’énergie propre, efficace et fiable. Les plaques bipolaires, l’un des composants clés des PEMFC, jouent un rôle crucial en fournissant des connexions électriques, en distribuant les gaz réactifs, en dissipant la chaleur de réaction et en éliminant les sous-produits. Cependant, elles représentent également une part significative du coût global des PEMFC.
Selon le matériau utilisé pour les plaques bipolaires, elles peuvent être classées en métalliques, en graphite et en composites. Cet article passe en revue les différents matériaux des plaques bipolaires et leurs processus de fabrication. Parmi ceux-ci, les plaques bipolaires métalliques attirent l’attention dans les applications de véhicules de tourisme en raison de leurs propriétés mécaniques et physiques supérieures, ainsi que de leur avantage de coût par rapport aux matériaux en graphite poreux et en composites. Cependant, les principales préoccupations pour les plaques bipolaires métalliques sont leur processus de fabrication et leur résistance à la corrosion.
À l’avenir, le développement de revêtements avancés résistants à la corrosion et conducteurs, ou de matériaux métalliques innovants pour les plaques bipolaires, améliorera considérablement l’adoption des PEMFC dans les véhicules de tourisme.
En raison de contraintes de durabilité et de coût, les piles à combustible à membrane échangeuse de protons (PEMFC) n’ont pas encore atteint une application commerciale à grande échelle, les plaques bipolaires étant l’un des composants critiques limitant leur faisabilité. En général, les plaques bipolaires représentent plus de 80 % de la masse totale de la pile, environ 30 % du coût total et occupent la majeure partie du volume de la pile.
En termes de structure, les plaques bipolaires dans une pile à combustible remplissent six fonctions fondamentales :
1. Séparer les cellules individuelles au sein de la pile ;
2. Distribuer les gaz réactifs ;
3. Fournir des connexions électriques ;
4. Éliminer les sous-produits aqueux ;
5. Dissiper la chaleur de réaction ;
6. Résister aux forces de serrage.
Pour répondre à ces exigences fonctionnelles, le Département de l’Énergie des États-Unis (DOE) a fixé des objectifs spécifiques pour les caractéristiques des plaques bipolaires pour les années 2020 et 2025, comme indiqué dans le Tableau 1. Selon la dernière feuille de route du Fuel Cell Technologies Office, le coût actuel des plaques bipolaires est d’environ 5,4 $ par kW, dépassant largement l’objectif du DOE de 2025 fixé à 2,0 $ par kW. Cela indique que pour atteindre les objectifs du DOE, les matériaux des plaques bipolaires doivent devenir plus abordables tout en maintenant une haute conductivité électrique et thermique, une faible résistance de contact et une bonne résistance à la corrosion.
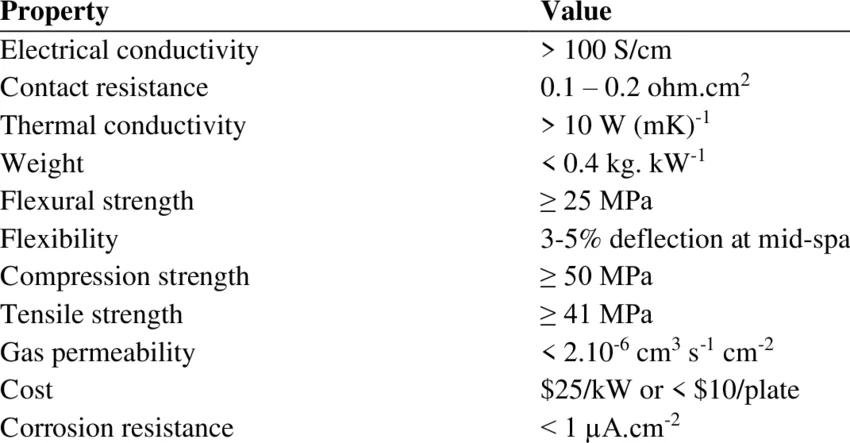
Les plaques bipolaires peuvent être catégorisées en métalliques, en graphite et en composites en fonction des matériaux utilisés. En Chine, les plaques bipolaires en graphite sont actuellement les plus couramment utilisées dans les piles à combustible à membrane échangeuse de protons (PEMFC). Cependant, les plaques bipolaires métalliques attirent l’attention en raison de leur potentiel de réduction significative des coûts avec la production à grande échelle et de leur compacité, en particulier dans les piles à haute puissance, par rapport aux plaques en graphite. En revanche, les plaques bipolaires composites sont en voie de disparition en raison des défis de production de masse et des coûts élevés.
Cet article fournit une revue complète des plaques bipolaires en graphite, métalliques et composites, discutant de leurs caractéristiques, processus de fabrication et méthodes de préparation. Il explore également les différents revêtements utilisés pour les plaques bipolaires métalliques. Enfin, l’article présente les applications des piles à combustible basées sur ces différents types de plaques bipolaires.
Plaques bipolaires en graphite
Le graphite est actuellement le matériau prédominant utilisé pour les plaques bipolaires en Chine en raison de sa haute conductivité électrique, de sa stabilité chimique, de sa stabilité thermique et de sa résistance à la corrosion. Cependant, en tant que matériau poreux et fragile, le graphite présente une faible résistance et une grande fragilité, ce qui rend difficile de répondre aux exigences d’étanchéité des plaques bipolaires. Pour surmonter ces limitations, le graphite doit subir plusieurs cycles d’imprégnation et de carbonisation pour créer des plaques de graphite non poreux.
Les plaques de graphite non poreux sont généralement fabriquées en graphitisant de la poudre de carbone/graphite et de la résine à des températures élevées (environ 2 500 °C). Ce processus nécessite un programme de montée en température précis, entraînant un cycle de production long et des coûts élevés. De plus, le processus de graphitisation peut entraîner une nouvelle porosité en raison de l’évaporation des impuretés, ce qui peut se traduire par un taux de porosité de 20 % à 30 % sur la surface des plaques de graphite. La présence de pores augmente le risque de fuites dans les PEMFC, ce qui peut réduire la concentration des gaz réactifs et, par conséquent, diminuer les performances de la pile. Pour atténuer ces risques, les plaques de graphite sont imprégnées pour réduire la porosité et améliorer la qualité de surface. Une solution largement utilisée est la plaque de graphite non poreux imprégnée de manière répétée.
La Figure 1 illustre une comparaison des courbes de densité de courant (J) et de tension (U) dans une pile à combustible avant et après imprégnation. Il est évident que les performances de la pile sont significativement améliorées lorsqu’elle est assemblée avec des plaques bipolaires en graphite imprégnées.
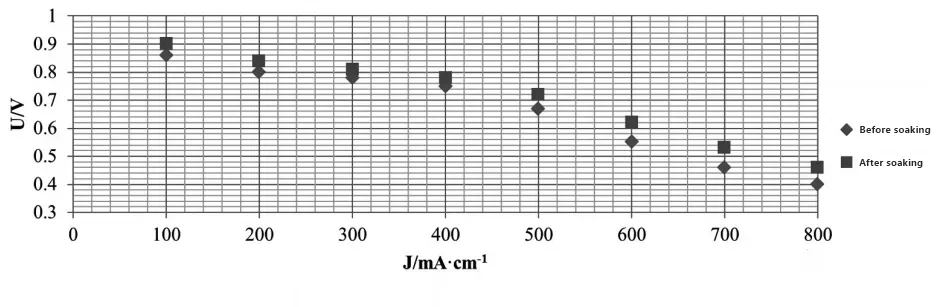
Plaques de graphite usinées
Les plaques de graphite usinées sont généralement produites par traitement mécanique du graphite synthétique. Le processus de fabrication implique les étapes clés suivantes :
1. Préparation des matières premières : Le coke et le brai sont mélangés et carbonisés à une température comprise entre 1 000 et 1 300 °C pour former du matériau carboné. Ce matériau est ensuite imprégné de brai et cuit, suivi de la graphitisation dans un four électrique à des températures allant de 2 500 à 3 000 °C.
2. Découpage : Le matériau brut de graphite est grossièrement découpé en plaques selon les dimensions requises pour les plaques bipolaires.
3. Imprégnation : Les plaques de graphite découpées sont imprégnées de résine pour remplir les pores de surface et internes. Typiquement, les plaques sont immergées dans la résine pendant environ 24 heures, suivies d’un traitement thermique pour solidifier la résine. Selon le type de résine utilisé, ce processus peut être divisé en imprégnation de résine phénolique et imprégnation de résine alcool furfurylique, entre autres.
4. Meulage : Après découpe et imprégnation, les plaques de graphite nécessitent un meulage pour atteindre la douceur souhaitée. Cela implique un meulage grossier, moyen et fin pour garantir les dimensions correctes et la qualité de surface.
5. Gravure/Usinage : Cette étape est cruciale dans le traitement des plaques bipolaires. La précision du processus de gravure ou d’usinage détermine les tolérances dimensionnelles et la qualité des canaux de flux sur les plaques.
En raison de la faible résistance et de la fragilité du graphite, cette méthode de traitement n’est pas idéale pour la production de plaques bipolaires ultra-fines (moins de 1,5 mm). De plus, une friction excessive entre les outils et le graphite peut entraîner une précision dimensionnelle et une qualité de surface sous-optimales. Pendant le processus d’usinage, le graphite peut se fracturer en petites particules et en fines poussières, exposant les outils de coupe à des contraintes d’impact et de compression élevées. La nécessité d’usiner des canaux de flux complexes ajoute encore au coût global. En conséquence, cette méthode est progressivement abandonnée dans de nombreux pays, où la plupart des fabricants utilisent désormais le moulage par injection ou le moulage par compression pour la production.
Plaques de graphite moulées par injection
Les plaques de graphite moulées par injection sont produites en mélangeant une proportion spécifique de graphite avec de la résine. Ce mélange est alimenté dans la trémie d’une machine de moulage par injection, où il est chauffé et fondu. Le mélange fondu est ensuite injecté dans un moule fermé sous pression, et après refroidissement et solidification, le produit est retiré du moule. Pour augmenter la conductivité électrique de ces plaques bipolaires, des poudres métalliques peuvent être ajoutées au mélange, et des fibres de carbone ou des fibres céramiques peuvent être utilisées pour améliorer la résistance mécanique. Cependant, le moulage par injection présente plusieurs inconvénients, tels que des temps de déliement prolongés (jusqu’à 7 jours), des fissures dans les sections épaisses, des limitations de taille et des défauts. Une graphitisation supplémentaire peut améliorer les performances des plaques, mais cela augmente considérablement le coût, rendant cette méthode moins adaptée à la production à grande échelle.
Plaques de graphite moulées par compression
Pour réduire les coûts de traitement et améliorer la capacité d’extension, les chercheurs se sont tournés vers le moulage par compression pour la production de plaques bipolaires. Ce processus commence par la préparation d’un mélange de poudre de graphite et de résine, suivi d’un prétraitement du mélange et du moule. En utilisant une température et une pression spécifiques, la poudre est fondue et se répand dans toute la cavité du moule, assurant une couverture complète. La plaque bipolaire est retirée du moule après durcissement. Si le liant est un plastique thermodurcissable, il faut généralement quelques minutes pour durcir avant le démoulage. Si un liant thermoplastique est utilisé, le moule doit être refroidi en dessous du point de fusion du liant avant le démoulage.
Dans l’ensemble, la demande du marché pour les plaques bipolaires en graphite reste élevée, mais des problèmes de porosité, de coûts et de longs délais de traitement nécessitent encore des améliorations. De plus, pour réduire la résistance au courant et à la conduction thermique, les plaques bipolaires doivent être aussi fines que possible tout en maintenant une résistance mécanique adéquate et une bonne barrière aux gaz. Compte tenu de l’utilisation actuelle des véhicules à pile à combustible à hydrogène en Chine, les véhicules commerciaux tels que les bus, les camions de logistique, les véhicules de nettoyage et les chariots élévateurs sont les principaux marchés cibles. L’utilisation fréquente de ces véhicules commerciaux exige une plus grande durabilité de leurs composants, faisant des plaques bipolaires en graphite un choix adapté pour les applications de piles à combustible. Les plaques de graphite sont appréciées pour leur longue durée de vie, ce qui en fait une option privilégiée pour les véhicules commerciaux à pile à combustible dans les opérations de démonstration.
Shanghai Hongfeng, une entreprise chinoise, a développé des plaques bipolaires en graphite d’une épaisseur de seulement 1,4 mm tout en maintenant les performances, atteignant des niveaux de densité de puissance approchant ceux des premières plaques bipolaires métalliques de Toyota.
Plaque bipolaire en métal
Comparées aux plaques bipolaires en graphite, les plaques bipolaires métalliques gagnent en popularité en raison de leur excellente conductivité électrique et thermique, leur aptitude à l’usinage, leur processus de fabrication moins complexe et leur potentiel à produire des plaques bipolaires ultra-minces. De plus, les processus de production en masse sont bien établis, permettant des réductions de coûts significatives grâce à la fabrication à grande échelle. Jusqu’à présent, l’acier inoxydable, les alliages d’aluminium, les alliages de titane, les alliages de nickel, les alliages de cuivre et les composites à matrice métallique ont été utilisés dans la production de plaques bipolaires métalliques. Cependant, les plaques métalliques sont sujettes à la corrosion, nécessitant des revêtements protecteurs de surface.
Processus de gravure sur métal, d’emboutissage et de formage hydraulique
Gravure sur métal
La gravure sur métal implique l’utilisation de produits chimiques pour enlever des zones spécifiques d’une plaque métallique, créant des motifs et des caractéristiques précis. Ce processus est couramment utilisé pour sa haute précision et sa capacité à produire des conceptions complexes. Les principaux avantages incluent :
Haute Précision : La gravure sur métal permet un détail très fin, ce qui la rend idéale pour les géométries complexes et les champs d’écoulement intricats.
Aucun Stress Mécanique : Étant un processus sans contact, il y a une distorsion ou un stress minimal sur la plaque métallique, assurant une précision dimensionnelle.
Flexibilité : Il est facile de changer de design sans nécessiter de modifications importantes des outils, offrant une flexibilité pour le prototypage et les petites séries de production.
Emboutissage
L’emboutissage utilise une matrice et une presse pour façonner le métal dans les formes souhaitées. Cette méthode est reconnue pour son efficacité et son coût-avantage dans la production à grande échelle. L’emboutissage est généralement choisi pour :
Vitesse de Production Élevée : L’emboutissage est un processus rapide, ce qui le rend adapté à la fabrication en grand volume.
Coût-Efficacité : Une fois la matrice créée, le coût par unité diminue considérablement, ce qui en fait une méthode préférée pour la production de masse.
Cohérence : L’emboutissage assure l’uniformité à travers de grandes quantités, maintenant une qualité et des tolérances constantes.
Processus de Formage Hydraulique
Le formage hydraulique utilise la pression hydraulique pour façonner les plaques métalliques, généralement en les pressant contre une forme ou une matrice. Cette méthode est appréciée pour sa capacité à créer des formes complexes et des contours profonds. Les avantages du formage hydraulique incluent :
Polyvalence : Le formage hydraulique peut produire des géométries complexes et convient à une large gamme d’épaisseurs de métal.
Réduction des Coûts d’Outils : Comparé à l’emboutissage, le formage hydraulique nécessite souvent des outils moins complexes, ce qui peut conduire à des coûts de mise en place initiaux inférieurs.
Moins de Déchets de Matériaux : Ce processus peut être plus efficace en termes d’utilisation des matériaux, réduisant les déchets et les coûts globaux.
Revêtements pour Plaques Bipolaires Métalliques
Malgré les nombreux avantages des plaques bipolaires métalliques, elles sont plus sujettes à la corrosion, ce qui peut affecter négativement leur performance et leur durabilité. La corrosion des plaques bipolaires métalliques se produit parce qu’à l’anode, l’environnement réducteur peut réduire la couche d’oxyde métallique protectrice, formant des hydrures et provoquant la dissolution du métal dans l’eau. Ce processus permet au métal d’être transporté dans le flux de carburant, augmentant potentiellement le risque de contamination de la membrane échangeuse de protons et affectant négativement l’activité de la couche de catalyseur. À la cathode, l’environnement oxydant augmente considérablement le taux de corrosion, conduisant à une dégradation des performances et à une défaillance prématurée de la pile.
Toyota Motor Corporation a été pionnière dans l’utilisation de plaques bipolaires métalliques avec des revêtements protecteurs dans son véhicule à pile à combustible Mirai, résolvant divers problèmes tels que la corrosion, le coût et la conductivité. Les revêtements utilisés sur les plaques bipolaires métalliques peuvent être largement catégorisés en deux types :
1. Revêtements à base de Carbone : Cela inclut les revêtements de graphite.
2. Revêtements à base de Métal : Cela comprend les revêtements de métaux précieux, les carbures métalliques, les nitrures métalliques et les oxydes métalliques.
Plusieurs routes de processus sont utilisées pour appliquer ces revêtements, y compris l’électroplacage, le placage chimique (tel que le placage à chaud, le revêtement par pulvérisation), le dépôt chimique en phase vapeur (CVD) et le dépôt physique en phase vapeur (PVD). En Chine, le PVD est couramment utilisé pour les revêtements de plaques bipolaires métalliques en raison de sa haute pureté, de sa bonne densité, de sa forte adhérence avec le substrat et de son insensibilité au matériau de base, ce qui en fait une technique de modification de surface préférée.
Plaques bipolaires composites
Les plaques bipolaires composites combinent les avantages des plaques en graphite et en métal, offrant une faible densité, une résistance à la corrosion et une facilité de moulage. Cependant, elles rencontrent des défis liés aux longs temps de traitement et à une fiabilité à long terme limitée, ce qui affecte leur adoption généralisée. Les plaques bipolaires composites peuvent être divisées en deux types : les plaques bipolaires composites structurelles et les plaques bipolaires composites basées sur les matériaux.
Plaques bipolaires composites structurelles
Les plaques bipolaires composites structurelles utilisent des plaques minces en métal ou d’autres plaques conductrices à haute résistance et haute densité comme séparateurs, avec des plaques minces en carbone poreux ou un treillis métallique comme plaques de champ d’écoulement, liées avec des adhésifs conducteurs. Cette structure composite combine les forces des plaques en métal et en graphite : les plaques en métal fournissent résistance et durabilité, tandis que les plaques en graphite créent des canaux d’écoulement sans nécessiter de haute densité ou de renforcement. L’inclusion de graphite réduit également l’exposition directe du métal aux environnements corrosifs, atténuant les risques de corrosion. Cependant, le processus de production est complexe et l’étanchéité est relativement plus difficile.
Plaques bipolaires composites basées sur les matériaux
Les plaques bipolaires composites basées sur les matériaux sont principalement formées en mélangeant de la poudre de graphite/fibres renforcées avec une résine thermoplastique ou thermodurcissable pour créer une préforme, qui est ensuite durcie ou graphitisée. Les plaques bipolaires composites peuvent être encore divisées en plaques bipolaires composites à base de carbone et en plaques bipolaires composites à base de métal. Le tableau 4 fournit une comparaison entre les plaques bipolaires composites à base de métal et celles à base de carbone.
Les plaques bipolaires composites à base de carbone peuvent ajuster la conductivité et la résistance mécanique en fonction du ratio de charges conductrices à la résine, permettant une production économique grâce au moulage par compression ou injection. Cette approche offre un potentiel considérable pour les applications futures. Les plaques bipolaires composites à base de métal utilisent généralement le métal comme séparateur, avec du plastique, du polycarbonate ou d’autres matériaux pour réduire le poids. Des adhésifs conducteurs lient le cadre en plastique au séparateur en métal, et des plaques minces en carbone poreux ou en graphite, produites par moulage par injection ou frittage, servent de plaques de champ d’écoulement.
Bien que les plaques bipolaires composites à base de métal combinent les avantages des plaques en graphite et en métal, leur structure complexe et leur processus de production rendent la production en masse difficile, avec des coûts nettement plus élevés que les plaques bipolaires composites à base de carbone. Cela limite leur adoption dans les applications PEMFC, mais elles offrent des avantages uniques dans des scénarios spécifiques où leur structure robuste et leur durabilité sont nécessaires.